目次
■車の製造技術とは
車は多くの部品からできており、製造工程はプレス工程、溶接工程、塗装工程、エンジン製造工程、組立工程、完成検査の6つの工程から成ります。
車の製造工程とさまざまな製造技術について、順を追って解説していきます。
製造工程の流れ
車の製造ラインは、基本的には6つの工程で完成します。
最初の3工程でボディの基本フレームを作ります。まず、プレス工程では1枚の鋼板を切断してプレス機で成型、2番目の溶接工程ではプレス成型された鋼板を溶接して基本フレームを成形、3番目の塗装工程では出来上がったホワイトボディを塗装します。
4番目のエンジン製造工程ではエンジンを作り、最終的に5番目の組立工程で塗装を終えたボディに、エンジンやインパネ、シート、ドアなどを組み付けます。ここで製造は終了しますが、最後に検査工程で完成検査して、問題なければ出荷されます。
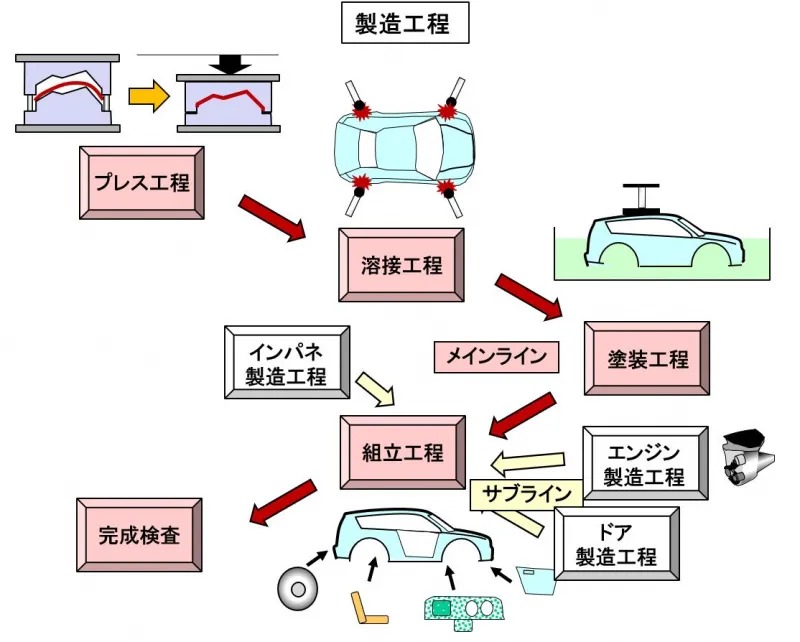
プレス工程
ボディなど車の主要構造には、主に厚さ1mm程度の鋼板(冷間圧延鋼板)が使用されます。ロール状の鋼板を、ドアやボンネット、サイドパネルなどの適切なサイズに切断します。
切断後、プレス機の金型で鋼板を挟み、プレスして部品を作り出します。通常プレスは1回でなく、何回かプレスして成型します。
溶接工程
プレス成型された部品は、溶接ロボットを使ってつなぎ合わせます。溶接方法は、厚さや部位によって使い分けます。
接合する2枚の鋼板に電流を流して、発生する熱で接合するスポット溶接が主流です。そのほか、点溶接でなく線溶接ができるアーク溶接や、ロボットアームが鋼板を挟めない部位で使われるレーザー溶接なども適材適所で使い分けます。
塗装工程
プレス工程と溶接工程を経て作られたボディは、ホワイトボディと呼びます。
ホワイトボディは、まず錆防止のために電着塗料の入ったプールに浸けて下塗りします。その後、中塗り塗装、ボディカラーの上塗り塗装を行い、最後に保護膜の役目を果たすクリアコートを施します。
エンジン製造工程
エンジンの部品の多くは、外部の専門部品メーカーで作られ、それらの部品がサブラインに搬入されて組み立てられます。自動車メーカーによっては、エンジン専用工場で組み立てられてから、搬入される場合もあります。
完成したエンジンは、台上試験によって出力性能や騒音を検査して、異常がないかを確認します。
組立工程
塗装工程を終えたボディに、エンジンやインパネ、シート、ウィンドウ、ドアなどを組み付けます。組み付けられる部品は、エンジン同様、部品メーカーやサブラインで小組されて、メイン組立ラインに搬入されます。
完成検査
具体的な検査項目は、数百項目にも及び、大別すると外装/内装検査、エンジンルーム検査、ヘッドライト光軸検査、水漏れ検査、灯火類点灯点滅検査、足回り検査、台上走行検査、完成車実走行などです。
複数の検査員によって、1台ごとに実施され、最終的にすべての検査に合格した車が出荷されます。
完成検査の不正
自動車を市場に投入するためには、国が定める安全基準を満たす必要があります。しかし、1台1台を国が完成検査するわけにもいかないので、法令に基づき認定されたメーカーの検査員が完成検査するように規定されています。
2017年秋の日産とスバルによる無資格者による完成検査に始まり、その後も検査未実施や検査データの書き換えなど不正が相次ぎました。マツダやスズキでも不適切な検査が明らかになりました。
