目次
■スポット溶接とレーザー溶接の弱点を補完
●より高密度でより速い溶接が可能に
製造ラインの溶接工程では、スポット溶接を中心として、部位によっては補強の目的でアーク溶接やレーザー溶接を適用しています。
ボディの剛性を高めるために、トヨタが開発した溶接手法であるレーザー・スクリュー・ウェルディング(LSW)について、解説していきます。
●現行の溶接技術とその課題
スポット溶接は、従来からクルマのボディ溶接の主流として採用されています。溶接する2枚の鋼板を電極で挟み、通電して電気抵抗による発熱で鋼板を溶かして接合します。
課題は、点接合でしかも近接するスポット間の電流リークを避けるために、短いピッチで溶接ができないことです。結果として、十分な接合剛性を確保するのが難しくなります。
レーザー溶接は、レーザーを集光した熱で鋼板を溶かして溶接します。点ではなく、線溶接ができることが、最大の利点です。一方でスポット溶接とは異なり、鋼板を挟み込んで溶接しないため、鋼板間のわずかな隙間(板隙)によって品質が不安定になり、適用できる範囲が限定されるという課題があります。
以上の課題を踏まえ、現行のレーザー溶接は、強度が必要な箇所にスポット溶接した点と点の間を補強する形で使われるのが、一般的です。
●レーザー・スクリュー・ウェルディング(LSW)とは
LSWは、ロボットの先端に装着したレーザー発振器からレーザーを照射して、重ね合わせた鋼板を溶接する手法です。
従来は、スポット溶接の点と点の間に細い線を引くようにレーザー溶接を行い、補強していました。LSWは、線溶接ではなく、溶接の形を円形にして接合面積を広げました。スポット溶接の間に直径5mm程度の円形溶接部を数カ所設けます。
メリットは、次の通りです。
・密度の高い(スポット間隔が狭い)溶接による接合剛性の向上
・高速(スポット溶接の約3倍)の溶接による生産効率の向上
・片側からの溶接アクセスが可能なため、溶接自由度の向上(狭い部位や構造の溶接)
4代目新型プリウスに採用した例では、打点ポイント数を旧型車に比べて30%増やすことができ、ボディ剛性は60%向上しています。
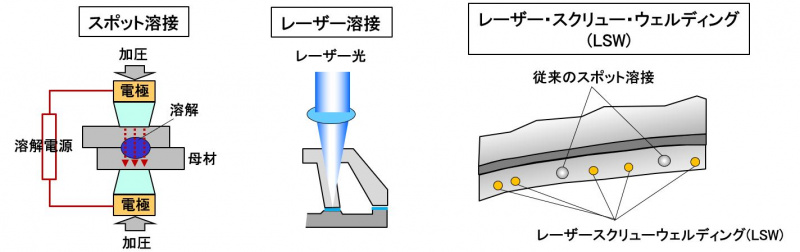
●クルマとしてのメリット
クルマにもたらすメリットとしては、大きくは2つあります。一つ目は、ボディ剛性の向上による走行性能の安定化です。
剛性が高いと、加減速時やコーナリング時のボディの捻じれが抑えられ、確実に駆動力を路面に伝えることができます。これにより、クルマの操縦安定性や乗り心地が向上し、さらに車体各部の歪みに起因する車体振動や騒音も低減できます。
二つ目は、軽量化です。接合剛性が向上すれば、補強材を減らす、構造を見直すことができ軽量化につながります。また、LSWは片側アクセスで溶接ができるので、スポット溶接に比べて接合配置の自由度が高くなります。骨格設計の制約が少なく、軽量化設計が容易になるメリットもあります。
レーザー・スクリュー・ウェルディング(LSW)は、スポット溶接とレーザー溶接の課題を克服し、両方の特徴を生かした技術です。最大の成果は、剛性や軽量化、生産性といった一見すると相いれない要求を同時に改良している点ではないでしょうか。
この技術を通して、優れたクルマづくりのためには、設計技術や開発技術だけでなく、生産技術の寄与も大きいことが分かります。
(Mr.ソラン)