目次
■車の開発とは
ニューモデルの開発では、商品構想を始めて市場に出荷するまでに通常5~6年を要します。多種多様な市場の要求に応えるためには、車の開発コストを下げる、開発期間を短縮することが必要です。
車づくりの開発の流れと開発の効率化の試みについて、解説していきます。
車の開発の流れ
車の開発は、大別して企画フェーズ、開発フェーズ、生産準備フェーズに分けられます。
・企画フェーズ
商品企画は、車の狙いや用途、ターゲット市場とターゲットユーザーなど、どのような車かを大まかに定義します。
・開発フェーズ
パワートレインや新技術については個別の確認試験を行い、それと並行して車としての評価や確認は試作車で行います。さまざまな条件で走行させて問題を抽出して、設計と試作、実験を繰り返すことによって、機能や性能、信頼性を向上させます。
デザインは、CAD(コンピューター設計支援)/CAM(コンピューター製造支援)など、さまざまな開発ツールの導入によって、デジタルモデルを主体に玉成します。
・生産準備フェーズ
試作段階の設計から徐々に生産に向けた設計へ移行し、各種生産設備や型・治工具など生産に必要な準備を行います。
生産トライアルを何回か行い、品質を確保できることが確認できれば、正式に生産を開始します。
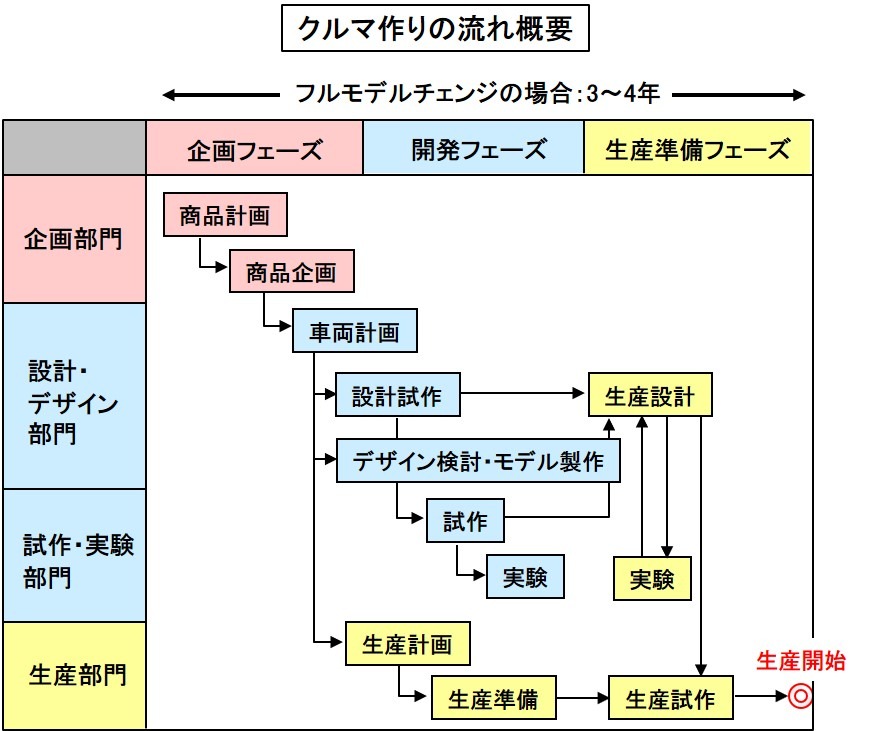
プラットフォーム戦略(モデルベース化)とモジュール化
自動車メーカーは、ユーザーの多様性や環境規制等の厳しい要求に、低コストで効率良く応えるため、プラットフォームの共用化に取り組んでいます。プラットフォームとは、ボディ内外装部とアッパーボディを除いた骨組み(土台)を指します。
最近は、同一セグメントだけでなく、セグメントを超えたプラットフォームの共用化に積極的に取り組んでいます。
プラットフォーム戦略の中核であるモジュール化は、限りある開発リソースを有効活用して、多様な車種を開発するための開発手法です。車両を4~5のブロック(モジュール)に分割して、部品の共用化を図った上で、「レゴブロック」のように組み合わせて目標とする車を完成させます。
VWのプラットフォーム構想MQBやルノー・日産のCMF、トヨタのTNGAは、車種やセグメントを超えて部品を共通化して、コスト低減と開発効率の向上を実現しています。
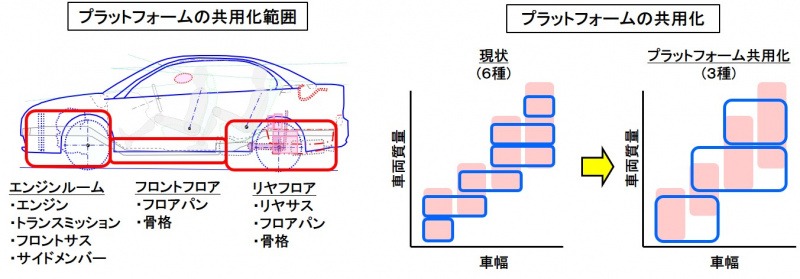

モデルベース開発(MBD)
モデルベース開発とは、プログラム仕様書に相当する仕様モデルを作成し、そのモデルをベースにシミュレーションを活用する開発手法です。開発期間の短縮とソフトウエアの品質を向上させる効果があります。
紙の仕様書の代わりに制御の流れを仕様モデルで表現し、検証を繰り返すことで、システムとソフトウエアの完成度を高めます。その後、自動生成機能によってソースプログラムを作成して実機に書き込み、制御対象のシステムと接続して検証します。
最終的には、システム全体を実車で検証してプログラムを完成させます。
デザインのデジタル開発
車の機能開発と同様、デザイン開発もCAD(コンピューター設計支援)/CAM(コンピューター製造支援)などの導入によって、デジタルモデルを主体とした開発へと進化しています。
・まずはデザインのコンセプトを反映したイメージスケッチを描きます。
・イメージスケッチの中から選ばれたデザイン案を、CADによってより具体的なデザインに絞り込み、レンダリング(完成予想図)を完成させます。
