目次
■車の低燃費技術とは
現在自動車メーカーは、電動車の開発に精力的に取り組み、電動車の普及に邁進しています。一方で、2040年でもエンジン搭載車(含む、HEVやPHEV)は、全体の過半数を占めると予想されています。
電動化技術とともに重要なエンジンの低燃費技術について、解説していきます。
エンジン車はなくなるのか
燃費/CO2規制やZEV(ゼロエミッション車)規制の強化を背景に、すべてのメーカーは電動車の開発に注力しています。一方で、新興国でのエンジン車の普及や、エンジンを搭載するHEV、PHEVが今後増加することを考慮すると、エンジン搭載車は2040年でも全体の過半数を占めると予想されています。
したがって、電動車に負けない低燃費エンジンや電動車用の低燃費エンジンを、電動化技術とともに車の両輪のごとく開発することが重要です。
エンジンのエネルギー収支
エンジンの仕事量は、燃料が燃焼して発生する熱量から、各種の損失(冷却損失、機械損失、ポンプ損失、排気損失、燃料の未燃損失)を差し引いた残りの熱量から引き出されます。
これらの損失は、一般には燃焼による発生熱量の60%以上に相当し、すべてが廃棄されます。
1)冷却損失
燃焼室やシリンダーなどの壁面から、冷却水に捨てられる熱損失
2)機械損失
クランクシャフトやピストンなど回転や往復運動時に発生する摩擦損失(フリクション)
3)ポンプ損失
ガソリンエンジンで、空気量をスロットル弁で絞るときの通路抵抗による損失
4)排気損失
排出ガスとして捨てられる熱や圧力の損失
5)燃料の未燃損失
シリンダー内に投入された燃料の一部が、燃焼せずに捨てられる損失
燃費を良くする、熱効率を向上させることは、これらの損失を減らすことに他なりません。
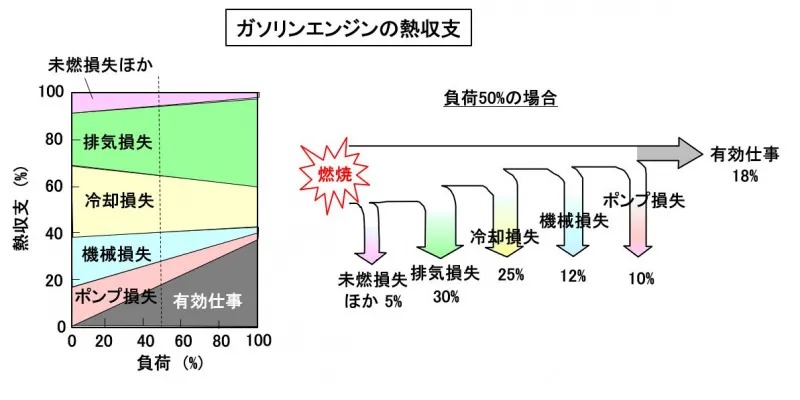
各種損失を減らす燃費向上手法
1)冷却損失
燃焼室のSV(表面積/体積)比を減らすロングストローク化(別頁で解説)、クールドEGR(別頁で解説)やリーンバーン(別頁で解説)による燃焼温度の低下は、冷却損失を減らす効果的な手法です。
2)機械損失
ピストンやクランクシャフトなど、さまざまな摺動部の形状や材料、加工法などよるフリクション低減(別頁で解説)、軽量化やダウンサイジング(別頁で解説)、また潤滑油の低粘度化なども機械損失の低減につながります。
3)ポンプ損失
スロットル開度を開ければ開けるほどポンプ損失は低減するので、ダウンサイジングやEGR、リーンバーン(別頁で解説)などはポンプ損失の低減に効果的です。また、ポンプ損失低減に効果的な可変動弁機構は、多くのエンジンで採用されている一般的な手法です。
4)排気損失
過給(別頁で解説)は排気エネルギーの一部を回収するため、排気損失を低減します。アトキンソンサイクル(別頁で解説)やミラーサイクルは、高膨張比サイクルなので排気損失を低減する有効な手法です。また、直接排気熱を回収する廃熱回収システム(別頁で解説)も、排気損失を減らす手法です。
5)燃料の未燃損失
燃料が蒸発しにくい低温時は、燃料が蒸発しにくいため未燃の燃料(HC)が増加します。これを避けるため、微粒化を促進した噴射弁が開発されています。また、未燃燃料を排気行程中に燃焼させるための排気温度制御も採用されています。
本章では、エンジン技術の低燃費に絞り、最近注目を集めている可変圧縮比エンジンやHCCI(予混合圧縮着火)エンジンも含めて、さまざまな最新の低燃費技術の詳細について個々に解説していきます。
■ダウンサイジングターボとは
2000年以降、欧州では燃費向上のため、排気量の小さいエンジンに直噴ターボを組み合わせた「ダウンサイジング直噴ターボ」が普及し始め、日本でも採用例が増えてきました。
最近のRDE(実走行排出ガス)規制など、実走行での燃費や排出ガスを重視する動きの中で、課題も浮上してきたダウンサイジング直噴ターボのメリットと課題について、解説していきます。
ダウンサイジングのメリット
ダウンサイジングは、排気量を小さくして燃費向上を図り、出力低下をターボで挽回するコンセプトです。欧州で採用が始まり、日本でも採用例が増えています。
排気量を小さくする、あるいは気筒数を減らすと、ポンプ損失とフリクションが低減するため燃費が向上します。
ポンプ損失の低減は、同じ出力を得るためのスロットル開度が大きくなるため、また、摩擦損失の低減はエンジンの構成部品が小型化するためです。
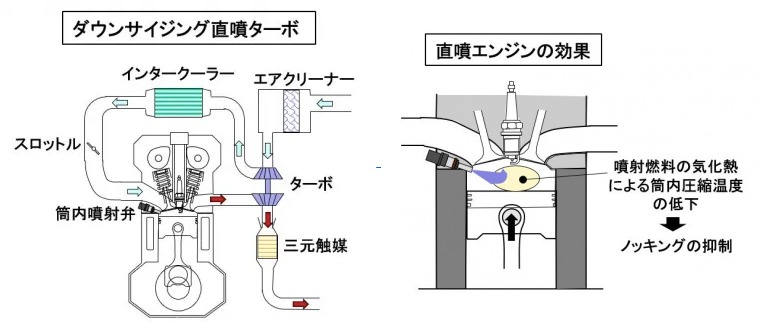
直噴ターボのメリット
ターボで過給すると、吸入空気が圧縮され、シリンダー内の圧縮温度も上がるため、無過給エンジンに比べてノッキングが発生しやすくなります。したがって、過給エンジンは無過給エンジンよりも圧縮比を低めに設定しなければいけません。