優れた技術や魅力的なデザインでも、それを具現化する製造技術や製造品質が確保できないと、車には採用できません。車の構想から始まって、研究や開発を経て最終的に車を完成させるという流れの中で、最終段階の製造工程に注目してみました。
本章では、製造工程とさまざまな製造技術について、詳細に解説します。
■プレス加工
製造ライン最初の工程であるプレス工程は、鋼板を型に合わせてプレスすることによって、ボディのルーフやフロア、サイドパネルなどの主要パネルを成型します。
軽量化と高強度の両立が求められる主要部品のベースをつくるプレス工程とプレス加工技術について、解説していきます。
プレス工程の流れ
プレス加工に使われる1mm程度の鋼板は、鉄鋼メーカーからロール状のコイルで搬入されます。
鋼板コイルは、まず平らに伸ばし、圧縮や引張りなどの力を加えて歪のない均一な平板にします。ボンネットやサイドパネルなどの大きさに合わせて、ブランキングマシーンと呼ばれる専用のカッターで切断します。
使用する鋼板は、ボディの部位によって大きさや材質、厚みも異なりますが、大小合わせると1台当たり100枚以上使われます。
切断された鋼板は、それぞれの部品の金型を挟んだプレス機でプレス(大きなものでは、3000トン以上で加圧)して、部品の形に成型します。1回のプレスでなく、何回かのプレスによって部品形状に仕上げます。
プレス加工法
サイドパネルのような大物部品のプレス加工では、「ドロー工程」「トリミング工程」「ベンド工程」「ピアス工程」の4工程で完成させるのが一般的です。
ドロー工程でおおまかな大きさと立体形状に成型され、次のトリミング工程で余分な外形形状を切断します。ベンド工程で細かな曲げ加工を行い、ほぼ最終の部品形状になります。最後に、ピアス工程で必要な穴あけなどを行い、完成します。
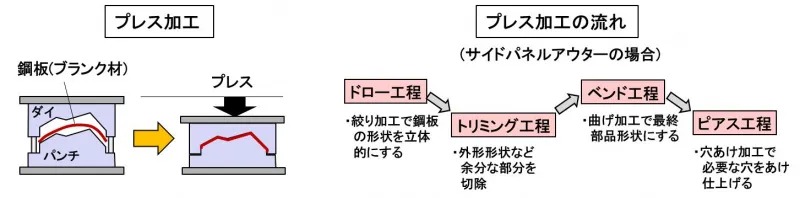
金型のゴミ嚙み
プレス加工は大きな圧力でプレスするので、プレス金型に入り込んだミクロン単位のゴミや塵によって、パネルに微妙な凹凸ができることがあります。金型のゴミ噛みには細心の注意が要ですが、万一パネルにわずかな凹凸が発生した場合は、状態にもよりますが現場の熟練工が叩いて修正します。
プレス加工で使う材料
従来から自動車用の大物プレス部品の主要材料として使用されているのは、冷間圧延鋼板です。最近は軽量化のため、冷間圧延の高張力鋼板(ハイテン)の適用が急速に進んでいます。
一般の鋼板は、引張り強さ270~310MPa程度ですが、高張力鋼板は340MPa以上の引張り強さがあり、1470MPaの高張力鋼板まで車用に適用されています。高張力鋼板を使えば、強度を確保しながら板厚を薄くできるので、軽量化できます。
ただし高張力鋼板では、強度が強くなるほど成型性が悪くなります。そのため、初期は高張力鋼板の使用は、センターピラー内部の補強材やサイドシル、サイドメンバーなど、形状が単純な部位に限られていました。成形技術の改良が進み、適用範囲は広がっています。
ホットスタンプ
欧州を中心に、ホットスタンプ(熱間プレス)の適用が進んでいます。ホットスタンプは、鋼板を加熱して柔らかい状態で成型する技術で、超高張力鋼板などの成型に適するほか、形状の自由度が高いのが特徴です。冷間プレスでは難しい複雑な形状の部品用として、ホットスタンプの需要が高まっています。
ただし、生産性では冷間プレスに劣るので、現状は熱間プレスと冷間プレスを使い分けています。
プレス加工は、一般の機械加工と比べて、加工時間が短く、加工精度がプレスの型で決まることから、大量生産に適した加工法です。