・レンダリングを図面化して、3次元CADのデータを作成します。
・この3Dデータをもとに、クレイモデルが製作され、修正を繰り返しながら完成させます。
・デザインの最終評価は、クレイモデルをベースに艤装も樹脂やフィルムなどで仕上げたハード(樹脂)モデルで行います。
車づくりは、試作と試験を繰り返す従来のすり合わせ開発から、コンピューターを活用した設計(CAD)や解析、シミュレーション技術(CAE)を駆使した開発プロセスに大きく進化しています。
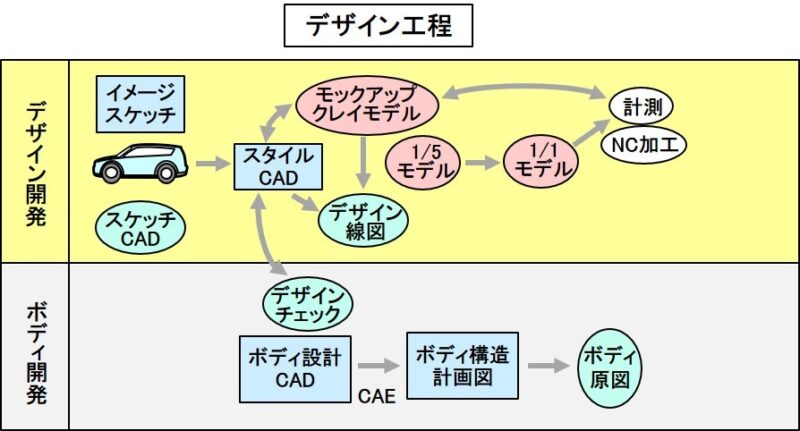
本章では、車の開発の流れ、開発プロセスについて、詳細に解説していきます。
■車づくりの流れとは
最近の車には、さまざまな最新技術が搭載され、開発に多くの工数と時間を要します。そのため自動車メーカーは、コンピューターを活用した設計(CAD)や解析、シミュレーション技術(CAE)を駆使し、開発効率の向上に取り組んでいます。
車づくりの流れ、開発プロセスの概要について、解説していきます。
車開発の流れ
自動車メーカーは、経営計画に基づいて長中期商品計画と短期商品計画を立案して、それを毎年更新します。具体的には、どのようなモデルをどこで生産し、どこでどれくらい販売するか、仕向け地ごとの収益はどうなるかなどです。
商品計画の中で、コンセプトが承認されたモデルのプロジェクトが、生産化に向けて開発をスタートさせます。生産されるまでの流れは、大まかには企画、開発、生産準備の3つのフェーズに大別されます。
車づくりは、内容や規模によって以下のように分類されます。
・ニューモデル(5~6年程度)
全く新規の車種開発です。
・フルモデルチェンジ(3~4年程度)
既存車種の全面改良で、デザイン、ボディ、パワートレイン、足回りまで変更する場合が多いです。
・マイナーチェンジ(2~3年程度)
車種ライフの途中に商品力強化のため、一部(例えば、ボディやパワートレインなど)を変更します。
・フェースリフト(1~2年程度)
マイナーチェンジよりさらに小規模な変更です。
企画フェーズ
企画部門が担当して、商品企画と製品企画を行います。
商品企画は、車の狙いや用途、ターゲット市場とターゲットユーザーなど、どのような車かを大まかに定義します。商品企画をベースにして、開発を本格的に進めるために具体化するのが製品企画です。
例えば、車種構成や基本レイアウト、寸法、質量などの基本構成、目標性能、原価、開発費用と工数などを明確化します。
開発フェーズ
設計部門とデザイン部門、試作部門、実験部門が担当します。
パワートレインや大物技術は、プロジェクトとは別に先行的に研究開発を行っています。プロジェクトは、車の目標を達成するためにどんなパワートレインを使うか、どのような先進技術を使うかを決め、車両本体の開発と合流させます。
コンポ単体の確認試験も行いますが、車としての評価や確認は試作車で行います。さまざまな条件で走行させて問題を抽出して、設計と試作、実験を繰り返すことによって品質と信頼性を向上させます。
現在は、シミュレーション(CAE)技術が進み、構造や強度、衝突試験もCAEを利用した設計ができるようになりました。おかげで、試作車台数や試験数の大幅な削減を実現しています。
デザインはCADを駆使して検討を進め、モックアップは最終確認程度で済みます。インパネ形状などは、3Dプリンターを使って検討用の試作品ができるので、開発期間が短縮されてコストも低減できます。
生産準備フェーズ
開発の進捗に応じて、試作段階の設計から徐々に生産に向けた設計へと移行します。