直噴(筒内直接噴射)は、吸気ポートに燃料を噴射する通常のガソリンエンジンに対して、以下のメリットがあります。
・シリンダー内に噴射された燃料は、周辺から熱を奪って気化します。この気化潜熱によってシリンダー内の温度が低下し、密度が上昇し、吸入空気が増え、出力が向上します。
・シリンダー内の圧縮温度が下がると、ノッキングしづらくなります。ノッキングが抑えられれば、圧縮比を上げることができ、出力向上や燃費向上につながります。
以上のように、直噴はノッキングしづらく、ターボ化による圧縮比の低下を最小限に抑える効果があるため、ダウンサイジングターボには必須シテムなのです。
ダウンサイジング直噴ターボの課題
ダウンサイジングするということは排気量が小さくなるので、ターボが効かない低速域はトルク不足になります。また、ターボにはターボラグがあり、これら2つはダウンサイジング直噴ターボの大きなデメリットです。特に、CVTやステップATが多い日本では、発進加速などで力不足が目立ちます。
もうひとつの課題は、排気量が小さいため、中高負荷域の燃費や実走行燃費が悪化しやすいことです。マツダは、実走行の燃費を重視してダウンサイジングよりも適正な排気量「ライトサイジングの高圧縮比エンジン」の方が総合的に優れている、との見解を示しています。
ダウンサイジング過給エンジンとライトサイジング高圧縮比エンジンのどちらが優れているかは、車の使い方や走行条件に大きく左右されます。
ダウンサイジングの元祖
自動車用ディーゼルエンジンは、ほぼすべてターボエンジンです。ターボ装着によって、性能向上だけでなく、排出ガスを効果的に低減できるからです。したがって、過給によって必要な出力が確保されているディーゼルエンジンは、すでにダウンサイジングしていると言えます。
欧州では、2017年9月から国際的に統一されたモード試験「WLTC」や、実走行の排出ガスを規制する「RDE」が施行されています。これらは、高速走行を重視した実走行に近い運転条件の評価なので、小排気量のダウンサイジング直噴エンジンにとっては逆風と言えます。
■アトキンソンサイクルとミラーサイクル
低燃費技術として、最近多くのエンジンで採用されているアトキンソンサイクルとミラーサイクルは、メーカーによって呼び方が違うだけで、基本的には同じ技術です。
両者の違いを含めて、その機構とメリットについて解説していきます。
圧縮比と膨張比
圧縮比とは、「シリンダー内の空気または混合気(空気+燃料)が、ピストン上昇によってどれくらい圧縮されるのか」の割合を示す指標で、次の計算式で表されます。
圧縮比=(燃焼室容積+排気量)/燃焼室容積
一方で膨張比は、「燃焼ガスが、ピストン下降によってどれくらい膨張するか」の割合を示す指標で、通常は圧縮比と同じ値を示します。
熱効率は、燃焼エネルギーがピストンを押し下げる機械的エネルギーにどれだけ変換されるかの割合です。したがって、熱効率は膨張比に依存しますが、一般には圧縮比=膨張比なので、両者を区別せず、代表して圧縮比が使われることが多いです。
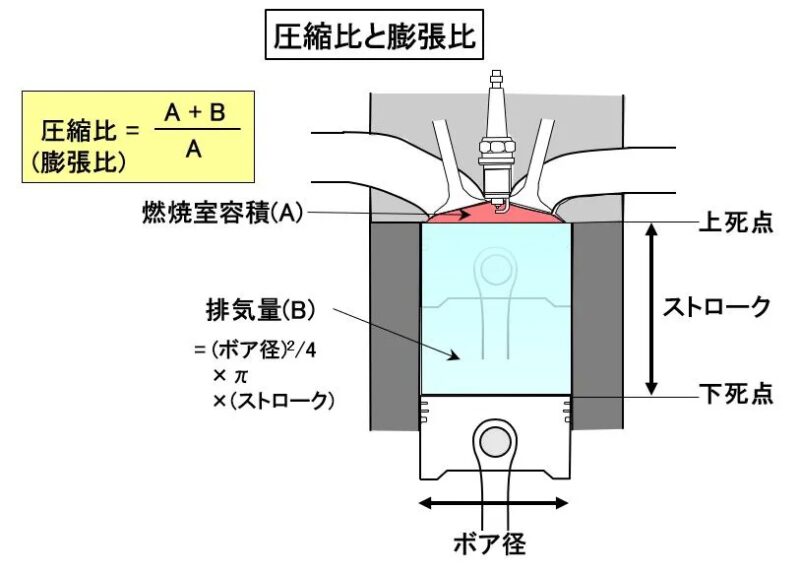
アトキンソンサイクル
通常のエンジンでは、吸気、圧縮、燃焼、排気行程の各行程の長さは、同じ(圧縮比=膨張比)です。アトキンソンサイクルは、特殊な機構によって圧縮行程(圧縮比)よりも、膨張行程(膨張比)を長くした熱サイクルです。
ガソリンエンジンでは、ノッキングが発生するため、圧縮比の上昇には限界があります。そこで、アトキンソンサイクルによって、圧縮比をノッキングしない値に抑えて、膨張比だけを上げて熱効率を上げようとするコンセプトです。
ただし、アトキンソンサイクルを実現するための機構が複雑で、機械損失が大きいなどの課題が解決できなかったため、自動車用としては実用化されていません。
ミラーサイクル
アトキンソンサイクルの圧縮比<膨張比を、吸気弁の閉弁時期の調整で実現したのが、ミラーサイクルです。具体的には、高い熱効率を確保するため、膨張比を高く設定した上で吸気弁の閉時期を遅らせる、あるいは早めることによって、実圧縮比を下げます。
吸気弁遅閉じの場合、ピストンが下死点から上昇し始めても、吸気弁は開いたままなので圧縮は始まりません。このとき、シリンダー内に吸入された吸気はピストンの上昇によって、吸気ポート側に押し戻されます。
圧縮行程は、吸気弁が閉じてから始まるので、実質的な吸気行程は短くなり、圧縮行程<膨張行程という関係が成立します。
ミラーサイクルは、アトキンソンサイクルを簡易的に実現した手法なのです。
