■自動車メーカーよりサプライヤーや研究機関にこそメリットのあるモデルベース開発。社員数2桁の中小企業での活用例もある
2021年9月24日、日本のものづくり、日本の自動車産業にとってターニングポイントとなりえる大きな発表がありました。
それがMBD(モデルベース開発)推進センターの発足です。
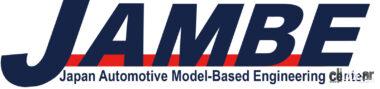
立ち上げ時の運営委員を構成するのは、株式会社アイシン、ジヤトコ株式会社、株式会社デンソー、パナソニック株式会社、三菱電機株式会社というサプライヤー5社と、株式会社 SUBARU、トヨタ自動車株式会社、日産自動車株式会社、、本田技研工業株式会社、マツダ株式会社の自動車メーカー(OEM)5社の計10社。
同センターの基本理念は、”MBD技術を広く普及展開し、モデルを用いた高度なすりあわせ開発「SURIAWASE2.0」を実現することにより、日本の自動車産業の国際競争力向上に貢献する”というものです。
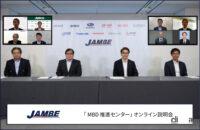
このように日本のものづくりをレベルアップさせると期待されている「モデルベース開発」とは、どのようなものでしょうか。ひと言で表現すれば「経験を数式にする」ということです。
MBD推進センターの発足にあたり、ステアリングコミッティ委員長の人見光夫 氏はモデルベース開発のメリットを『三角形の面積を測るという仕事があったとして、毎回方眼紙を当ててマス目を数えるのか、公式を編み出せば次からは簡単になるようなもの』と表現しました。
技術要素をモデル化することで実際に試作したりせず、プログラム上で開発できるようになるため、開発費が安価になり、また開発速度もアップするというメリットしかない方法がMBDというわけです。
実際、マツダがSKYACTIVテクノロジーを一気に開発できた背景にはMBDがあったというのは周知の事実であり、それは同社の強みにもなっています。当然ながら他の自動車メーカーもMBDを積極的に活用しています。
しかし、そこで問題が起こります。各社が異なるモデルを使っていることで、サプライヤーなど複数社と取引のある企業は、OEMごとにあわせたモデルを用意しないといけなくなったのです。これはコスト面で非常にもったいない話です。
OEMが共通のモデルを使えばサプライヤーの開発費は抑制できますし、パーツ開発のスピードも上がります。
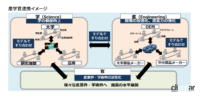
そこに、MBD推進センターが発足した意味があります。
モデルの内容は各OEMによって異なっていても、ルールを共通化することで、サプライヤーがMBDを利用しやすくすることで普及を促そうというわけです。同時に、共通言語化したモデルを大学の研究室などでも利用することで産学官の連携がより密になることも期待されます。
とはいえ、MBDの導入にはコストと人材育成の両面でハードルが高いのでは? という課題も浮かんできます。
そうした点について尋ねてみたところ、MBDの経験豊富なマツダに関わるサプライヤーの例として、株式会社ヒロテックツーリング(従業員32 名、資本金 3000 万円)という、プレス金型の中小企業においてMBDを活用した事例があるということを教えてもらいました。
同社のケースでは、、ひろしまデジタルイノベーションセンター(公益財団法人ひろしま産業機構)にあるプレス成形シミュレーションソフトの安価な共用サービスや広島経済同友会が運営するデジタルものづくり塾(地場企業群が先行企業などのアドバイザーによる支援を受けつつ共同でデジタルツールを学習・実践する場)に参加することなどで、MBDの導入に成功したといいます。
MBD推進センターによるルールの整備と中小企業でもMBDを導入しやすくするための様々なサポートが加速すれば、日本のものづくりは同じモデルによって進められることになります。
はたして、MBDによって日本のものづくりはどれほどレベルアップをすることができるのでしょうか。日本の基幹産業である自動車製造からはじまるMBDの広がりに大いに期待したいと思います。