生産化のために必要な生産部門からの要望を開発部門にフィードバックし、各種生産設備や型・治工具など生産に必要な準備を行います。
生産トライアルを何回か行い、品質を確保できることを確認できれば、正式に生産が開始します。
かつては大量の試作車を製作して、各機能の確認試験や耐久性試験を実施していました。CAEによる解析技術の進化によって、試作車の台数も減らすことができ開発期間と開発費を削減できるようになりました。
さらにCAEによる開発が進めば、ほとんど試作車を作ることなく最終確認車の評価だけで、車の開発が完了するかもしれません。
■プラットフォーム戦略とは
ユーザー嗜好の多様性や環境規制等の要求に応えるために、さまざまなボディ形状やパワートレイン、安全機能の搭載が車に求められています。自動車メーカーは、この多様な要求に応えるため、プラットフォームの共用化戦略に取り組んでいます。
プラットフォーム戦略の狙いやメリットについて、解説していきます。
車のプラットフォーム
プラットフォームには、「土台」という意味があります。プラットフォームとは、広義の意味ではどの部分ということでなく、基本構成部分を指す概念的な用語です。
狭義の意味は、一般的にボディ内外装部とアッパーボディを除いた骨組み(土台)のシャシー部を指します。
車のシャシーは、多数のプレス部品を組み合わせて溶接した大型部品なのでコストがかかります。したがって、新型車を開発するたびにプラットフォームを作らず、同じセグメントの車では極力流用するのが一般的です。
2010年以降、自動車メーカーはさらなる開発効率の向上やコスト低減を狙って、セグメントを超えたプラットフォームの共用化に取り組んでいます。
この場合のプラットフォームは、広義の意味で様々な基本構成部分を指します。
以下、広義のプラットフォーム戦略について解説します。
プラットフォーム戦略の狙いと効果
プラットフォーム戦略は、「標準化」、「共用化」、「モジュール化」の3つの重要な要素で構成されます。この3つの要素が、多くのメリットをもたらします。
・標準化
共通のルールに基づいた作業標準や設計標準に代表されるように、部品のバラツキ低減など、品質を確保する有効な手段です。
・共用化
複数の車で部品を共用化する「部品共用化」は、量産効果によるコスト低減の常套手段です。セグメントの枠を超えてラインを共用化する混流生産ができるので、生産コストも低減できます。
・モジュール化
車全体をいくつかの独立したブロック(モジュール)に分割する手法で、分業や外製化によってモジュールごとに並行開発ができます。さらに、さまざまなモジュールを「レゴブロック」のように組み合わせることができるので、短期開発で車種のバリエーションを増やせるのが最大の特長です。
プラットフォーム戦略の課題
多くのメリットがあるプラットフォームの共用化ですが、一方で、過度に進めると車の商品力が低下する、個性がなくなるという問題があります。
プラットフォームの共用化は、部品の寸法や選択などに制約を受けるため、車の仕様や開発の自由度が下がり、その車の特徴や個性を出すのが難しくなります。
プラットフォームの共用化と車の商品力のバランスは、共用する部品の範囲をどこまで設定するかで決まります。言い換えると、ひとつのプラットフォームでいくつの車種をカバーするかの設定が重要です。
プラットフォームの共用化によって、品質を確保しながら低コストの車を短期間で開発し、同時に商品力向上も実現できるようになりました。