アトキンソン/ミラーサイクルのメリットとデメリット
アトキンソン/ミラーサイクルによる燃費向上の要因は、高い膨張比による熱効率の上昇と、吸気弁の遅閉じによるポンプ損失の減少です。
吸気弁の遅閉じは、排気量を小さくしたのと等価です。排気量が小さくなると、同じ出力を得るためには、スロットル開度を大きくする必要があるのでポンプ損失が減少します。
また排気量が小さくなれば、出力が低下します。これが大きなデメリットなので、出力不足を挽回するため、ターボなど過給機を組み合わせることが必須です。
ほとんどのメーカーは、アトキンソンサイクルと呼び、マツダはミラーサイクルと呼んでいます。どちらが正しいということではなく、広義で表現するか、狭義で表現するかの違いだけです。ミラーサイクルは、アトキンソンサイクルを実現するひとつの手法なのです。
アトキンソン/ミラーサイクルは、吸・排気弁の開閉時期を自在に制御できる可変動弁機構の普及とともに、ごく一般的な技術になりました。また、ダウンサイジング直噴ターボとの組み合せも積極的に進められています。
■大量EGRとは
もともとEGRは、不活性の排出ガスを吸気に導入することで燃焼温度を下げ、NOxを低減する手法として開発されました。現在のガソリンエンジンでは、EGRはNOx低減というより、効果的な低燃費技術として活用されています。
ガソリンエンジンのEGRによる燃費低減効果を中心に、解説していきます。
EGR
EGR(Exhaust Gas Recirculation:排出ガス再循環)は、CO2を主とする不活性の排出ガスの一部を吸気に戻して、吸気とともに燃焼室に導入するシステムです。排出ガスを含む吸気は、酸素濃度が低下するので燃焼温度が下がります。
もともとEGRは、ガソリンエンジンでCO、HC、NOxを同時に浄化できる三元触媒が開発される以前に、燃焼温度を下げNOxを低減する目的で活用されていました。
高性能の三元触媒が開発された現在は、NOx低減というよりも燃費向上のために採用されています。
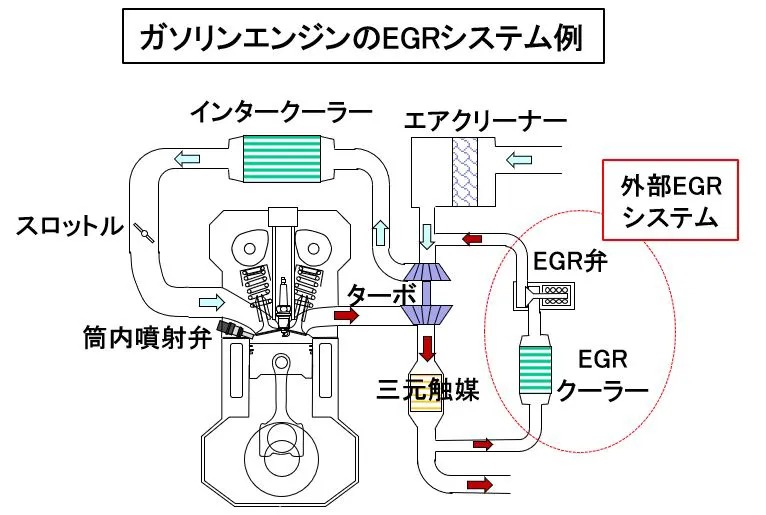
EGRの効果
EGRによる燃焼温度の低下によって、以下のメリットが得られます。
NOx低減
NOxは、2000K以上の燃焼時に窒素が酸素と(酸化)反応して生成します。EGRによって、酸素濃度が下がりNOxの生成量が減少します。
冷却損失低減
燃焼温度が低下すると、燃焼室やシリンダー壁面から冷却水に奪われる冷却損失が低減します。
ポンプ損失低減
ガソリンエンジンでは、排出ガスが吸気に導入されると、同一出力を得るためのスロットル開度が大きくなり、スロットル弁による吸気通路の絞り抵抗、ポンプ損失が低減します。
EGR量の限界
ガソリンエンジンは、三元触媒でCOとHC、NOxを同時に浄化するため、EGRの狙いはNOx低減というより、冷却損失の低減とポンプ損失の低減、すなわち燃費の向上です。
ディーゼルエンジンの場合は、もともとスロットル弁がなくポンプ損失はほとんどないため、EGRの効果はNOx低減と冷却損失の低減です。ただし、導入できるEGR量には限界があります。ディーゼルエンジンの場合は、酸素不足によるPM(煤など含む微粒子状物質)の増加、ガソリンエンジンでは燃焼が不安定になるからです。
ガソリンエンジンのEGRシステム
EGRには、導入の仕方によって「外部EGR」と「内部EGR」の2方式があります。
外部EGRは、排出ガスを排気管から取り出し、パイプによって吸気系に導く一般的な方式です。EGR弁によるEGR流量やEGRクーラーによるEGRガス温度の高精度な制御ができます。しかし、長いEGR経路が必要なため、EGR導入の応答遅れが発生します。
内部EGRは、可変動弁機構によって吸・排気弁の開閉時期を調整し、燃焼室内に燃焼ガスを残留させる、あるいは排気管から排出ガスを逆流させる方式です。
外部EGR方式のようにEGR系部品の必要がなく、また応答性良くEGRを増減できます。しかし、制御できるEGR量には限界があり、精度高くEGR量を制御できません。
両者の利点を生かすため、外部EGRと内部EGRを組み合わせるのが最も効果的です。
EGRシステムは古くから採用されている基本技術ですが、規制の強化とともにEGRの高精度制御が進み、排出ガス低減および燃費向上のために不可欠な技術となっています。
■リーンバーンとは
リーンバーン(希薄燃焼)は、1990年代に三菱GDI(ガソリン直噴エンジン)やトヨタ、日産によって市場投入されましたが、完成度が十分でなく10年程度で市場から消えました。
燃費/CO2規制の強化を背景に、直噴システムや要素技術の進化とともに再び注目され始めたリーンバーンについて、解説していきます。
