目次
■コストと生産性が課題だが、軽量かつ高強度で現在最も注目されている先端材料
●レース車のカウルやフレームなどに使われ、量産車でも徐々に普及中
現在クルマとバイクにとって理想的な軽量化材料は、軽くて強いCFRP(炭素繊維強化プラスチック)です。コストと生産性に課題はあるものの、高性能の高級バイクでカウルやフレーム、ホイールなどに使われています。
現在最も注目されている先端材料CFRPについて、解説していきます。
●CFRPの特徴
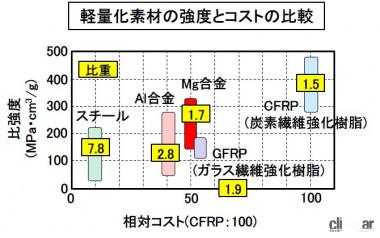
CFRPは、炭素繊維を樹脂で固めた炭素繊維強化プラスチックです。加圧成形し高温で熱処理を施して高強度を実現しています。高価ですが、軽くて強い、硬くて寸法精度が高いなどの特徴から、航空機やロケット、近年はクルマ、バイクへの適用が進んでいます。
CFRPの比重は1.5程度でスチール(比重7.8)の約1/4、強度(強度/比重)はスチールの5倍以上です。また融点は、スチールの1536℃に対して、CFRPは2500℃以上であり、いかに優れた素材かが分かります。
●CFRPの課題
最大の課題は、コストと生産性です。
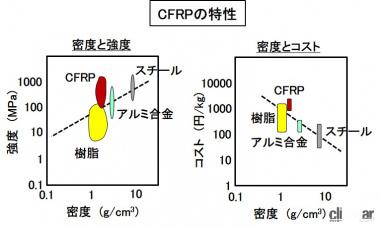
CFRPのコストは、スチールの10倍以上です。
一般的なのは、航空機のフレームなどに使われる、エポキシ樹脂などの熱硬化樹脂に炭素繊維を混ぜて造る熱硬化性CFRP(ドライカーボン)です。ただし、これは高温高圧の圧力釜、オートクレーブを使って成形するため、加工終了まで2~4時間かかり、大量生産には向きません。
現在クルマやバイク用として開発が進められているのは、熱可塑性樹脂を使うCFRP(ウェットカーボン)です。CFRTP(炭素繊維強化熱可塑性樹脂)と呼ばれ、熱硬化性CFRPよりも成形時間を大幅に短縮でき、大物ブレスの成形でも数分以内、小物部品であれば30秒以内で成形できます。
これなら大量生産も可能なので、開発が加速され採用が増えています。
●最初はレース車に採用
バイクへのCFRPの適用は、レース車から始まりました。1978年には、ホンダの耐久レーサーRB1000でCFRPのカウルが採用され、1981年にはMotoGPのNR500でCFRPのホイールとフロントフォークのインナーチューブに、翌年にはスイングアームに採用されました。
この時、ブレーキはカーボン製のディスクブレーキを採用しています。これは、CFRPとは異なる炭素繊維を炭素で固めた硬くて剛性の高い、しかも軽くて熱にも強い「炭素繊維強化炭素複合材」です。鋳鉄製ディスクに対して、質量は約半減、1500℃以上の高温にも耐え、耐摩耗性に優れており、300km/h以上のスピードで走行するレース車のために開発したディスクです。
ただし、最近はMotoGP用としてCFRPの採用例はなく、2009年にドゥカティがモノコックフレームで採用したぐらいです。適度なしなりがなく柔軟性が欠けることが、敬遠される理由です。
●市販車への適用例
バイクへのCFRP適用で代表的なのは、カウルなど外装品とホイール、サイレンサー、各種カバー類ですが、CFRPは高価なため多くは純正品でなくアフターパーツです。
少数ですが、純正品でボディフレームやスイングアームに適用したモデルも出現しています。
ヤマハの電動トライアルバイク「TY-E」は、CFRPのモノコックボディを採用。BMWは、モトラッドHP4RACEでメインフレーム全体をCFRPで構成しています。また、ドゥカティの2021年新型「ディアベル1260ランボルギーニ」や「パニガーレV4SP」では、エアインテークやサイレンサーカバー、スポイラー、フェンダーなどでCFRPを多用しています。
CFRPは、プラスチックの軽量と高い成形性に加え、繊維の持つ高強度と高剛性を併せ持つ理想的な素材です。クルマでは適用が加速されていますが、車両価格の低いバイクでは高コストがネックとなっています。当面は高性能な高級バイクに適用は限られますが、生産性が向上して使用量が増えれば、コストが下がり採用が進むと思われます。
(Mr.ソラン)