燃費の良い安全な車をリーズナブルな価格で提供できるのも、プラットフォーム戦略が貢献しています。
■各社のプラットフォーム戦略
2010年以降自動車メーカーは、ユーザーと市場の多様かつ高度な要望に応えるため、車作りを根本から見直しています。具体的には、限られたリソースで短期に高品質の車を開発するためのプラットフォーム戦略の構築です。
VWとルノー・日産、トヨタの3大メーカーが取り組んでいるプラットフォーム戦略について、解説していきます。
3大メーカーの取り組み
2010年以降、自動車メーカーはさらなる開発効率の向上やコスト低減を狙って、セグメントを超えた広義のプラットフォーム戦略に取り組んでいます。中でも、車全体を独立したブロック(モジュール)に分割して開発するモジュール化は、プラットフォーム戦略の目玉です。
3大メーカーが取り組んでいるプラットフォーム戦略について、解説します。
フォルクスワーゲン(VW)「MQB(モジュラー・トランスバース・マトリックス)」
プラットフォーム戦略に初めて本格的に取り組んだのは、2012年に発表されたVWのプラットフォーム構想MQBです。セグメントを超えて主要部品を共通化し、生産コストと開発コストの低減を実現しています。
エンジンの搭載位置、トランスミッション搭載やサスペンション取り付けの共通化だけでなく、電装部品や電子制御システムなども共通化し、電子プラットフォームもモジュール化しています。
MQBは、ポロやゴルフ、パサートなどのVW以外にも、アウディのTTやA3などにも適用されています。
ルノー・日産「CMF(コモン・モジュラー・ファミリー)」
CMFでは、車体を「エンジンコンパートメント」、「コクピット」、「フロントアンダーボディ」、「リヤアンダーボディ」の4つのモジュールと、これに電子部品をまとめた「電子アーキテクチャー」を加えた5つのモジュールで分割して、車両を構成します。
それぞれのモジュールには複数のバリエーションがあるため、それらを組み合わせることで自由に車のサイズやスタイルを変更できます。
最大の狙いは、互換性のあるモジュールによって、ルノー、日産アライアンスのシナジー効果を引き出すことです。そのため、プラットフォームの共有化を一気に採用するのではなく、共有できる部分のコンポーネントをまず共有することを優先させています。
購買から開発までシナジー効果を引き出し、2015年には5000億円に相当する効果を得ました。
トヨタ「TNGA(トヨタ・ニュー・グローバル・アーキテクチャー)」
商品力向上とコスト低減の二律背反を両立させることを目標とし、企画、開発、調達、生産のすべての工程から、全体最適を図るプラットフォーム戦略です。
セグメントごとのプラットフォームは残すものの、同じプラットフォームを使う複数の車種を同時に開発する「グルーピング開発」によって、互換性のある部品やシステムを開発するのが特長です。
個別車種の最適開発から脱却して、モジュール化した部品戦略により部品の種類を減らしてコストを低減します。そのコスト低減分を、商品力の向上に振り向ける考え方です。
またTNGAはプラットフォームのモジュール化だけでなく、走行性能や運動性能、乗り心地など、車の基本性能についても、さらなる向上を実現させる基盤として重要な役割を担っています。
TNGAの第1弾は2015年のプリウスで、その後クラウン、カムリ、C-HRなどに展開しています。
VWとルノー・日産、トヨタの3大メーカーが進めるプラットフォーム戦略には多少の違いはありますが、部品の共用化とモジュール化をベースとしてコスト低減と商品力向上を目標としている点は共通です。
