目次
■車のトランスミッションとは
エンジンの発生するトルクと回転数を走行条件に応じて増減 (変速) して、適切な出力をタイヤに伝達するのがトランスミッション (変速機) です。歯車やプーリーを組み合わせた複雑な機構で構成されるトランスミッションの仕組みや特徴について、解説していきます。
トランスミッションの必要性
トランスミッションがないことを想定すれば、トランスミッションの必要性がわかると思います。例えば、1速だけだと発進はできますが、エンジン回転が上がりうるさいだけでスムーズな加速はできません。5速だけだと、そもそも発進ができません。
発進や登坂のような大きなトルクが必要な場合は、トルクを増大するために減速比が大きいローギヤが必要です。一方で、高速では燃費を良くするためにエンジン回転速度を下げる減速比の小さいハイギヤが必要です。
EVにトランスミッションは不要
EVは、トランスミッションがなくても基本的には問題なく走行できます。なぜでしょうか?
エンジン車のトルク特性は、トルクバンドが狭い山形の曲線を示します。一方モーターのトルクバンドは広く、回転数に対して反比例の関係になっているため、基本的にはトランスミッションが不要なのです。
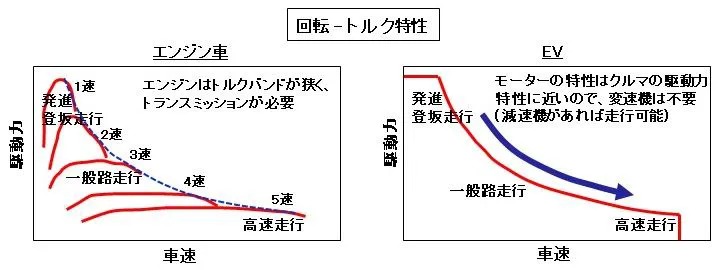
トランスミッションの種類
現在、自動車で使われている代表的なトランスミッションは、以下の5種類です。
1) MT(マニュアル・トランスミッション)
ドライバーがクラッチとシフトレバーを操作し、歯車の組み合わせを変更することによって変速します。クラッチは、変速時に一時的に駆動力を断続する役目を担います。
最大のメリットは、動力伝達効率が95%以上と高く、燃費性能に優れていることです。日本では、新車販売の2%にも満たないMT車ですが、構造がシンプルで低コストなため新興国で、またダイレクト感を好む欧州で普及しています。
2) ステップAT(オートマチック・トランスミッション)
遊星歯車機構の各歯車にある多板クラッチを油圧制御することによって、自動的に断続し、スムーズな変速を行います。
変速操作が不要で簡便ですが、内部構造が複雑なため、多段化すればさらに重量が増し、コストも高くなります。
3) CVT (連続可変トランスミッション)
1対のプーリーに金属ベルトを掛け、プーリーの半径を連続的に変化させて無段階で減速比を変更します。
比較的シンプルな構造で変速比が大きくとれるため、エンジンの燃費の良い運転領域が使いやすい利点があります。ただし、金属ベルトとプーリー間の摩擦によって駆動力を伝達するため、歯車よりも駆動損失が大きいことが課題です。
4) DCT(デュアルクラッチ・トランスミッション)
2系統の歯車機構と多板クラッチを備え、奇数段(1、3、5速)と偶数段(2、4、6速)それぞれのクラッチを交互に断続することによって、シームレスに変速します。
自動変速ですが、MTのようなダイレクト感のある変速フィーリングを体感できます。構造はMTなので、動力伝達効率が高いため燃費が良く、欧州車では徐々に増えています。
5) AMT (オートマチック・マニュアル・トランスミッション)
MTをベースに、クラッチ操作と変速をアクチュエーターによって自動化したトランスミッションです。
MT同様、構造がシンプルで軽量、動力伝達効率が高いことが最大の利点です。ドライバー自らが変速操作するMTに対して、アクチュエーターが変速するときの変速ショックに違和感があり、日本では欧州ほど評価されていません。
燃費規制や電動化に対応するため、トランスミッションの役割がますます重要になってきました。本章では、多種多様なトランスミッションについて、仕組みや特徴を個別に解説していきます。
■MT(マニュアル・トランスミッション)とは
