目次
■輸送機器部品の量産品として世界初の採用
●原料は「木」です!
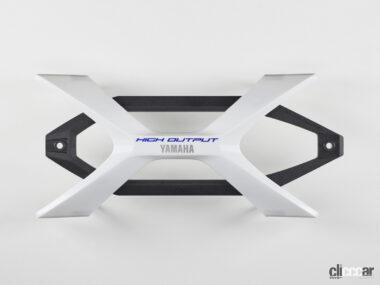
植物由来のセルロースを補強材として使った「セルロースナノファイバー強化樹脂」を、水上オートバイのエンジンカバーの材料として、ヤマハ発動機が開発し、北米で販売を開始しました。これはもちろん、温室効果ガス(CO2)の排出削減、環境負荷低減のための取り組みです。
輸送機器部品の量産品としては世界初の採用だという、このセルロースナノファイバーとは、どんな素材なのでしょうか? 量産化にはどのような努力があったのでしょうか? ヤマハ発動機マリン事業本部の開発スタッフおふたりに聞いてきました。
●パルプをナノレベルまで細かくして、補強材として使用
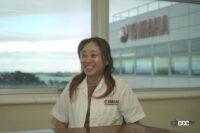
ヤマハ発動機が採用した新素材は、「セルロースナノファイバー強化樹脂」というプラスチックの一種です。プラスチックは、様々なものに使われていますが、単体では柔らかすぎたり壊れやすかったりするので、補強材を混ぜて強化プラスチックにして使うこともよくあります。ガラス繊維やカーボン繊維を補強材にしたFRP、CFRPなどが有名ですね。
今回紹介するこのセルロースナノファイバー強化樹脂は、木材から取り出したパルプを、ナノレベルまで解繊(繊維を解きほぐすこと)して作った「セルロースナノファイバー」(CNF)を補強材として使用したプラスチックです。
このCNF、どんなメリットがあるのでしょうか? ヤマハ発動機マリン事業本部の井上さんは「自然由来で、CO2を吸収している素材のため、環境にいいとか、高強度で繊維単体では鋼鉄の5倍の強度があるといわれています。あとは、水平リサイクルができます。弊社の実験としては、複数回リサイクルしても強度がほぼ変わらないという結果が出ています」といいます。
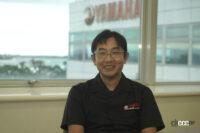
ただセルロースの繊維を使うというだけでなく、それをナノレベルまで細かくするというのには理由があります。
まず「繊維がダマになると、やっぱりそこから割れやすくなるんです。繊維が太ければ太いほど重なりとかが生じやすいので、そうならないようにナノまで解繊されたものを綺麗に分散させて、網目状にすることで強度を高めることができます」と、同じくヤマハ発動機マリン事業本部の益子さんはいいます。
今回、CNF強化樹脂が採用されたのは、エンジンカバーの部分ですが、この部品には以前はタルク(鉱物の一種)を補強材としてポリプロピレンに混ぜた強化樹脂が使われていました。その素材に対して、CNF強化樹脂は同等の強度と比重の低減により、なんと25%以上の軽量化が図れるのだそうです。ちなみに、強度がそれほど求められないような製品に関しては、ナノレベルまでは解繊していないセルロースファイバーを使うのも選択肢のひとつで、ヤマハ発動機ではまだ使っていませんが、世の中には出てきているようです。
●同じ強度のプラスチックとしてリサイクルできる
もうひとつの注目ポイントは、強化樹脂なのに“水平リサイクル”ができるということです。これは補強材を混ぜた強化樹脂では非常に難しいとされていて、例えばガラス繊維を使った強化プラスチック(GFPP=ガラス繊維強化プロピレンなど)の場合は、リサイクルする際にいちど粉砕すると、繊維が短くなってしまいます。そのため、再生しても同じ強度のものは作れないんだそうです。
そこでGFPPなどを再生する場合は、強度が必要とされない製品にするしかなく、それでは使えないということになると廃棄せざるをえません。しかも、ガラスは焼却炉にくっついてしまうので燃やせない。そうすると、埋めるしかないんだそうです。
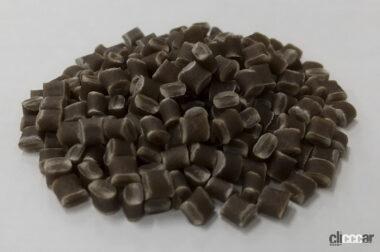