■モジュール化とは
プラットフォーム戦略の中核であるモジュール化は、車両を4~5のブロック(モジュール)に分割して部品の共用化を図る手法です。「レゴブロック」のようにブロックを組み合わせて、目標とする車を完成させます。
モジュール化の狙いやメリットについて、解説していきます。
車のモジュール化
1990年代に出現したモジュール化は、開発効率のためではなく、生産ラインの効率向上のために採用された手法でした。
個々の部品をメインラインで順番に組み付ける従来の方式でなく、組付けられる部品を機能ごとにブロック化(モジュール化)して、車を組み立てます。モジュールごとに分業や外製化ができるので、生産効率を高めることができます。
2010年頃から各社が取り組み始めた開発のためのモジュール化は、プラットフォーム戦略の中の目玉として注目されました。
車両を独立した機能を持つモジュールに分割して、それぞれを並行開発して最終的に組み合わせる手法です。さまざまなモジュールを「レゴブロック」のように組み合わせることによって、短期開発で車種のバリエーションを増やせるのが、最大の特長です。
モジュール化の狙い
車は、数万にもおよぶ多くの部品の機能の組み合わせによって、性能が実現されています。仕様の異なる派生車を開発する場合、特定の部品を変更すると関りのある周辺部品も仕様変更が必要になり、多大な工数と時間がかかってしまいます。
モジュール化では、比較的関係の弱い独立したモジュールに分割して、機能の変更をできるだけモジュール内でできるようにします。互換性があり、ある程度独立して機能を果たすモジュールの組み合わせで、派生車などの開発をモジュール単位で行えるようにします。
結果として、短い開発期間と少ない開発工数で、多くの商品種類を生み出すことが可能となります。
モジュール化の取り組み
一般的なモジュール化では、車両を「コクピット」、「フロントアンダーボディ」、「エンジンルーム」、「リヤアンダーボディ」の4つのモジュールに分けます。またそれぞれのモジュールは、例えばA型コク ピット、B型コクピット、〇〇型コクピットのように、3~6種類のバリエーションで構成されます。
車の目標性能や機能に合わせて、各モジュールの中の複数のバリエーションの中から1つを選択して、モジュールを組み合わせて目標とする車(例えば、D型コクピット、B型フロントアンダーボディ、A型エンジンルーム、A型リヤアンダーボディ)を完成させます。
VWのプラットフォーム構想MQB(モジュラー・トランスバース・マトリクス)やルノー・日産のCMF(コモン・モジュール・ファミリー)、トヨタのTNGA(トヨタ・ニューグローバル・アークテクチャー)などは、プラットフォーム戦略の中でモジュール化を推進しています。
車種やセグメントを超えた部品の共通化によって、部品の種類を減らして開発費で20~30%程度、コストで20%程度低減していると予想されます。
VWやトヨタ、ルノー・日産などグローバルで戦う大規模メーカーは、開発工数を増やさず、世界各国のユーザー・ニーズに合致した車を作ることが求められています。
それを実現するのが、限られた工数で短期間に多くの派生車を開発するモジュール化技術です。
■モデルベース開発(MBD)とは
自動車メーカーは、試作車数を減らして開発期間を短縮するため、多様な制御にモデルベース開発(MBD:Model Base Development)を積極的に活用しています。