リーンバーンエンジン
エンジンに吸入される空気と投入される燃料の重量割合を空燃比と呼びます。燃料と空気(酸素)が過不足なく燃焼する理論空燃比は、約14.7です。
リーンバーンとは、空燃比が理論空燃比14.7よりも大きい、すなわち燃料が少ない(薄い)混合気の燃焼です。実際には、空燃比が約20以上の燃焼をリーンバーンと呼びます。逆に、空燃比が14.7よりも小さい、燃料が多い(濃い)状態をリッチ混合気と呼びます。
リーンバーンが実現できれば燃費は良くなりますが、一方、理論空燃比で機能する三元触媒ではNOxを十分に浄化できません。
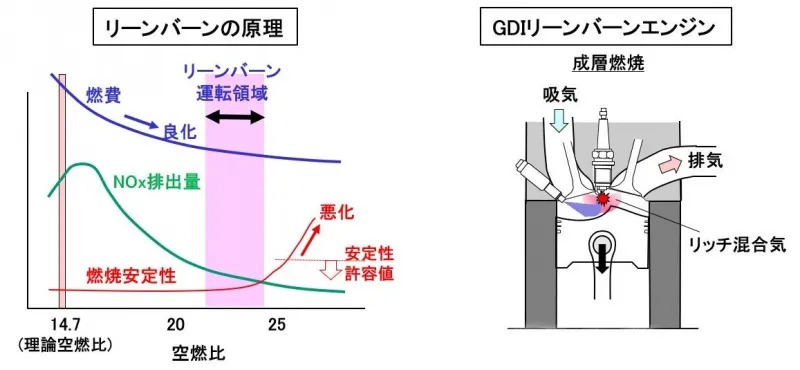
過去のリーンバーンエンジン
1996年、三菱がGDIリーンバーンエンジンを市場投入しました。GDIエンジンは量産初の直噴エンジンで、しかも燃費に優れたリーンバーンを採用した、当時としては画期的なエンジンでした。続いてトヨタや日産も、直噴リーンバーンエンジンを少量ですが、市場に投入しました。
GDIでは、燃料噴霧形状と球状のピストンキャビティ(ピストンの窪み)、タンブル流(縦渦)を組み合わせてリーンバーンを実現しました。これは成層燃焼方式と呼ばれ、着火を確実にするために点火プラグ付近だけリッチ(燃料を集中)にして、燃焼全体としてはリーンな混合気で安定燃焼を成立させる手法です。
当時のリーンバーンは、十分に完成された技術とは言えず、煤発生によるカーボンデポジット(堆積)やオイルの汚損、運転の仕方によっては燃費向上分が目減りするなどの問題がありました。さらに、次期排出ガス規制に対してNOxの適合が困難であったため、10年程度で市場から消えていきました。
リーンバーンによる燃費向上
リーンバーンによって燃費が向上するのは、以下の3つの理由からです。
・ポンプ損失の低減
リーンバーンでは、同一出力を得るための吸入空気量は増えます。したがって、スロットル開度が大きくなるため、ポンプ損失が低減します。
・冷却損失の低減
リーンバーンでは、相対的に燃料量が少ないため、燃焼速度が遅くなります。燃焼が緩慢になると、燃焼温度が低下し、燃焼室やシリンダー壁面から冷却水に奪われる冷却損失が低減します。
・比熱比の上昇
熱効率は、下記の通り圧縮比と比熱比で決まります。圧縮比と同様、比熱比が高いほど熱効率は向上します。
熱効率 = 1 – (1/ε)κ-1 ε:圧縮比 κ:比熱比
比熱比
比熱比は、定圧比熱(圧力一定での比熱)と定積比熱(体積一定での比熱)の比で表されます。空気の比熱比が1.4と最も高く、理論空燃比の混合気で1.26程度まで下がり、リーンバーンは混合気が薄い、空気に近づくので比熱比が上昇します。
上記の通り、比熱比が上昇すれば熱効率が向上します。
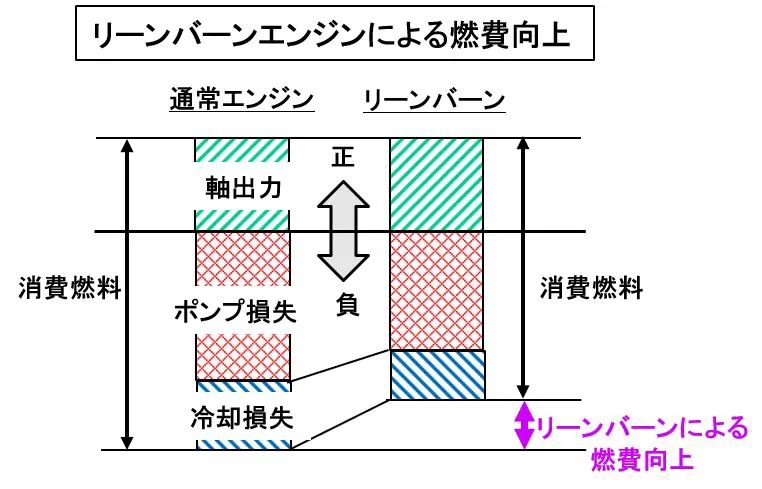
リーンバーンエンジンの今後
かつての成層リーンバーンは、まだ当時の課題が完全に解決しているとは言い難く、採用するためにはブレークスルー技術が必要です。
現在、リーンバーン実現のためのいくつかのコンセプトが提案されていますが、最も有望なのは、HCCI(予混合圧縮着火)ガソリンエンジンかもしれません。HCCIによって、部分負荷領域では、NOxがほとんど発生しないほどの超リーンバーン(空燃比で30以上)で運転でき、大幅な燃費向上が達成できる可能性があります。
多くの自動車メーカーは、2025年までに熱効率45%を実現するという目標を掲げています。実現のためのシナリオには、必ず空燃比30以上の超リーンバーンが取り上げられています。
「マツダ 3」でいち早くHCCIを実用化してきたマツダの技術も楽しみです。
■可変圧縮比エンジンとは
かつて夢のエンジンと呼ばれた可変圧縮比(VCR)エンジンが、2018年春に日産によって実用化されました。圧縮比を、運転条件に応じて自動的に最適化することによって、低燃費と高出力を両立する画期的なエンジンです。
日産が実用化に成功した可変圧縮比エンジンを例に、その仕組みや効果について解説していきます。
可変圧縮比のメリット
圧縮比とは、「シリンダー内の空気または混合気(空気+燃料)が、ピストン上昇によってどれくらい圧縮されるのか」の割合を示す指標で、次の計算式で表されます。
圧縮比=(燃焼室容積+排気量)/燃焼室容積
圧縮比が高いほど、エンジンの熱効率は向上します。熱効率が高いということは、燃費と出力が向上します。
しかし、ガソリンエンジンでは圧縮比を上げると、高負荷運転でノッキングが発生しやすくなります。したがって、通常は最もノックしやすい条件で、ノックしない範囲でできるだけ高い圧縮比に設定します。