でも、CNF強化樹脂に関しては、そのまま粉砕し溶かし、ペレットにして再度射出成形してリサイクルできます。もともとがナノファイバーなので、粉砕して繊維が短くなってしまうことがなく、リサイクルしても強度が落ちないのです。
つまり、性能を落としたリサイクルではなく、同じ水準のものとしてリサイクルできるわけです。これが「水平リサイクル」です。
まさに持続可能な素材です。
一方で、最終的には「残渣がないので、燃やすこともできます。もともと木なので」(井上さん)といいます。
●静岡県内の日本製紙とコラボして材料を開発
このCNF強化樹脂ですが、ヤマハ発動機が素材からすべて開発しているわけではありません。ペレットを供給しているのは、静岡県富士市にCNFの拠点を持つ日本製紙です。
もちろん、ヤマハ発動機のようなメーカーは新しい素材を常に探しているわけですが、益子さんがCNFに関心を持ったのは、もともとはデザイン本部にいたときに、京都で行われたCNFのフォーラムで「発色がよくて環境にもいい素材」として目に止まり、そこから「じゃあちょっとCNFの研究開発をしてみようか」と思ったそうです。
その後2016年ぐらいから、ヤマハ発動機がある静岡県内でもCNFの普及のためのフォーラムがあり、CNF強化樹脂を開発して製品化を目指していた日本製紙とマッチングしてもらって、タッグを組むことになったそうです。
「あとはトライアンドエラーです。まずは、CNF強化樹脂で作ったペレットを提供してもらって、それに対して自社内で成形した試作品で各物性の評価をさせていただいて、ここが足りないからここを変えて欲しいとか、そういうやりとりをして開発を進めました。
そうやって、凝集もしにくく、ウィークポイントができるようなこともないように日本製紙さんに樹脂の成分配合を設計してもらって、衝撃にも強い製品になってますし、これだったらいけるね!っていうところで、製品に採用させていただいたというような経緯です」(益子さん)
●水上オートバイだから最初に採用できた!?
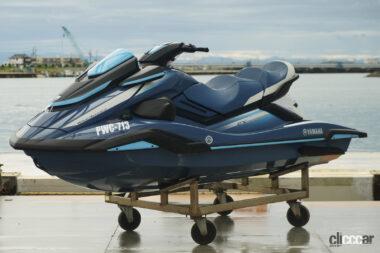
ヤマハ発動機といえば、まず2輪車をイメージする方が多いと思いますが、今回CNF強化樹脂が初採用されたのは、水上オートバイです。そこにもいくつか理由がありました。
「最近は海洋プラスチックが問題になったりしているなかで、少しでも環境にいいものを早期に採り入れたいという思いが、マリン事業部の中にあったんですよね。
あとは、このCNF強化樹脂は、従来の強化樹脂の材料に比べて、値段がかなり高額になっちゃうんです。その点、水上オートバイは価格が200万円台後半から300万円ぐらいなので、モーターサイクルと比べるともともとの製品単価が高い。そこで、価格に上乗せするのではなくて、他のとこでコストダウンして吸収することができたっていうのもあります」と井上さんはいいます。
「でも、マリンのほうで使って、使用量が増えれば値段は下がってくるので、そうすれば、他の商材にも展開できるんじゃないかと考えています」とも。
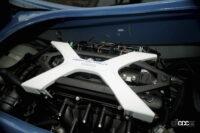
やはりCNF強化樹脂の大きなネックは、その価格でした。自動車メーカー、自動車部品メーカーなどもCNF強化樹脂への関心は強いのですが、コストの面から二の足を踏んでいて、採用に踏み切れていないという状況のようです。
その中で、ヤマハ発動機が先鞭をつけたわけですが、水上オートバイという趣味性が高く、価格帯も高めのジャンルだったからこそできたという面があるかもしれません。
ただ、この新しい素材の採用は、ヤマハ発動機といえども、そう簡単ではなかったようです。通常のように、会社内の材料開発部門が開発してヤマハの標準材として登録し、それを艇体開発などの部門が採用する、というルートならスムーズなのですが、今回は逆で、艇体開発の部門が「この材料を使いたい」と申し出たため、材料技術の部門や生産技術の部門などに、順番に説明して合意してもらって、やっと採用が実現したのだそうです。
●モーターサイクルにも採用して欲しい!?