制御開発の中核となっているモデルベース開発について、解説していきます。
従来のシステム開発
車には、さまざまな部品やシステムを作動させるために100個前後のマイコン(ECU)が搭載されています。センサーから得られた情報をもとに、マイコンの制御プログラムによってさまざまなシステムを作動させます。
したがって、制御プログラムの仕様書(テキストやフローチャート)の量は、車全体で膨大となります。
従来の制御開発では、まず仕様書に基づいてソフトウエア設計(基本設計から詳細設計)を行い、プログラムを作成します。
その後、単体テストやモジュールテスト、総合テストが行われ、さらに実機を使って仕様書通りに作動するのかを検証していました。
この検証は、ハードウエアに合わせて何回もやり直すので多大な工数と時間がかかります。また、それぞれの工程の検証は、人が行うためエラーや漏れが出る、個人の技量に依存するという問題が起こります。
モデルベース開発
モデルベース開発とは、実際に車で起こる各機能部品の現象を数理モデルで表して、コンピューターでシミュレーションを繰り返して、制御やシステムを作り込む開発手法です。
従来の開発方法に対して、大幅な開発期間の短縮とソフトウエアの品質を向上させることができます。
紙の仕様書の代わりに制御の流れを仕様モデルで表現して、システム設計の十分な検証を行った上でソフトウエア設計に移り、そこでも検証を繰り返すことで完成度を高めます。その後、自動生成機能によってソースプログラムを作成して実機に書き込み、制御対象のシステムと接続して検証します。
最終的には、システム全体を実車で検証してプログラムを完成させます。
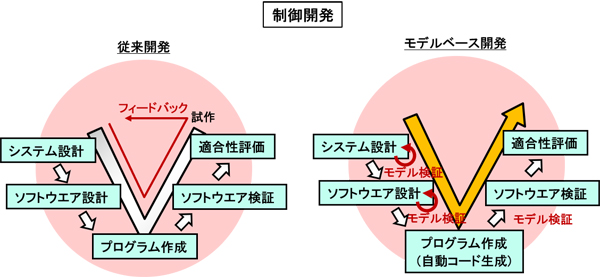
モデルベース開発のメリット
モデルベース開発のメリットは、以下の通りです。
・仕様モデルは物理現象を数式で表現するため、紙の仕様書に比べて情報が正確に伝わり、解釈の違いによる誤解が生じません。また、シミュレーションに使うことができるので、仕様検討の段階で、制御の流れの妥当性を確認できます。
・基本設計や詳細設計などのソフトウエア設計でも、シミュレーションによる検証を繰り返すことで、ソフトウエアの信頼性を高めることができます。
・ソフトウエア設計によって出来上がったモデルは、自動でコーディング(ソースコードに変換)してハードウエアに実装します。自動生成なので、実装担当者のスキルに依存せず、ミスも発生しづらくなります。
・ソフトウエアの検査に必要な環境をモデル化すれば、実機でなくても検査ができます。実機でないとソフトウエアの検査ができない従来方法に対して、早い時期に検査ができます。これにより、大幅な開発期間の短縮と開発コストの低減ができます。
多種多様なユーザーや市場の要望に応えるため、車の開発サイクルの短期化が求められています。そのような中で自動車メーカーは、制御開発の工数と時間が大幅に短縮できるモデルベース開発に積極的に取り組んでいます。
モデルベース開発の導入によって、開発工数が半減したという報告もあり、今後のさらなる改良と展開に期待するところ大です。
■試作車とは
車は市場に投入する前に、さまざまな機能や性能、耐久信頼性の確認のため試作車を製作して試験します。開発初期の試作車の目的は機能や性能、中盤は信頼性や耐久性、後半は車全体の品質の確認に重点が置かれます。
試作車の種類や役割について、解説していきます。
試作車の役割
試作車は、大別して研究開発用の試作車と量産確認用の試作車に分けられます。