MT車は、日本では新車販売の2%にも満たない少数派になってしまいました。しかし、世界的にみれば構造が簡単で低コストであるため新興国で、またそのダイレクト感を好む欧州では主流といっても過言ではありません。
技術的には成熟の域にあるMTの構造や機構について、解説していきます。
MTの特徴
MTの最大の特徴は、歯車で構成されるため動力伝達効率が95~98%程度あり、燃費が良いこと、軽量小型で低コストなことです。さらには、最近の日本市場ではあまりアピール性はありませんが、ダイレクト感のある走り「ファン・トゥ・ドライブ」ではないでしょうか。
一方、高齢者や不慣れな人にとって、変速操作が煩わしく、操作技量によって変速フィーリングが左右されるといった課題もあります。初期のMTに比べると、シンクロメッシュ機構の普及と改良によって、変速はかなりスムーズで容易になりました。
MTの構造
一般的なMTの構造は、各変速段の歯車が常時噛み合って空転しつつ、スリーブの移動によって歯車とアウトプットシャフトを選択段だけ結合する「常時噛み合い方式」です。
エンジンの回転は、クラッチ(別頁で解説)を介してインプットシャフトに伝わります。インプットシャフトは歯車を介してカウンターシャフトを回転させ、カウンターシャフトには各変速段に相当する複数の歯車が付いています。
変速レバーと連動したスリーブが移動することによって、選択した変速段の歯車とアウトプットシャフト(デフ、タイヤと連結)が結合されます。これによって、エンジンの回転が選択された変速比でアウトプットシャフトに伝わるのです。残りの歯車は、空転しています。
スリーブ(アウトプットシャフトとともに回転)と歯車を連結させるのが、シンクロメッシュ機構です。
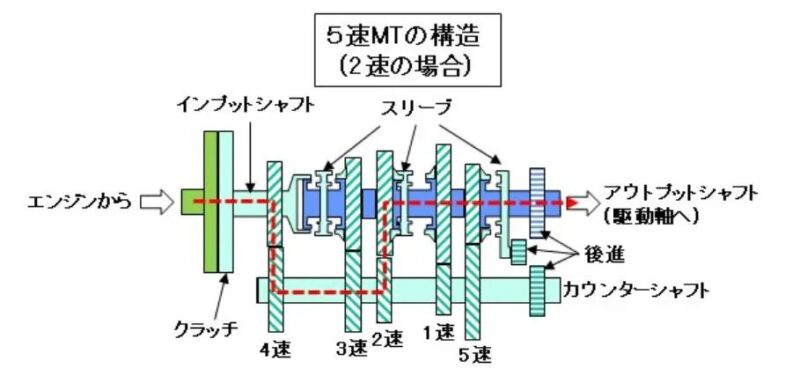
シンクロメッシュ機構
変速のときは、まずクラッチを切り、次の変速段を選択します。このとき選択された(空転)歯車とスリーブの回転には差があるために、そのまま連結しようとしても上手く歯がかみ合わず、大きな衝撃が発生し歯を傷めたりします。
シンクロメッシュ機構とは、スリーブを介してアウトプットシャフトと歯車の回転を同期させる機構です。
変速でクラッチを切ると、歯車が結合しているカウンターシャフトはフリーになるので、スリーブと歯車間の摩擦力によって、歯車の回転をアウトプットシャフトの回転に同期させるのです。
シンクロメッシュ機構をもう少し具体的に説明します。
歯車側に取り付けられた円錐状のシンクロナイザーとスリーブの間に、シンクロナイザーリングを設けます。スリーブを移動させると、シンクロナイザーリングに設けられた斜面とスリーブの斜面が接触し、その摩擦力によって回転差が吸収されます。徐々に同期して、最終的には選択段の歯車とスリーブが完全に結合します。
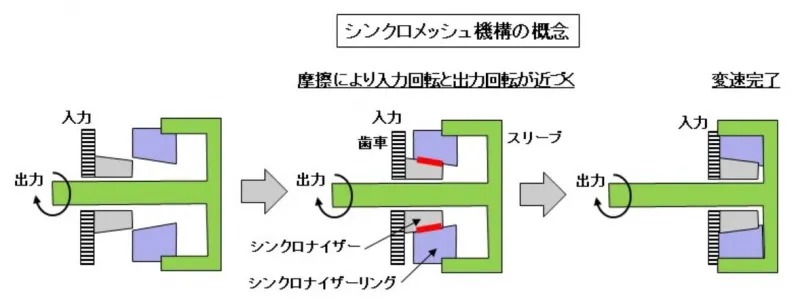
かつては、MTは圧倒的な燃費の良さで確たる存在感を示していました。一方で、ATやCVTなど自動トランスミッションの急速な改良によって、現在は燃費のアドバンテージが小さくなってしまいました。
新興国の需要とともにMTの数も当面は増加するでしょうが、本格的な電動化や自動運転の時代が到来すると、MTの将来は不透明になってしまいます。
■ステップAT(オートマチック・トランスミッション)とは
ステップAT車は、世界的にみてCVT、DCT、AMTを含めたAT全体の約6割を占め、主流となっています。特に渋滞が多い日本では、変速操作が不要であることが大きなメリットです。
要素技術の改良や多段化などによって、かつての燃費の悪さを払拭したステップATの構造や機構について、解説していきます。
ステップATの特徴