一方で、一般路走行の部分負荷条件ではノックしにくいので、本来はもっと高い圧縮比に設定するのが理想であり、最適な圧縮比ではありません。
この問題を解決するのが、可変圧縮比です。可変圧縮比機構によって、低負荷~中負荷運転では圧縮比を高く、ノックが発生しやすい高負荷運転では圧縮比を低く設定します。運転条件に応じて、自動的に最適な圧縮比に設定することによって、燃費と出力の両立が実現できます。
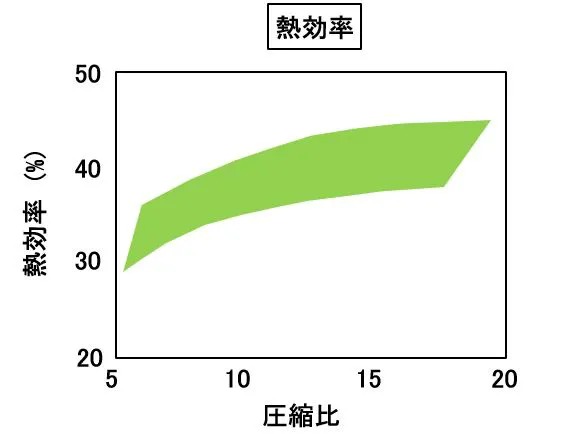
日産の可変圧縮比(VCR)機構
過去にいくつかのVCR(Variable Compression Ratio)機構が提案されましたが、機構の複雑さや耐久性の問題から実用化された例はありません。
実用化された日産のVCR機構は、圧縮比の変更をピストンの上死点高さの変化で行います。上死点とは、上下運動するピストンの最上点のことで、圧縮行程中のピストンがより高い位置まで圧縮することで、圧縮比は上昇します。
この機構を実現するのが、独自に開発した複合リンク方式です。ピストンを支持し、クランクの回転運動をピストンの上下運動に変えるコンロッドの代わりに、3本のリンクをモーターによって巧妙に動かし、ピストンの上死点高さを連続的に変更します。
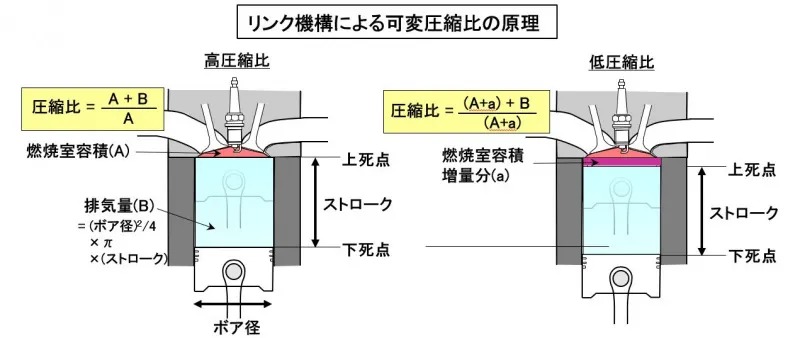
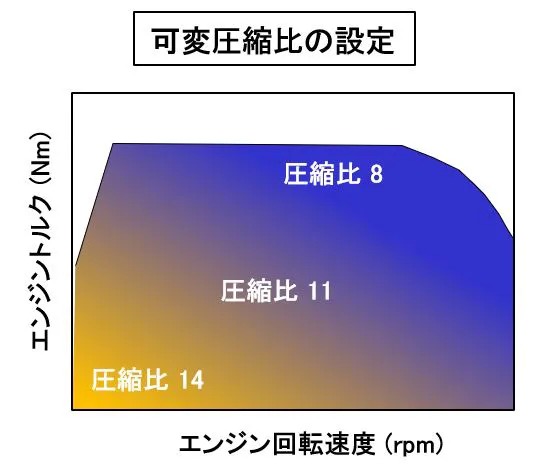
日産VCRの効果
日産は、2018年3月、北米向けのインフィニティのクロスオーバーSUV「QX50」搭載の排気量2.0Lのターボエンジンに、VCR機構を採用しました。
ターボエンジンは過給している分ノックしやすいため、無過給エンジンに比べて圧縮比を下げる必要があります。したがって、VCRの効果がより大きく発揮できます。
ノックしない一般路走行などの低~中負荷運転では、燃費を良くするため高圧縮比14に、ノックが発生しやすい高負荷運転では、ノックが発生しないように低圧縮比8とします。その間の領域の圧縮比は8~14の間をシームレスに変化させます。
すべての運転領域で最適な圧縮比に設定できるVCRのメリットを生かし、熱効率は40%を達成し、従来エンジンに比べて燃費が27%向上したと発表しています。通常は圧縮比が低く、熱効率の低いターボエンジンにとって、熱効率40%は驚異的に高い数値と言えます。
VCRには別の方法も
欧州メーカーは、リンク機構でなく、コンロッド長さを調節する手法によってVCRを実現しようとしています。欧州メーカーでは、リンク機構でなく、コンロッド長さを調節する手法によってVCRを実現しようとする動きがありますが、今のところ実用化されたものはありません。
自動車メーカーが考える、エンジンの熱効率向上のシナリオの中で、最も注目されているのが可変圧縮比エンジンと、HCCI(予混合圧縮着火)エンジンです。
かつては夢のエンジンと言われていた革新的な技術が、実用化レベルになってきました。EVの開発が加速していますが、内燃機関も負けずに進化し続けています。
■予混合圧縮着火エンジンとは
長年、多くのエンジン技術者が、実用化に向けて注力してきたHCCI(予混合圧縮着火)エンジンが、2019年、マツダによってついに量産化されました(新型マツダ3に搭載)。
マツダが開発した「SPCCI(火花点火制御圧縮着火)」を例に取り上げ、その手法や効果について解説していきます。
HCCIエンジン
HCCI(予混合圧縮着火:Homogeneous Compression Charge Ignition)エンジンは、燃料と空気を燃焼室全域で濃度が均一になるように混合して、圧縮による温度上昇によって自己着火させる「多点着火による予混合燃焼」です。
ガソリンエンジンの均一予混合という特性と、ディーゼルエンジンの圧縮着火の特性を併せ持つエンジンです。
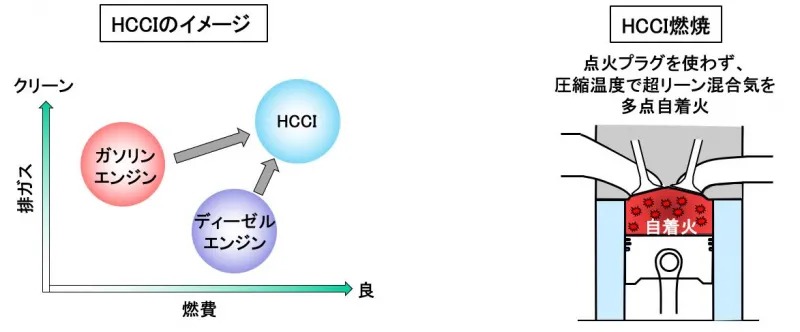
HCCIのメリット
通常の火花点火では燃焼(火炎伝播)できないような超リーンな(薄い)均一混合気を形成し、燃焼室全域で起こる多点圧縮着火の低温燃焼を実現するHCCIには、以下のメリットがあります。
・均一な予混合気の燃焼であるため、ディーゼルのような煤を含んだPM(微粒子状物質)がほとんど発生しません。
・非常に薄い超リーンバーンであるため、スロットル開度が大きくなり、ポンプ損失が低減します。また、燃焼温度が低いため、NOxの生成がほとんどなく冷却損失も減少します。
・燃焼室全体で均一混合気の多点着火が起こるので、未燃損失が少なく完全燃焼しやすいため、熱効率が高くなります。
HCCIの課題