それぞれの試作車は、さらに数段階の試作車に分けられ、研究開発用であれば新技術の機能確認用や車両性能用、燃費用など、機能ごとにそれぞれ試作車を製作します。
量産確認用であれば、量産仕様の図面、設備で製作する車両なので、目標性能の達成や車全体の品質の確認など、車の最終確認を行います。
試作車は量産車とは異なり、一台一台製作するのでコストは高く、特に開発初期の試作車は量産車の10倍程度のコストがかかる場合があります。したがって、メーカーはCAEを使ったデジタル開発やMBD(モデルベース開発)などを推進して、試作車台数を減らすことに注力しています。
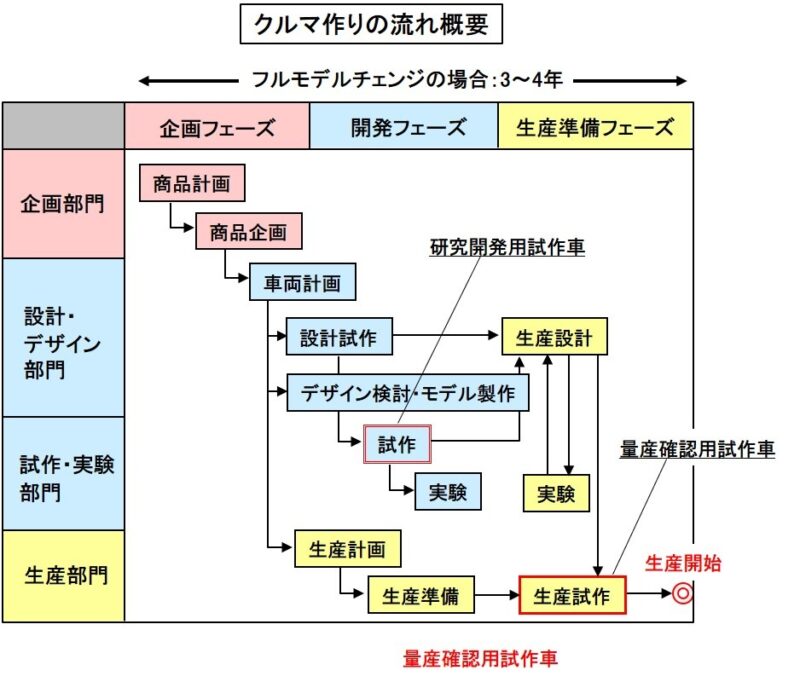
研究開発用の試作車
研究開発の段階では、走行性能用や燃費試験用、排ガス試験用、衝突試験用など、機能ごとに専用の試作車が製作されます。試験結果は、設計にフィードバックされて改良を繰り返します。
この段階では、新作のボディは出来上がっていないので、新型エンジンを開発する場合は同等レベルの旧型ボディに搭載して、走行性能や燃費性能などの改良を行います。
開発確認車によって開発目標の達成が確認できれば、次の量産確認フェーズに移行します。
量産確認用の試作車
量産確認段階では、量産仕様の図面と設備で製作した試作車によって、機能や性能、信頼性などを含めた品質目標のすべてが達成できているかを確認します。
走行性能やドライビングフィール、燃費、排ガス性能、安全性などを厳しい走行試験によって確認し、問題あれば設計にフィードバックして改良を繰り返します。
また、仕向け地特有の環境条件や走行条件を考慮して、現地での走行試験も行います。
試作車が公道を走行するためには
試作車による走行試験は、初期はテストコース中心に実施しますが、本格的な走行試験となると公道を使った実地走行が必要です。
公道を走行するためには、試作車が「保安基準」に適合していることを確認後、運輸支局に「車両改造」を申請して認可を受けます。
改造部品が保安基準に適合している、エンジンを換えた場合は排ガス規制へ適合しているなどが、試作車に求められます。
量産間近の試作車は、新型のボディも出来上がっているので公道では秘匿が必要です。走行するときには、カモフラージュのためにボディラインが分かりづらいようにマスキングしたり、場合によってはボディ表面に模様付けしたりします。
時々、「○○の次期車をスクープ!」といって、情報誌にカモフラージュした車が掲載されることがあります。メーカーが、宣伝目的であえてリークする場合もあるようですが…。
プロトタイプ車
試作車に近い「プロトタイプ車」という表現があり、原型や試作品といった意味で使われます。
試作車と同じ意味で使われる場合もありますが、あえて違いを表現すれば、プロトタイプ車とは量産車と同じボディ、スタイルの試作車、量産間近の試作車のことを指します。
新エンジンなど多くの新しい技術が採用された新型車の開発では、確認試験のために100台以上の試作車を製作することもあります。
最近は、開発費の削減や開発期間の短縮のため、CAEを使ったデジタル開発やMBD(モデルベース開発)などの活用によって、試作車台数は大幅に削減されています。
■デザイン開発とは
車の機能開発と同様、デザイン開発もCAD/CAMなど、さまざまな開発ツールの導入によって、デジタルモデルを主体とした開発へと進化しています。
開発期間の短縮と効率化が進むデザイン開発とデジタル化について、解説していきます。
車のデザイン開発