以前はプレス成型性については、形状の複雑さや微妙な調整のために、熟練設計者の経験に頼る部分が多々ありました。最近はプレス成型のシミュレーション技術が進み、精度良く事前検討ができるようになっています。
■ボディ溶接
製造ラインの溶接工程は、プレス加工された各部位のパネルを溶接で組み合わせる工程です。高い精度で効率よく組み上げるため、溶接作業を自動制御するロボット溶接で行います。
溶接工程で採用されている主要な溶接技術について、解説していきます。
溶接工程
車の製造ラインは、基本的には6つの工程で完成します。
前半のプレス工程と溶接工程、塗装工程を経て、ボディの基本的なフレーム構造「ホワイトボディ」が出来上がります。その後、サブラインのエンジン製造工程でエンジンを組み立てて、最終的に組立工程でボディにエンジンやインパネ、シート、ドアなどを組み付けます。最後に完成検査で最終チェックして、出荷されます。
溶接工程では、プレス成形された各部位の部品を、溶接ロボットによってつなぎ合わせます。溶接ロボットは、厚さや部位によって溶接方法を使い分け、車種に合わせて自動で制御されます。
溶接方法の主流は、接合する2枚の鋼板に電流を流して、発生する抵抗熱で接合するスポット溶接です。そのほか、点溶接でなく線溶接ができるアーク溶接や、ロボットアームが鋼板を挟めない部位で使われるレーザー溶接などがあります。
代表的な3つの溶接方法について、説明します。
スポット溶接
スポット溶接は、溶接時間が短くて生産性が高いため、車の溶接の主流となっています。
接合する2枚(3枚も可能)の鋼板を圧着して高電圧をかけ、接合部に発生する抵抗熱で鋼板を溶解して溶接します。
スポットの数を増やすとボディ剛性は上がりますが、スポット間に電流リークが発生するため、短いピッチで溶接ができないという課題があります。強度が必要な部位では、極力スポット数を増やすことが理想ですが、スポット溶接だけではどうしても限界があります。
アーク溶接
アーク溶接は、空間中に高電圧をかけて発生するアーク放電を利用して溶接する方法です。その中でも、シールドガスに不活性ガスを用いるミグ(MIG)溶接が一般的です。電極にワイヤーの溶接材料を使用し、ワイヤーと溶接部位の間に発生したアークで、ワイヤーと部位を溶解しながら溶接します。
ミグ溶接は、シールドガスの効果によってひずみが発生しづらいので、薄板鋼板の溶接に適しています。しかし、自動化に不向きなため、用途は溶接アームが入りにくい場合や強度が必要な場合に限られます。
レーザー溶接
レーザー溶接は、レーザーを集光した熱で鋼板を溶かして溶接します。溶接熱の影響が少なく、溶接変形が少ないこと、点ではなく線溶接ができることが最大の利点です。
スポット溶接よりも接合強度が上がるので、ボディサイドシールやスポット溶接が難しいルーフなどに使われます。ただし、スポット溶接のように鋼板を挟んで溶接しないため、鋼板間の微妙な隙間(板隙)によって溶接品質が影響される課題があります。
現行のレーザー溶接は、強度が必要な箇所にスポット溶接した点と点の間を補強する形で使われるのが、一般的です。
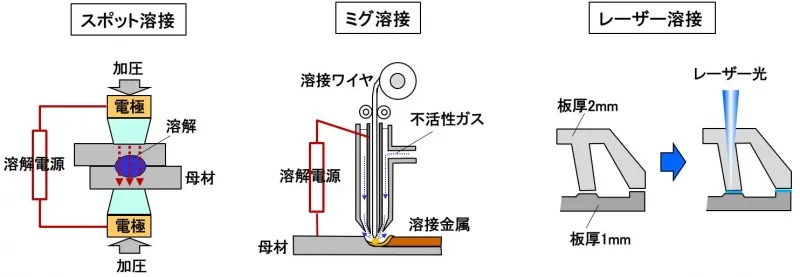
自動車用ボディには、高い剛性と軽量化、コスト低減、さらには材質の多様化などのニーズに応えるため、さまざまな溶接技術が開発されて適用されています。
今後も鋼板中心のボディの場合については、スポット溶接が主流です。スポット溶接で対応できない部位については、アーク溶接やレーザー溶接で補強する、適材適所で使い分けることになります。