ATとは、ステップAT、CVT、DCT、AMTを含めた自動トランスミッション全般を指しますが、日本ではATというと通常はステップATのみを指すことが多いようです。
ステップATは、トルクコンバーター(トルコン)と自動変速機で構成されています。
トルコンは、動力をトランスミッションに伝達したり遮断したりする流体クラッチの役目とともに、駆動トルクを増幅する機能も兼ね備えています。自動変速機は、複数の遊星歯車機構を油圧制御によって切り替えて、スムーズな変速を実現します。
トルコンはドーナツのような形をして、内部はポンプとステーター、タービンで構成され、それぞれにプロペラがついています。これら3つのプロペラは直接つながってはいませんが、内部に満たされた作動油の回転力によって、動力をスムーズに伝達する仕組みになっています(トルコンの詳細については、別頁で解説)。
ステップATの構造
遊星歯車機構は、サンギヤと遊星ピニオンギヤ、遊星キャリヤ、リングギヤで構成されています。この中のサンギヤ、遊星キャリヤ、リングギヤの3要素のどれかを固定し、残りの2つを入力軸と出力軸に巧妙に切り替えることで変速を実現します。
ギヤの切り替えは、油圧制御によって各要素に配置された多板クラッチの断続で行います。
変速段数の増加は、前列の遊星歯車による変速後の駆動力を再度、後列の遊星歯車に入力することによって行います。通常、3~4速ATでは2組、5~6速ATでは3組、7~9速ATでは4組の遊星歯車を直列につなぎます。
最近のステップATは、燃費の向上をねらって多段化が進み、10段ATも登場しています。
遊星歯車機構の作動
増速、減速、後退(逆回転)の場合の遊星歯車機構の動きを、簡単に説明します。
・増速
サンギヤを固定し、入力軸を遊星キャリヤ、出力軸をリングギヤとします。遊星ピニオンギヤが自転しながらサンギヤの周りを公転し、出力軸のリングギヤは遊星キャリヤが自転する分だけ増速回転します。
・減速
サンギヤを固定し、入力軸をリングギヤ、出力軸を遊星キャリヤとします。遊星ピニオンギヤが自転しながらサンギヤの周りを公転し、出力軸の遊星キャリヤは、遊星ピニオンギヤの分だけ減速回転します。
・後退(逆回転)
遊星キャリヤを固定し、入力軸をサンギヤ、出力軸を遊星キャリヤとします。遊星ピニオンギヤは自転のみなので、出力軸の遊星キャリヤはサンギヤに対して、減速しつつ逆回転します。
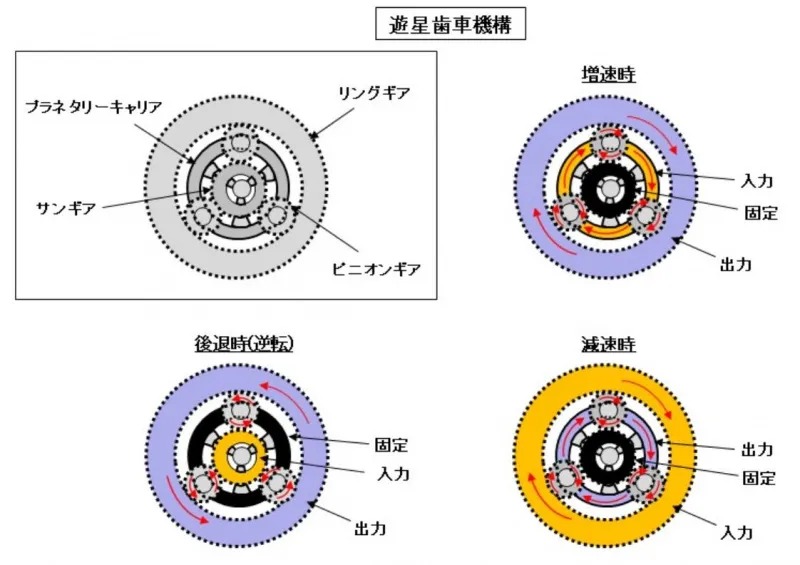
最近のステップATは、高度な制御によって変速はスムーズになり、かつて悪かった燃費についても運転条件にもよりますが、MTに負けないレベルまで改善されてきました。
課題は、多段化によってさらに大きく重くなること、また機構が複雑で精密なためコストが高いことです。
■トルクコンバーター(トルコン)とは
トルクコンバーター(トルコン)は、エンジンの出力をトランスミッションに伝達、遮断する流体クラッチで、エンジントルクを増幅する機能も兼ね備えています。
エンジンとステップATおよびCVTの間に配置され、重要なつなぎ役を担っているトルコンの構造や機構について、解説していきます。
トルコン
トルコンは、エンジンとステップATおよびCVTの間に配置され、2つの重要な役割が果たしています。
1つ目は、エンジンの出力をトランスミッションに伝達したり遮断したりするクラッチの役目。2つ目は、入出力に回転差がある場合にエンジントルクを増幅する機能です。
トルコンはドーナツのような形をして、内部はポンプとステーター、タービンで構成され、それぞれにプロペラがついています。これら3つのプロペラは直接つながってはいませんが、内部に満たされた作動油の回転力によって、駆動力をスムーズに伝達する仕組みになっています。
トルコンの構造