最近の車づくりは、できるだけ試験や試作車を減らして効率を向上させるため、CAE(Computer Aided Engineering:シミュレーション)やCAD(Computer Aided Design:コンピューター設計支援)/CAM(Computer Aided Manufacturing:コンピューター製造支援)によるデジタル開発を積極的に推進しています。
デザインの開発には、外観を決めるエクステリアデザインと内装全般のインテリアデザイン、ボディと内装の色を決めるカラーデザインがあります。これらは、車両側の機能・性能開発と並行して、デザイン部門と設計分門、試作部門が協力しながら進めます。
以下にデザイン開発の流れとデジタル化について、紹介します。
デザインコンセプトづくり
まず商品企画部門が、車の狙いや用途、ターゲット市場とターゲットユーザーなど、どのような車を開発するにかを大まかに定義します。
デザイン部門は、定義された車のコンセプトを具現化するために、どのようなエクステリア/インテリアの車にすべきかのイメージスケッチ、ラフスケッチを作成します。かつては手書き中心でしたが、最近はコンピューターグラフィックを使うケースが増えています。
レンダリング(完成予想図)
イメージスケッチの中から選ばれたデザイン案を、CADを使ってより具体的なデザインに絞り込み、レンダリングを作成します。デジタルモデラーが、前後横の全方向から見た車の外形をデジタルデータ化します。
この時点で、エンジンやトランスミッション、シート配列などのパッケージングも考慮した上で、カラーを含めて細部の凹凸まで詳細に表現します。
ドローイングとモデル化
レンダリングをもとに、そのデザインに設計要件を盛り込んだ図面に置き換えていきます。この図面をもとにデザインCADを使って3次元データ化が行われます。
この3Dデータをもとに1/5、実寸のクレイモデル(モックアップ)用のNC(工作機械制御)データを作成します。クレイモデルは、内側の金属フレームを発泡剤で覆って大枠のボディを形成して、その上に工業用の粘度を盛って製作します。インパネ形状などは、3Dプリンターを使って樹脂も組み合わせて製作します。
出来上がったクレイモデルは、レーザースキャニングなどで3次元計測してスタイリングCADにフィードバックし、修正を繰り返しながら最終クレイモデルが完成します。
CADが普及する以前は、デザイナーがイメージスケッチから線図を手書きし、それをもとにクレイモデルを製作し、レイアウトマシーンで計測してボディの外形線図を作成していました。
最終承認
デザインが確定すると、最終審査のためのハード(樹脂)モデルを製作します。ハードモデルは、艤装も樹脂やフィルムなどで仕上げ、見た目は実車と同一にして最終承認を受けます。
最終承認が得られた時点(量産開始時期の約1.0~1.5年前)で、すべての部品の3次元CADデータは、生産着工図面として生産関係の設計部門に渡されます。
最近は、3次元データをバーチャルリアティ(VR)空間で再現することによって、多くの関係者が同時にさまざまな角度からデザインをレビューできるようなりました。
CAD/CAMの普及で、デザインの3次元データの作成や、それをベースにしたクレイモデルの製作が効率良くできるようになりました。
さらに最近は、空間に車を再現するバーチャルリアティ(VR)を利用することによって、クレイモデルの製作回数を削減し、開発期間を短縮しています。
(Mr.ソラン)
クリッカー自動車用語辞典 https://clicccar.com/glossary/