一方、長年実用化を妨げてきた最大の課題は、HCCIが成立する運転領域が限られる、狭いことです。低負荷域では、混合気の温度が低いため安定して着火できず、高負荷になるとノッキングが発生します。ノッキングの発生は、高負荷では燃料量を増やすため燃焼が急激になることに起因します。
圧縮による自己着火であるため、自在に着火時期を制御できないことが解決を困難にしています。
着火時期を制御するため、過給技術や可変動弁機構を活用したEGR導入などが試みられています。広い運転領域でHCCIを成立させるのは難しいので、現時点は後述のマツダ方式のように火花点火方式と切り替えることが、最も現実的な解かもしれません。
マツダのSPCCI(火花点火制御圧縮着火)
マツダは、SPCCI(Spark Controlled Compression Ignition)を採用した次世代エンジンを、マツダ3に搭載して2019年に市場に投入しました。
低速・低負荷の運転領域をHCCI、高速・高負荷の運転領域は通常の火花点火燃焼に切り替える方式です。
低速・低負荷を中心とした実用運転領域では、点火プラグを補助的に使いながら、超リーンバーンの多点圧縮自着火のHCCIを実現しています。
空燃比が30を下回るような運転領域では、理論空燃比の燃焼に切り換え、さらに高速高負荷域では通常の火花点火燃焼にシームレスに切り替える方式を採用しています。
高圧縮比や火花点火制御、可変動弁機構、EGR制御、過給技術などを駆使して、燃焼を制御しています。成果としての燃費向上は、エンジン単体で20~30%程度と予想されています。
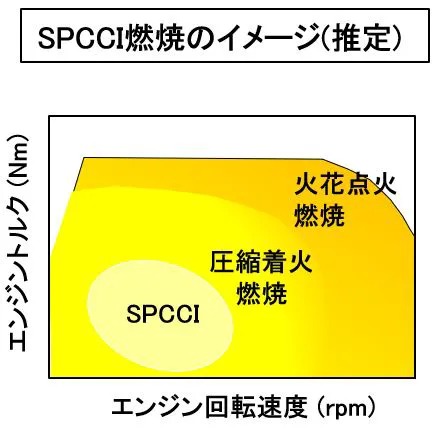
HCCIはディーゼルにもある
ディーゼルエンジンでも、限定的ですがHCCIと見なされる燃焼が実現しています。
一般的には、「低温燃焼方式」と呼ばれ、低圧縮比と大量EGRによって意図的に着火遅れを伸ばして、均一混合を促進する手法です。混合気が均一化されているので、従来のディーゼルのようなリッチな領域が存在せず、煤とNOxがほとんど発生しません。
長年、多くのエンジン技術者が、実用化に向けて注力してきたHCCI(予混合圧縮着火)エンジンが、2019年マツダ新型「マツダ3」の出現によって、前進しました。着火制御の難しさを、火花点火をトリガにして制御する手法によって、一部領域ながら圧縮着火燃焼を実現したのです。
現存するすべての先進技術を組み合わせたマツダのSPCCIは、現時点では現実的なHCCIの姿かもしれません。まだ進化の余地は多いので、今後もさまざまな形態のHCCIが出現してくると思われます。
■可変動弁機構とは
可変動弁機構は、出力向上だけでなく、燃費向上や排出ガス低減のために、多くのエンジンに標準的に採用されています。
各自動車メーカーが独自に開発している可変動弁機構の仕組みや効果について、解説していきます。
可変動弁機構の種類
初期の可変動弁機構は、回転速度に応じて吸・排気弁の開閉時期を変更し、全域で高出力を確保するために開発されました。
弁開閉時期の可変機構だけでなく、弁リフト量の可変機構も開発され、最近では出力向上だけでなく、燃費向上や排出ガス低減のためにも活用されています。
可変機構はメーカーによって異なり、それぞれ独自の名称が付けられていますが、大きくは3つに分類できます。
カム位相型(トヨタ「VVT-i」、BMW「VANOS」など)
典型的な手法は、カムシャフト先端のスプロケット部に、位相角変更用の油圧機構を備えたタイプです。電動化によって過渡時にも応答良く作動するようになりましたが、開弁時期とともに閉弁時期も変わるので使い方が限定されます。
カム切り替え型(ホンダ「VTEC」、ポルシェ「VarioCam Plus」、アウディ「AVS」など)
カムプロファイルの異なる複数のカムシャフトを切り替える機構です。カム位相型と組み合わせることによって、最適な弁開閉時期と開弁期間、弁リフト量を制御できます。
油圧駆動型(FCA/アルファロメオ「MultiAir」)
カム山で駆動させるのではなく、カム山がポンプを押して発生させた油圧で吸気弁を駆動します。弁駆動の自由度が高く、理想的なプロファイルを実現できますが、油圧系が複雑でコスト高であるため普及には至っていません。
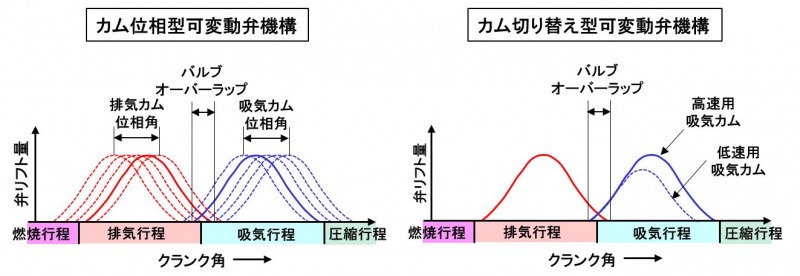
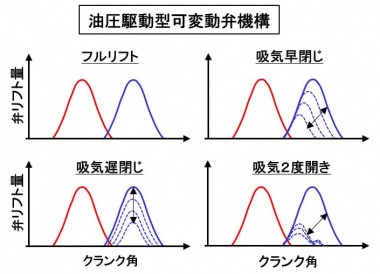
その他、進化型の弁開閉時期&弁リフト量の連続可変機構として、トヨタ「バルブマチック」、日産「VVEL」、BMW「Valvetronic」、三菱「SOHC型MIVEC」などがあります。出力制御だけでなく、弁リフト量によって吸気量を制御できるので、ポンプ損失の低減など活用の範囲が広がります。