■ボディ溶接 レーザー・スクリュー・ウェルディング
製造ラインの溶接工程では、スポット溶接を中心として、部位によっては補強の目的でアーク溶接やレーザー溶接を適用しています。
ボディの剛性を高めるために、トヨタが開発した溶接手法であるレーザー・スクリュー・ウェルディング(LSW)について、解説していきます。
現行の溶接技術と課題
スポット溶接は、従来から車のボディ溶接の主流として採用されています。溶接する2枚の鋼板を電極で挟み、通電して電気抵抗による発熱で鋼板を溶かして接合します。
課題は、点接合で、しかも近接するスポット間の電流リークを避けるために、短いピッチで溶接ができないことです。結果として、十分な接合剛性を確保するのが難しくなります。
レーザー溶接は、レーザーを集光した熱で鋼板を溶かして溶接します。点ではなく、線溶接ができることが最大の利点です。一方で、スポット溶接とは異なり、鋼板を挟み込んで溶接しないため、鋼板間のわずかな隙間(板隙)によって品質が不安定になり、適用できる範囲が限定されるという課題があります。
以上の課題を踏まえ、現行のレーザー溶接は、強度が必要な箇所にスポット溶接した点と点の間を補強する形で使われるのが、一般的です。
レーザー・スクリュー・ウェルディング(LSW)
レーザー・スクリュー・ウェルディング(LSW)は、ロボットの先端に装着したレーザー発振器からレーザーを照射して、重ね合わせた鋼板を溶接する手法です。
従来は、スポット溶接の点と点の間に細い線を引くようにレーザー溶接を行い、補強していました。LSWは、線溶接ではなく、溶接の形を円形にして接合面積を広げました。スポット溶接の間に直径5mm程度の円形溶接部を数ヵ所設けます。
メリットは、次の通りです。
・密度の高い(スポット間隔が狭い)溶接による接合剛性の向上
・高速(スポット溶接の約3倍)の溶接による生産効率の向上
・片側からの溶接アクセスが可能なため、溶接自由度の向上(狭い部位や構造の溶接)
4代目プリウスに採用した例では、打点ポイント数を旧型車に比べて30%増やすことができ、ボディ剛性は60%向上しています。
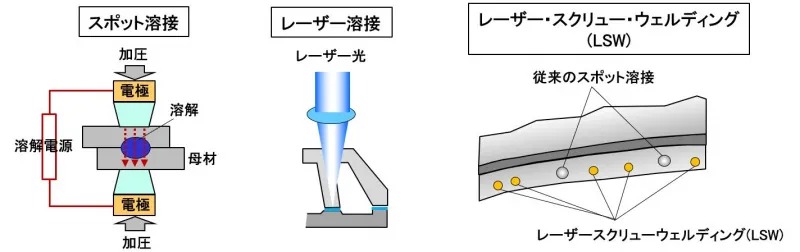
LSWのメリット
車にもたらすメリットとしては、大きくは2つあります。一つ目は、ボディ剛性の向上による走行性能の安定化です。
剛性が高いと、加減速時やコーナリング時のボディの捻じれが抑えられ、確実に駆動力を路面に伝えることができます。これにより、車の操縦安定性や乗り心地が向上し、さらに車体各部の歪みに起因する車体振動や騒音も低減できます。
二つ目は、軽量化です。接合剛性が向上すれば、補強材を減らす、構造を見直すことができ軽量化につながります。また、LSWは片側アクセスで溶接ができるので、スポット溶接に比べて接合配置の自由度が高くなります。骨格設計の制約が少なく、軽量化設計が容易になるメリットもあります。
レーザー・スクリュー・ウェルディング(LSW)は、スポット溶接とレーザー溶接の課題を克服し、両方の特徴を生かした技術です。最大の成果は、剛性や軽量化、生産性といった、一見すると相いれない要求を同時に改良している点ではないでしょうか。
この技術を通して、優れた車づくりのためには、設計技術や開発技術だけでなく、生産技術の寄与も大きいことが分かります。
■ボディ塗装
プレス工程と溶接工程を経て、ボディの基本骨格が出来上がったホワイトボディは、塗装工程で塗装されます。塗装は、基本的には1回でなく、下塗り、中塗り、上塗りの3工程で行われます。