エンジンの駆動力によってポンプのプロペラが回転し始めると、中の作動油も同時に回転を始めます。作動油は遠心力によって、ポンプの外側へ流れ始め、タービン側のプロペラにあたり、タービンも回転し始めます。タービンは、トラスミッションとつながっているため、タイヤの駆動力となって車を動かします。
ポンプとタービンの間にあるステーターは、タービンから流れ込む作動油を再度ポンプ側に戻して、ポンプの回転力をアシストします。エンジントルクにこのアシスト力が加わることで、エンジントルクが増幅できるのです。入出力の速度比が小さいほど、トルクの増幅効果は大きく2~3倍になります。
エンジンの回転が上がると作動油の遠心力が強まり、ポンプ回転とタービン回転が同等になります。タービンへ駆動力を無駄なく伝えることができるので、トルコンによるトルク増幅効果と相まって、スムーズで力強い発進・加速ができます。

ロックアップ機構
作動油による駆動力の伝達は、通常の摩擦クラッチに比べて効率が悪いので、燃費悪化の要因になります。
ロックアップは、油圧制御によってロックアップ用クラッチを接続し、エンジンとトランスミッションを直結する手法です。直結すると振動は発生しやくなりますが、動力伝達効率が上がり、燃費は向上します。
トルコンの作動原理
トルコンの作動原理は、対向する2台の扇風機を使って説明できます。
一方の扇風機を回し、もう一方はスイッチを切っておきます。扇風機が”弱”程度の回転では、対向する扇風機は回りませんが、回転力を強めると対向する扇風機は回り始めます。
回転する扇風機がポンプ、スイッチOFFの扇風機がタービン、作動油が空気というわけです。やってみてください、確かにスイッチOFFでも扇風機は回り始めます。
スムーズな発進や走行を生かしつつ、燃費を良くするために変速後はすぐにロックアップして直結で走行する方向で、ステップATとトルコンの改良は進んでいます。
ステップATは、さらなる燃費向上をねらって、スムーズな変速とダイレクト感のある走りの両立を目指しています。
■CVT(連続可変トランスミッション)とは
CVT(連続可変トランスミッション)は、日本のノロノロ運転や渋滞時のストップ・アンド・ゴーに最適なトランスミッションであり、小・中型車を中心に普及率を伸ばしています。
エンジンとの統合制御で低燃費を発揮するCVTの機構やメリット・デメリットについて、解説していきます。
CVTの仕組み
一般的なCVTは、一対の入出力プーリーに金属ベルトを掛けて、駆動力を伝達します。入出力プーリーの有効径(ベルトの巻きかけ半径)を変えて、変速比を連続的に変化させます。
金属ベルト(プッシュベルト式)は、数百枚の金属コマを重ね、両側から薄い鋼板の輪を重ねたもので挟んで構成されています。
プーリーの断面は、V字構造になっており、油圧制御でベルトのかかる面がV字の斜面を昇降します。この結果、プーリーの有効径、すなわち変速比が連続的に変化します。
プーリーは、入力側(ドライブ側)のプーリー幅を変化させると、ベルトに引っ張られて出力側(ドリブン側)のプーリー幅も変化し、幅広い変速比が実現できます。
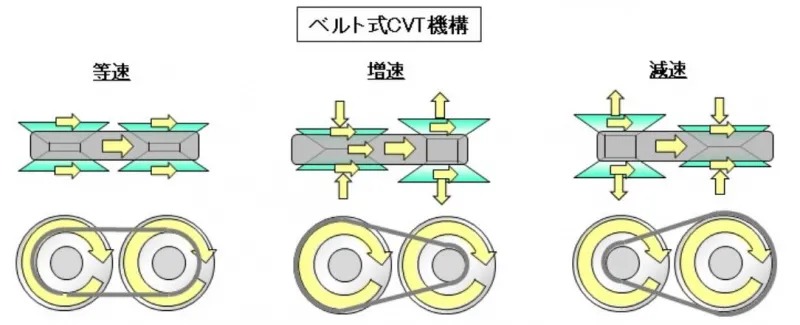
CVTのメリット
一般的には、CVTもステップAT同様、前段にトルコンを配置します。トルコン効果と相まって、発進はスムーズで、駆動力が途切れないため変速ショックがなく、加減速がスムーズです。
エンジンには、「燃費の目玉」と呼ばれる熱効率の良い領域が存在します。「燃費の目玉」付近を通るように、変速比を任意に選択できるため、燃費が向上します。小型車や日本のように市街地中心の走行に向いています。
また、歯車を使った他のトランスミッションと比べて、部品点数が少なく、シンプルな構造で軽量小型です。
CVTのデメリット