可変動弁機構のメリット
低速の全負荷条件では、開弁期間を短く(閉弁を早く)して弁リフト量を小さ目にして低速トルクを向上させます。一方、高速域では開弁期間を長く(閉弁を遅く)、弁リフト量を大きくして最高出力を向上できます。
同時に、高速域では吸・排気弁のオーバーラップ期間を長くして、排出ガスの抜けを改善することによって出力向上を図ります。
燃費を重視する部分負荷では、吸気弁を遅閉じすることによってポンプ損失を低減させ、燃費を向上させます。また吸・排気弁のオーバーラップ期間を長くして、燃焼ガスをシリンダー内に残留させる内部EGRによってポンプ損失を減らし、燃費と排出ガス性能を改善できます。
エンジン冷態時は、触媒温度が低いため、排出ガスの浄化効率が低下します。吸・排気弁オーバーラップ期間や排気弁閉時期の調整によって、触媒温度の暖気を促進します。
最近の可変機構の高速かつ高精度制御の実現によって、多様なメリットが生み出され、可変動弁機構は、多くのエンジンで標準的に採用されています。
オーバーラップ期間
空気の流れには慣性があるので、排気弁は上死点後に閉じ、吸気弁は上死点前に開くようにします。この上死点前後で、排気弁と吸気弁の両方が少しだけ開いている期間をオーバーラップ期間と呼びます。
オーバーラップ期間が短いと、燃焼室に残留する燃焼ガス(残留ガス)が減り、オーバーラップ期間が長いと、残留ガスが増えます。出力向上や燃費向上、排出ガス改善など目的によって、オーバーラップ期間を可変動弁系機構によって適正に制御します。
可変動弁機構は、吸・排気の効率やシリンダー内の温度・圧力、内部EGR量など、出力や燃費、排出ガス性能を決定する重要なパラメーターを制御できる機構です。
直噴ターボや可変圧縮比、HCCIなどの先進技術には、必要不可欠の技術です。
■気筒停止エンジンとは
1980年代には大排気量エンジンに採用されたものの、その後存在が薄らいでいった休筒システムですが、燃費/CO2規制強化に対応する手段として、採用するモデルが登場しています。
休筒システムの機構とメリット、今後の普及の可能性について解説していきます。
休筒(気筒停止)の歴史
休筒は、作動中のエンジンの特定気筒を休止、燃焼を休止させることで、アイドルや低速運転の燃費を低減するシステムです。
初めて休筒を採用したのは、1981年のGMキャデラックV8エンジン、日本では1982年の三菱4気筒「MD(可変排気量)」エンジンです。その後も採用例は少数ですが、欧州と米国メーカーが継続的に採用し、日本では2003年にホンダがVTECをベースにした休筒システム「VCM(可変シリンダーマネージメント)」をアコードV6エンジンに採用しました。
2012年にVWゴルフ1.4Lがダウサイジング直噴ターボに採用、さらに2018年に入ってマツダがCX-5のSKYACTIV-G 2.5Lに採用し、再び注目され始めました。
休筒の手法
休筒を実現する代表的な手法は、ロッカーアームを空打ちさせる手法と、弁リフト量の可変機構を利用してゼロリフトカムに切り替える手法です。
これらの手法によって、特定気筒の吸・排気弁の駆動を停止(ピストンは作動)して、シリンダー内の燃焼を停止させます。点火プラグの放電は、再燃焼(作動)時の汚れによる失火を回避するため継続しておきます。
吸・排気弁が駆動しないのでシリンダー内は密閉状態ですが、ピストンで圧縮して膨張させるという正負の仕事がバランスするために、損失は発生しません。密閉することによって、シリンダー内の温度が維持され、再燃焼しやすくなる効果もあります。
当然ですが、ピストンの往復運動による摺動抵抗は発生します。
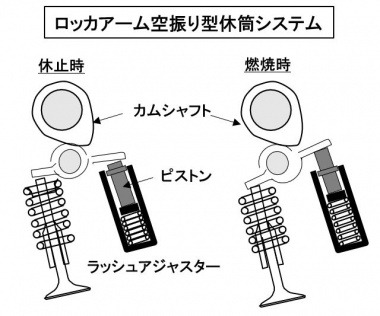
休筒のメリットとデメリット
特定の気筒を休止させることは、見かけ上、排気量を小さくするのと同じです。したがって、同じ出力を得るためにスロットル開度は大きくなり、ポンプ損失が低減します。さらに、燃焼気筒が減ることによって、排気損失や冷却損失も減少することから、総合的にはアトキンソンサイクルやクールドEGRと比べても同等の効率が実現できます。また、弁駆動を停止するため、駆動損失の一部も減少します。
課題は、当初から市場で不満が多かった切り替え時のショックと休筒時の振動です。
切り替えショックについては、直噴化や制御の高度化によって最近の採用例ではほぼ解消されています。振動については、4気筒であれば2気筒作動に、6気筒であれば4気筒ないし3気筒作動になるため、不利になることは否めません。しかし、フライホイールやクラッチディスク、エンジンマウントなど、振動低減の要素技術の進化によって、改善されつつあります。