塗装工程で行われる塗装技術について、解説していきます。
ボディ塗装の概要
ボディの塗装は、それ自体大きな商品価値であり、一方でボディを腐食から守るという役目も担っています。塗装の厚みは0.1mm程度ですが、厳冬や灼熱、酸性雨、潮風などに晒されても、色褪せやひび割れを起こさない耐久性が要求されます。
ホワイトボディは、前処理としてまず洗浄してから錆防止の下塗りをします。その後、中塗り塗装を経て、ボディカラーとなる上塗りをして、最後にクリアコートを行います。これを「4コート3ベーク」と呼びます。
コートとベーク
4コート3ベークのコート(coat)は塗装の数、ベーク(bake)は乾燥の数を示します。メーカーによっては、中塗りを省略した3コート2ベークで塗装を行う場合もあります。塗装技術は進み、コート数が少ないから品質が劣るわけではありません。
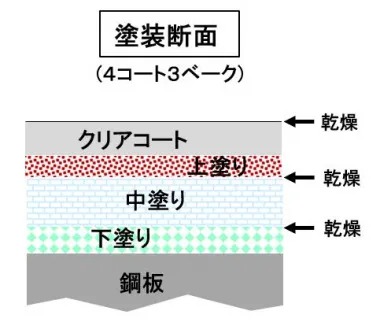
下塗り
溶接が終わったホワイトボディはすぐに錆びてしまうので、下塗り工程に移されます。下塗り工程の前に、防錆や下塗りの塗装の密着性を良くするため、最初にリン酸塩などで化成処理してボディに被膜が作られます。
下塗りには電着塗装という技法が使われ、鋼板と塗料との馴染みを良くするとともに、錆防止という重要な役目を担っています。
電着塗装では、水性の電着塗料が入ったプールの中にホワイトボディを浸し、塗料をプラス、ボディをマイナスにして電流を流し、塗料を車体に引き付けて塗装します。この数分間の通電で20~30ミクロン(0.02~0.03mm)程度の塗膜が形成されます。
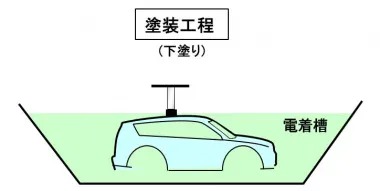
中塗り
下塗りの段階では、表面はまだ粗いです。最終的な仕上がりを良くするため、また耐チッピング性を高め、色落ちを抑えるため、30ミクロン程度の中塗りを行います。
チッピングとは、飛んできた小石によって塗装面が剥がれることで、錆の原因となります。
中塗りは、塗膜が均一になるようにロボットのスプレーによって行われます。ここでは、静電塗装という技法が使われます。微粒上の塗料を帯電させて、ボディ側をマイナスにしておくと、電気的に塗料がボディに付着しやすくなります。
上塗り
上塗り工程では、最終的なボディカラーの塗料が静電塗装によって吹き付けられます。塗料には、普通のソリッドカラーと、光を反射させる顔料を含んだメタリック系があります。ソリッドカラーは40ミクロン程度の厚さです。一方、メタリック系は15ミクロンほどのベース層に30~40ミクロンの透明なクリアコートが上塗りされます。
ソリッドカラーは、そのままでもある程度の光沢があり、クリアコートが必要ないように設計されています。
最近は、ソリッドカラーでクリアコートされている車が増えています。クリアコートによって、より光沢感が増すことと、耐紫外線や耐酸性雨、耐摩耗性など、耐久性を向上させるのが狙いです。
昔の車は、10年も乗ると機能の低下よりも、塗装の剥がれや色褪せが目立っていました。塗装技術が進み、最近はボディが色褪せた車を見かけることはなくなりました。また同じカラーでも、メーカーによって微妙な違いがあり、ボディカラーの差別化が進んでいます。
ボディカラーは、車を引き立たせて商品価値を高める重要な要素になっています。
■エンジンとインパネの製造
エンジンやインパネを構成する部品は、一般に外部部品メーカーで製造され、製造ラインのサブラインで組み立てられます。