初期のCVTでは、多くのドライバーが加速時に先にエンジン回転が上がってから加速する「ラバーバンドフィール(ゴムバンドのようにレスポンスが悪い)」に、違和感やレスポンスが悪いと感じていました。歯車でなく、プーリーとベルトで変速するCVT固有の現象ですが、ハードとソフト(制御)の両面からの改良によって、2015年以降は問題ないレベルまで改善されています。
プーリーとベルトの摩擦力で動力を伝えるため、高い油圧で押し付ける油圧ポンプの駆動損失、さらにプーリーとベルトの接触面を滑りながら変速するので、伝達損失が発生します。定常状態で10%程度、変速時には40%程度の損失が発生します。
ステップATより、コストは高くなります。プーリーの高精度加工や、特殊な金属ベルトなどがコストアップの要因です。
CVTの矛盾する要件
そもそも、CVTには、駆動力を伝えるときには滑らせない(摩擦力が大)、一方、変速時にはベルトを滑らせる、という矛盾があります。
高出力エンジンでは、動力を伝達するための強い摩擦力、高い油圧が必要となることから、駆動損失が増大します。したがって、CVTの高出力・大排気量エンジンへの適用は厳しいのです。
変速比を連続的にある程度自由に設定できる(より燃費の良い領域を使用できる)という点で、CVTは理想的なトランスミッションと言えるかもしれません。
日本では、小・中型車はCVT、大型車はステップATという棲み分けができていますが、弱点である動力伝達効率がさらに改良できれば、大型車にもCVTが食い込んでくるかもしれません。
■DCT(デュアルクラッチ・トランスミッション)とは
伝達効率の良いMTと、自動で効率的な変速ができるATの両機能を持ち合わせているのが、DCT(デュアルクラッチ・トランスミッション)です。日本での採用は限られますが、欧州では高い人気を持つDCTの機構や特徴について、解説していきます。
DCTの構造
DCTは、MTベースなので動力伝達効率が高く、ATのように変速制御を自動化して操作を不要としたトランスミッションです。
奇数段(例えば、1-3-5速)と偶数段(2-4-6速)に分割された2系統の歯車機構の入力軸と、入力軸を切り替えるための2系統の多板クラッチで構成されています。2本の入力軸は、多板クラッチON-OFFにかかわらず歯車を介して、1本の出力軸に統合して出力するようになっています。
2系統の切り替え用クラッチは、湿式の多板クラッチです。
湿式クラッチはオイルに浸っており、断続がスムーズで、摩擦熱をオイルで冷却できるため耐久性に優れ、DCTでは主流となっています。
各段の歯車制御は、ソレノイドバルブによってシフトフォークを動かすことで歯車を切り替えます。前段の多板クラッチと連動して、俊敏な変速を実現しています。
変速の仕組み
発進時の変速の仕方について、簡単に説明します。
まず奇数段クラッチをつないで1速で発進します。このとき、クラッチのつながっていない偶数段の2速の歯車は、かみ合わせを完了して待機状態です。
車速が上がった時点で、奇数段クラッチが切れると同時に偶数段クラッチがつながり、瞬時に2速へ変速します。このとき、クラッチがつながっていない奇数段は3速の待機状態です。
このように、奇数段と偶数段をシームレスに駆動力が途切れることなく、変速できます。
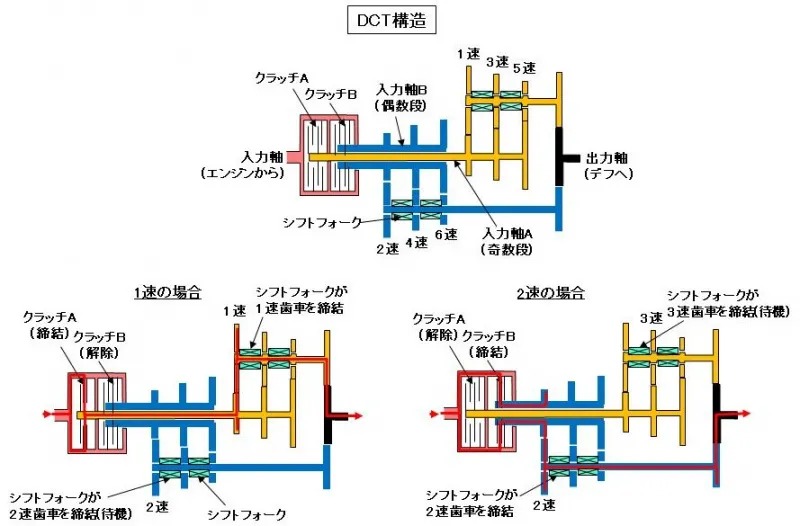
DCTのメリット・デメリット
DCTは、MTベースの歯車機構なので伝達効率は優れていますが、自動変速のための油圧系の損失があり、総合的にはMTの95~98%に対して90%前後まで下がります。
ただし、DCTは駆動力が途切れることなく瞬時(コンマ数秒程度)に変速できるため、運転者の変速技術に左右されるMTよりも、場合によっては燃費が良い場合もあります。