代表的な休筒システム
弁リフト量の可変機構を利用してゼロリフトカムに切り替える手法としては、ホンダのVTECをベースにした「VCM」や、VWのAVS(アウディ・バルブリフトシステム)ベースの「ACT(アクティブシリンダーテクノロジー)」などが代表例です。
ロッカーアームを空打ちさせる手法は、ダイムラー「AMG」のV8や、マツダCX-5のSKYACTIV-Gで採用されています。
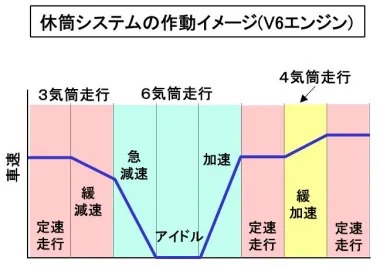
1980年代に休筒システムがブームになったときには、振動の問題もあり、主として6気筒以上の大排気量エンジンで採用されていました。
欧州では4気筒や3気筒で採用した例が増えています。ただし、休筒が得意な(燃費が良い)のは定常の低速走行であるため、日本の走行事情では期待するほどメリットが出にくいという難点があります。
■廃熱回収とは
現在、ガソリンエンジンの熱効率は20~40%程度で、残りのほとんどは熱として捨てられています。この排熱の一部を回収するのが、排熱回収システムです。
すでに実用化されている排熱回収技術と今後期待される技術について、解説していきます。
排熱回収の種類
さまざまな熱効率向上の技術が実用化されていますが、それでも燃料の持つ発熱量のうち、エンジンの仕事として引き出せているのは20~40%程度です。残りのほとんどは、熱として捨てられています。その排熱の一部を回収して再利用とするのが、排熱回収です。
排熱回収には、直接排気熱を熱として回収する排気熱回収システムと、蓄熱材を利用して一時的に熱を保持して再利用する蓄熱システム、排気熱で発電して電気エネルギーとして回収する熱電変換システムがあります。
この中で、実用化されているのは、排気熱回収システムと蓄熱システムです。
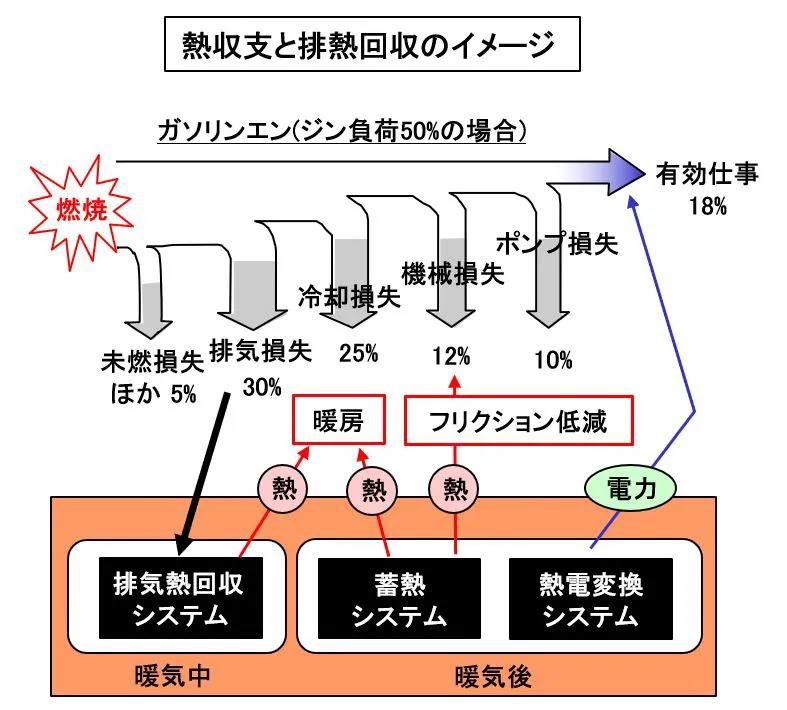
排気熱回収システム
排熱回収技術の中で実用化が進んでいるのは、排気管に熱交換器を搭載して、直接、排気ガスの熱を回収する排気熱回収システムで、HEVを中心に採用されています。
HEVでは、頻繁にアイドルストップによって燃費を低減しています。しかし、冷態時は室内の暖房を維持するために、アイドルストップはしません。燃費の良いHEVで冷態時の燃費悪化が目立つのは、これが要因です。
一般的な排気熱回収システムでは、排気系の触媒下流に排気熱をエンジン冷却水に回収する熱交換器を設置します。これにより、暖気が促進されてアイドルストップが早く作動し始め、実燃費が改善されます。
熱交換器の効率を上げるためには、流路をある程度絞る必要があり、圧損が大きくなります。排気回収を行うのは暖気中だけなので、それ以外の通常運転では、流路切り替えバルブによって熱交換器をバイパスさせます。
蓄熱システム
トヨタの4代目プリウスでは、一般の魔法瓶の真空断熱効果を利用した蓄熱タンクを装備した蓄熱システムを採用しています。
エンジン水温が所定温度を超えると、蓄熱タンクに温水を格納して蓄熱します。この温水は、エンジンが始動する前に、エンジンに供給して暖気を促進します。暖気時間が大幅に短縮されて燃費が改善され、さらにHC排出量も低減します。
熱電変換システム
2種類の異なる金属または半導体を接合した熱電変換素子は、両端に温度差があるとゼーベック効果(物体の温度差が電圧に直接変換される現象)によって起電力が発生します。これを利用した熱電変換システムを排気系に装備して200~300W程度の電力が回収できれば、市街地走行で3~5%の燃費改善が期待できます。
E化が進むと排熱や蓄熱技術の貢献度は下がります。ただし、エンジンはそう簡単にはなくならないから、テーマとして今後も重要です。
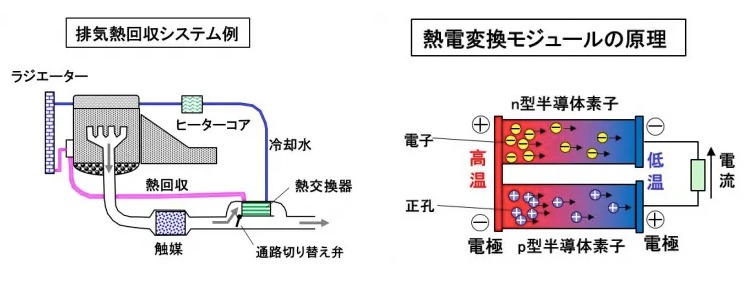
熱機関全体の課題
排熱利用は、車に限らず熱機関では非常に重要な課題です。NEDO(新エネルギー・産業技術総合開発機構)の「未利用熱エネルギー革新的技術研究組合」には多種のメーカーが参加して、以下の3つの技術について研究開発を行っています。
熱の使用量を減らす技術「蓄熱・遮熱・断熱」と、熱を変換して利用する技術「熱電変換・排熱発電」、熱を再利用する技術「ヒートポンプ」の3つです。
自動車メーカーの研究開発のシナリオの中に、排熱回収は必ず挙げられる永遠のテーマです。電動化が進む中では熱を電気に変化する技術が、将来活用できる有望な技術ではないでしょうか。
(Mr.ソラン)
クリッカー自動車用語辞典 https://clicccar.com/glossary/