エンジン部品の主要な製造方法である鋳造と鍛造、インパネなどの樹脂部品の製造方法、射出(インジェクション)成形について、解説していきます。
エンジンの組み立て
エンジンのシリンダーブロックやシリンダーヘッドなどの大物部品は、自動車メーカーで製造するのが一般的ですが、専門の部品メーカーに外注する場合もあります。また、ピストンやバルブなど多くのエンジン部品は、部品メーカーで製造されます。
これらの部品は、組立工場に搬入されてエンジンサブラインで組み立てられます。自動車メーカーのエンジン組み立て専用工場で完成させて、直接メインラインに搬入される場合もあります。
エンジンサブラインでは、ベースとなるシリンダーブロックに順次、クランクシャフト、ピストン+コンロッド、オイルパンなどが組付けられ、その上にシリンダーヘッド+吸排気マニホールドが搭載され骨格が出来上がります。
エンジンが完成すると、トランスミッションが組み付けられて、メインラインに組み込まれます。
エンジンの製造法
高回転・高温で回転するエンジンには、耐熱性や耐摩耗性、高い強度や剛性が求められます。これらの要求に応えるエンジン部品の製造法を大別すると、鋳造法と鍛造法があります。
シリンダーブロックやシリンダーヘッド、ピストンなどの部品は、形状が複雑で軽量化が必要なことから、一般にはアルミ合金の鋳造で製造されます。またコンロッドやギヤなどは、強度が必要なため鍛造で製造します。
鋳造は、金属を高温で溶かして液状にして型に流し込んで、冷やして固めます。複雑な形状でも、比較的容易に短時間で加工でき、安価で大量生産が可能です。
一方、内部に気泡ができやすく、また厚みが違う部分を冷やした際に残留応力が発生しやすいため、これらが強度を下げる要因となります。
鍛造は金属を加熱した後、ハンマーやプレス機などでプレス成型します。圧縮によって金属の結晶を整え、気泡などの内部欠陥を圧着させるため、高い強度が実現されます。
一方、精度の高いものを製造するには時間がかかり、精密な部品の製造には向きません。量産のスピードは、鋳造より遅くなります。
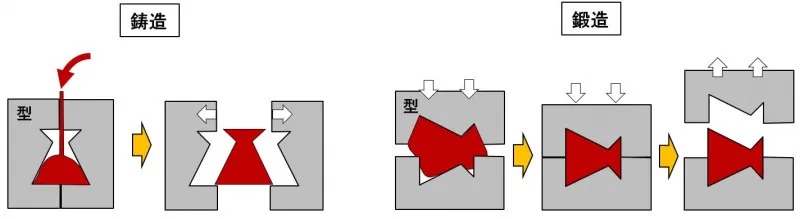
インパネの製造法と組み立て
組み立て工程が多いインパネやドアは、エンジン製造と同様、サブラインで組み立てられてメインラインに組み込まれます。
まず、インパネ本体にフレームを組み付けます。その後、エアバッグやエアコンダクト、メーター、カーオーディオ、グローブボックスなど、多くの部品が組み込まれます。
インパネには、メーターなど多くの機能部品が組み込まれ、目に見えない裏面にも多くの機能部品が収納されているため、組み付け強度も必要です。また複雑な形状になるため、インパネ本体は射出成形で製造されます。
射出成形は、熱可塑性の樹脂を成型機でいったん溶かし、金型に圧力を加えて射出した後、冷やして固めて型から取り出します。
各種成形技術の中でもっとも精密性が高く、短時間で大量生産ができるため、インパネだけでなくバンパーなど樹脂製の内外装品の多くは、射出成形で製造されます。
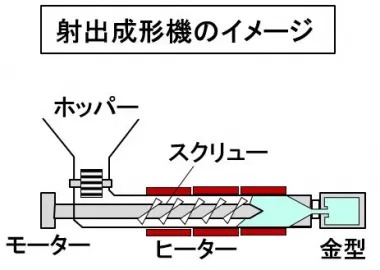
エンジンやトランスミッション、ドア、インパネなど、組み立て工程の多い大物部品は、サブラインで完成品まで製造、組み立てるのが一般的です。
効率よく車を組み立てるためには、サブラインとメインラインは常時連携をとる必要があります。
■完成検査