俊敏な変速は、中高速運転ではダイレクト感のある走りを実現しますが、一方、発進や極低速走行ではトルコンがないので、クラッチ断続時に多少のショックが発生する場合があります。
複雑な機構なので、コストは他のトランスミッションに比べ高くなります。
日本での採用は限定的
日本では、DCTの採用はホンダのHEV「i-DCD」と一部のスポーツ車に限られます。
欧州では、ダイレクト感と燃費の両立ができるDCTは人気がありますが、日本ではショックのないスムーズな加速と燃費を両立するトルコン付きCVTやステップATが普及しています。渋滞が多くストップ・アンド・ゴーの頻度が高い日本では、ダンパー的な役割のトルコンが必須かもしれません。
欧州や中国で人気のDCTですが、今後日本で普及するかというと、答えは「NO」だと思います。ベースであるMTの新車販売比率がすでに2%を切っている日本市場では、MTの改良線上に位置するDCTが、今後普及する可能性は小さいと思われます。
高速走行の定常や加減速運転が中心の欧州に対して、渋滞などのノロノロ運転の低速走行が多い日本の交通事情では、ちょっとしたギクシャク感でも致命的になってしまいます。
■AMT(自動MT)とは
AMT(自動MT)は、MTの構造そのままで変速操作とクラッチ操作を自動化したトランスミッションです。日本での採用例は少ないですが、欧州では廉価なトランスミッションとして小型車を中心に採用されています。日本でなぜ採用されないのかを含めて、AMTの機構や特徴について解説していきます。
AMT
AMTは、MTの燃費性能とATの利便性を狙い、MTの構造そのままで変速操作とクラッチ操作を自動化したトランスミッションです。広義のAMTには、デュアルクラッチ・トランスミッション(DCT)も含まれ、区別するためにシングルクラッチ式ATと呼ばれることがあります。
また、変速操作は運転者に任せて、クラッチ操作のみ自動化したタイプ(セミAT)もあります。
クラッチ操作および変速操作は、一般には電動油圧式アクチュエーター、または油圧を使わないモーターアクチュエーターで行います。油圧式は応答性に優れ、モーター式は小型、低コストです。
AMTのメリット
基本はMTなので、ダイレクト感のある走りとともに、動力伝達効率が高いため燃費が優れています。クラッチと変速操作部が自動化されていますが、構造は比較的シンプルで軽量、低コストです。
また、大半の部品がMTと共通化できるため、開発・製造コストを抑えられます。MT比率が高い欧州では、その効果がより大きくなります。
AMTのデメリット
最大の問題は、変速フィーリングが悪いことです。これが、日本市場で受け入れられない最大の理由です。
MTでは、クラッチを切って変速して次にクラッチをつなぐまでの間に、エンジンの駆動力がコンマ数秒間、途切れる時間があります。加速中に一瞬推進力がなくなる「トルク抜け」が起こるので、ドライバーは減速感を感じます。
MT車の場合は、自分で変速するので身構えることができるので慣れますが、AMTの場合は予期せぬタイミングで変速が起きるので、それをギクシャク感、ショックとして感じてしまいます。
欧州では渋滞が少なく、比較的高速の定常走行が多いのであまり気になりません。むしろ、運転の小気味よさを感じ、燃費メリットを享受しやすくなります。
一方、日本では渋滞が多く、ストップアンドゴーや低速走行が中心なため、変速時のギクシャク感が目立ち、ユーザーには許容できないのです。
日本でのAMT採用例
欧州では多くの廉価車に採用されていますが、現在日本でAMTを搭載しているのは、スズキの「エスクード」、「ソリオ」、「エブリイ」に限られます。スズキは、「AGS(Auto Gear Shift)」という名称で、MTをベースに油圧アクチュエーターとの接続部分とパーキング機構部分を変更して、AMT化しています。