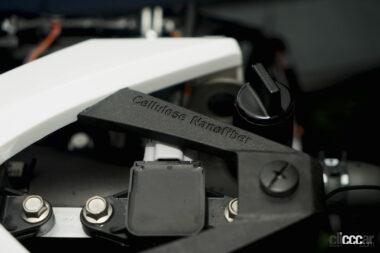
ともあれ、CNF強化樹脂が初めて輸送機器部品の量産品として採用されたわけです。CNF強化樹脂は今後、どんなふうに広まっていくのでしょうか。
益子さんは、「使ってもらいたいのはモーターサイクルです。特に、生産台数が多いASEAN(東南アジア)のモデル。そうすると、量産効果でコストが下がるのでもっと普及するはずです。なので、まずはそういう啓蒙活動を社内でボクらがひたすらしていくことになるでしょうね(笑)」といいます。
CNF強化樹脂は、耐衝撃性、耐摩耗性も上がるので、たとえばスクーターのフロア部分などには最適です。従来の強化樹脂より軽く作れるので、燃費の改善、電動バイクの電費の改善にも貢献します。もともと発色性のいい材料なので、塗装をしなくて済むようになれば、その塗装のコスト削減分で材料費の増加を吸収できるかもしれない。それでリサイクルできるとなれば、メリットは大きいでしょう。
また、CNF強化樹脂は木材が原料で、材料は国産100%なのだそうです。それによって、原材料の海外依存が減らせたり、国内の林業の活性化が図れたりというメリットもあるので、農水省が推進しているというような状況でもあるようです。
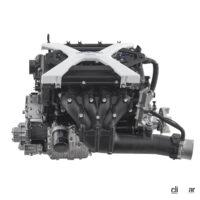
今回CNF強化樹脂が採用されたのは、水上オートバイ「ウェーブランナー」の5機種と、ウォータージェット推進機を搭載する「スポーツボート」の17機種です。エンジン自体がフルモデルチェンジされ、排気量アップしつつ環境に優しいエンジンになっていますが、そのエンジンカバーの素材にCNF強化樹脂が採用されたわけです。
ヤマハ発動機が、世界の輸送機器メーカーに先駆けてCNF強化樹脂を採用できた理由を、益子さんはこう語ります。
「ヤマハはなんでもチャレンジさせてくれる会社っていう、そこがイチバン大きいと思います。新しいことにも寛容で、失敗してもそれでペナルティがあることもない会社なので、チャレンジして製品になればいいじゃん!っていう感じでできたことかな、と思います」。
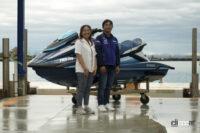
また井上さんは、ヤマハ発動機の中でも、特にマリン事業本部だからできたということを強調します。
「組織自体がミニマムにできているので、我々の所属も、艇体開発部の中に先行デザインがあって、組織的に分かれていないので、先行デザインでやっていることがすぐに量産として取り込みやすい環境にあったのは大きいですね。モーターサイクルのほうだと開発は開発、先行デザインは先行デザインって別れていますが、マリン事業本部では、組織的に同じところにいて『これやりたいんだよね』『じゃあやってみれば』みたいなことができたっていうところも大きいのかなぁ、って思います」。
持続可能な社会の実現というと、どうも義務感が先行してしまいますが、こういった先進的な技術の登場はなんだかワクワクさせてくれますね! 水上オートバイやモーターサイクルの楽しみも持続していけるように、ヤマハ発動機には期待しちゃいましょう。
(文:まめ蔵/写真:小林 和久、ヤマハ発動機)
【関連リンク】
ヤマハ発動機 技と術
https://global.yamaha-motor.com/jp/design_technology/technology/
ヤマハ発動機 クラフトマンシップ ヤマハの手
https://global.yamaha-motor.com/jp/design_technology/craftsmanship/
Sponsored by ヤマハ発動機