組み立てが完了したすべての車両は、国の定めた安全基準に適合しているか、品質は確保されているかを確認するため、数百にもおよぶ項目の検査が行われます。これが完成検査で、合格した車両だけに完成車検査修了証が発行されて、出荷が許されます。
製造工程の最終工程、完成検査について解説していきます。
型式指定の申請
メーカーが新型の自動車を生産、販売する場合は、あらかじめ国交省に届け出て、保安基準への適合性などについて審査を受ける必要があります。
審査は、燃費/排ガス試験やブレーキ試験などの基準適合性審査と、品質管理(均一性)審査があります。どのようなタイプの自動車で、申請通りの機能や性能を有するかなどの審査が行われ、合格すると型式指定が受けられます。
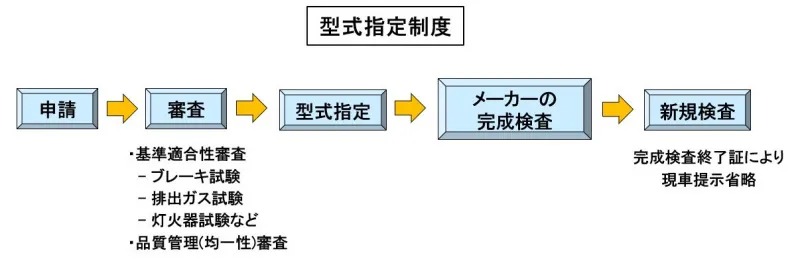
完成検査の概要
型式指定を受けた上で、メーカーは製造された車両すべてについて完成検査します。完成検査は、型式指定を受けた型式としての構造、機能、性能を有しているか、国の定める保安基準に適合しているかを検査します。適合していれば、完成検査修了証が発行されて出荷できます。
本来は、国または第三者機関が検査して判断すべきですが、すべての車両を検査することは現実的に不可能なので、国が各メーカーに検査と判断を委ねている形です。
完成検査は、各メーカーが定めた認定基準を満たした有資格者しか実施できません。検査員は、数百におよぶ車両全体の項目をチェックするため、車全般の技術と知識が必要です。
完成検査の実施規定
完成検査実施要領および判定に係る規定は、以下の通りです。
・完成検査実施規定第2条(完成検査の実施方法)
「検査員が基準に基づき点検を行い、その結果保安基準に適合すると認めた部分については、当該部分に係る検査に影響を及ぼす整備がされなければ、完成検査において保安基準に適合するものとする。」
・完成検査実施規定第2条(完成検査の判定)
「完成検査の判定は、保安基準、自動車検査独立行政法人審査事務規定および検査関係通達等さらに社内基準により実施するものとする。」
完成検査の内容
完成検査の内容は、型式指定の申請時にメーカーが提出した実施要領に則り実施するため、具体的なやり方についてはメーカーごとに異なります。しかし、目的は国の安全基準に適合しているか、品質が確保できているかの確認なので、内容に大差はありません。
具体的な検査項目は、外装/内装検査、エンジンルーム検査、ヘッドライト光軸検査、水漏れ検査、灯火類点灯点滅検査、足回り検査、台上走行検査、完成車実走行検査などです。
複数の検査員によって1台ごと実施され、最終的にすべての検査を合格した車が出荷されます。
また、燃費や排ガスなど重要項目については、例えば100台に1台程度の割合で抜き取り検査を行います。申請通りの燃費値が出るか、排出ガスが規制値に適合しているかを定期的に確認します。
もしも適合していなかった場合、適合できるまで生産はストップします。
不正が起きたケースも
2017年秋の日産とスバルによる無資格者による完成検査に始まり、その後も検査未実施や検査データの書き換えなど不正が相次ぎました。マツダやスズキでも不適切な検査が明らかになりました。
車の品質は、最終の完成検査で確認される以前に、部品ベースや組み立てた段階で何回もチェックされるので、実際のところ完成検査でNGになる車はほとんどありません。
もちろん、完成検査が適正にされていることが前提で言えることですが、もし正しく実施されてなければ、上記は戯言となってしまうでしょう。
(Mr.ソラン)
クリッカー自動車用語辞典 https://clicccar.com/glossary/