クリープ機能(トルコン付きミッションのように、アクセルを踏んでいなくても、わずかな推進力を持たせた機能でスムーズな発進をサポート)や、ヒルホールドコントロール(坂道でブレーキ油圧を数秒間保持して後退を回避)を採用して、AMTの発進にかかわる弱点を解消させています。
MT車の感覚を基準にしている欧州ではAMTが許容されても、CVTやステップATの自動トランスミッションに慣れている日本では、今後も許容されにくいのではないでしょうか。
■クラッチとは
クラッチは、エンジンの動力をMT(マニュアル・トランスミッション)に伝達したり、切り離したりする役目を担う「動力伝達装置」です。発進、変速、停止時にエンジンの動力を伝達、遮断するクラッチ機構の仕組みや作動原理について、解説していきます。
クラッチの機能
クラッチは、エンジンの動力をトランスミッションに伝達したり、切り離したりする装置です。クラッチペダルを踏み込むと、エンジンの動力が遮断され、クラッチペダルから足を離すと動力が伝達されます。
ただし、クラッチは単純なON-OFF制御だけではありません。MT車に乗るドライバーには、クラッチをつなぐときに「半クラッチ」というクラッチの踏む込み量の調整でクラッチをスリップさせながら接続するテクニックが必要です。
発進時は回転しているエンジンと停止しているトランスミッションを、変速時にはエンジンと異なる回転のトランスミッションをショックなくスムーズにつなぐために、半クラッチ操作が必要です。
クラッチの構成
クラッチ機構は、フライホイールとクラッチディスク、プレッシャープレート、クラッチカバーで構成されています。
フライホイールは、エンジンのクランク軸と直接繋がっており、エンジンのトルク変動を抑える働きがあります(別頁で詳細を解説)。
クラッチディスクは、フライホイールに取り付けられたクラッチカバーに収められており、メインドライブシャフトを介してトランスミッションと連結しています。摩擦によって圧着するので、クラッチディスクの接触面には摩擦材をドーナツ状に貼り付けています。
クラッチディスクを押し付けるのは、クラッチペダルと連動するプレッシャープレートと呼ばれる円盤です。プレッシャープレートは、ダイヤフラムスプリングで構成され、通常はスプリング力でクラッチディスクを押し付けています。クラッチペダルを踏み込むと、スプリング中央部が押されてスプリングの押し付け力がなくなり、フライホイールとの間に隙間が発生し、エンジンの動力が遮断されます。
クラッチの作動原理
クラッチディスクは、メインドライブシャフトにスプラインで常時噛み合っているので、トランスミッションと連れ回ります。
走行中は、フライホイールとクラッチディスクがプレッシャープレートによって押し付けられ、エンジンの動力がトランスミッションに伝達されています。クラッチペダルを踏み込むと、プレッシャープレートを動かし、フライホイールからクラッチディスクを引き離し、動力の伝達を遮断します。
半クラッチは、フライホイールとクラッチディスクが、スリップしながら回っている状態です。
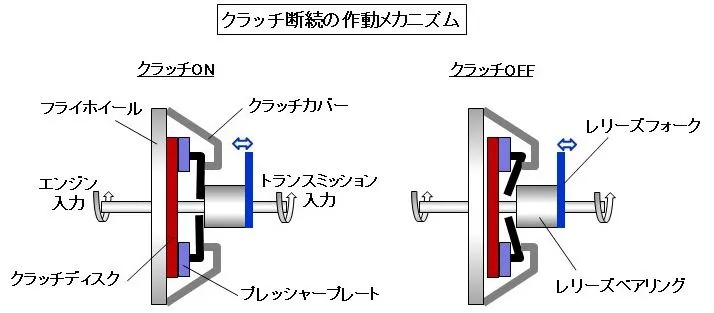
クラッチの寿命
クラッチは、摩擦力を利用して断続を繰り返すので、走行距離ととともにクラッチが滑りやすくなります。通常クラッチの寿命は、乗り方によって違いますが、走行距離で5~8万kmぐらいです。
ただし、坂道で半クラッチ状態を長く継続すると、摩擦熱によってクラッチがツルツル状態になり、即交換が必要となります。
日本では、新車の95%以上がAT車なので、多くの人がMT特有のクラッチ操作や半クラッチ操作を経験することはありません。AT車では、クラッチのような役目をするトルコンという便利な流体クラッチがあるので、普段は動力の断続を意識する機会はほとんどないと思います。
■変速比と減速比とは
トランスミッションの変速比や車の減速比、総減速比は、車が目標とする動力性能や燃費性能を実現するように設定されています。変速比と減速比、総減速比の設定の考え方について、解説していきます。
変速の必要性
EVは、モーターのトルクバンドが広いため、基本的にはトランスミッションがなくても、実用上問題ありません。一方エンジン車は、トルクバンドが狭いためトランスミッションが必要です。
発進や登坂のような大きなトルクが必要な場合は、ローギヤを使います。トランスミッションによって減速されても、入力されるエンジン出力(トルク×回転数)は変わらないので、減速されるとその分トルクが増大します。一方、高速ではハイギヤを使います。変速によって相対的にエンジン回転数を低下させて燃費を向上させます。
また、高速走行中に追い越し加速するときは、MT車ではシフトダウン、AT車ではキックダウンして変速段を下げて加速力を強化して対応します。
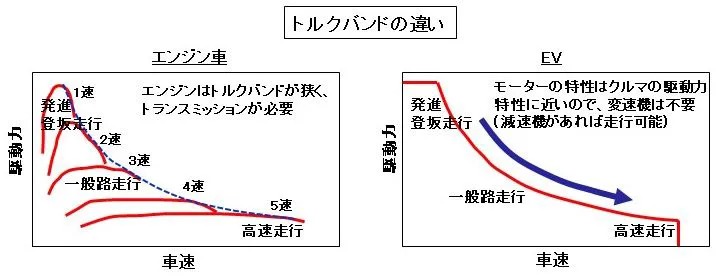
変速比と減速比、総減速比
変速比(ミッションギア比)とは、各ギア段のエンジン回転数とトランスミッション出力回転数の比です。トランスミッションでエンジン回転数がどれだけ減速されるかを示します。
例えば、あるギア段の変速比が2ということは、エンジン回転数が2,400rpm(回転数/分)のとき、トランスミッションで1/2に減速されてトランスミッション出力回転数は1,200rpmです。
さらに、タイヤに至るまでにデファレンシャルギアによる減速があります、これを減速比(デフ比)や最終減速比(ファイナルギア比)と呼びます。
例えば減速比が3ということは、上記設定でデフによって1/3に減速されるため、タイヤの回転数は400rpmです。
以上、トランスミッション変速比2、デフ比3の設定では、エンジン回転数2,400rpm→トランスミッション1,200rpm→タイヤ回転数400rpmとなります。
トランスミッション変速比と減速比の積を総減速比と呼び、これはエンジン回転数とタイヤ回転数の比を表します。
カタログには、これら各段の変速比と減速比、総減速比が表記されています。あるエンジン回転数でのタイヤ回転数、すなわち車速(πxタイヤ直径×タイヤ回転数)が算出できます。
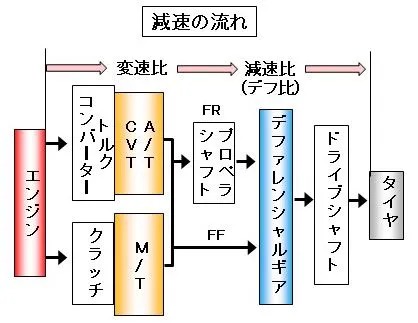
変速比の設定
一般に最低速段の変速比は、必要な発進加速や登坂能力で決まり、最高段数は走行抵抗に打ち勝ち必要な最高車速が得られる変速比に設定されます。それらの中間の変速比は、それぞれの中間段の走行性能と燃費性能をバランスさせて設定されます。
最近は特に燃費が重視され、ステップATでは多段化が進み、7速や8速のトランスミッションも珍しくはありません。変速段数が増えれば、発進加速を犠牲にすることなく、定速走行のエンジン回転数を低く抑えることができ、燃費を向上させることができます。また変速ショックが小さくなり、スムーズな走行と静粛性が得られます。
長年車に乗っている人は、最近の車は同じ車速でもエンジン回転数が低いと感じることが多いのではないでしょうか。
これは、総減速比を低く設定して、エンジン回転数を下げ負荷を上げて、「燃費の目玉」に近づけて、燃費を良くするのが狙いです。
燃費重視の車は、トルク不足や加速不足を指摘されることが多いですが、これはエンジンの出力不足というより、走りを犠牲にして総減速比が低い設定になっていることが要因のようです。
走りと燃費を両立するには、やはり減速比調整に頼るのではなく、エンジン本体の燃費を改良するしかありません。
(Mr.ソラン)
クリッカー自動車用語辞典 https://clicccar.com/glossary/