目次
■車の燃料噴射系システムとは
燃料は、燃料タンクからエンジンの噴射システムに圧送され、さまざまな噴射方式によってシリンダーの中に供給されます。
ガソリンエンジンおよびディーゼルエンジンの燃費や排出ガス性能を決定する燃料噴射システムについて、解説していきます。
燃料噴射システムの歴史
ガソリンエンジンの噴射システムは、排気ガス規制の強化や低燃費化ニーズに応えるため、従来の機械式のキャブレター方式から、1980年代から1990年代にかけて、吸気ポートに燃料を噴射する電子制御のポート噴射方式に置き換わりました。
ディーゼルエンジンの噴射システムは、かつては高圧の分配型噴射ポンプと燃料圧力によって弁開閉を行う自動弁を組み合わせた高圧噴射システムでした。2000年に入り、噴射自由度の高い電子制御のコモンレール噴射システムに置き換わりました。
キャブレター
キャブレターは、吸気管の負圧を利用して燃料を吸い出し、霧状にして空気と混合させながらシリンダーの中に供給するシステムです。エンジンの回転と負荷に応じて、燃料の吸い出し量が変化するように内部の燃料通路構造を構成しています。
ポート噴射システム(ガソリンエンジン)
電子制御のポート噴射では、噴射弁が各気筒の吸気ポートに装着されているため、燃料は正確かつ均等に分配されます。
ポート噴射の出現によって、シリンダー内の空燃比(吸入空気重量/供給燃料重量)を適切に制御でき、三元触媒と組み合わせて排出ガス性能が飛躍的に改善されました。
筒内噴射システム(ガソリンエンジン)
筒内噴射エンジンは、ディーゼルエンジンのようにシリンダー内に直接燃料を噴射するエンジンです。1990年後半に出現した筒内噴射エンジンは、リーンバーンを実現した画期的なエンジンでした。しかし、耐久性や排出ガス規制対応に課題があり、その後すぐに市場から撤退しました。
筒内噴射のメリットが再評価され、多くのメーカーがダウンサイジングターボと組み合わせて採用し始めました。現在の筒内噴射エンジンの多くは、リーンバーンを採用していませんが、充填効率が上がる、ノッキングが発生しにくいというメリットを生かして高出力と低燃費を実現しています。
リーンバーン
リーンバーンとは、空燃比が14.7(理論空燃比)より大きい(例えば30~40)、燃料に対して吸入空気が多い希薄燃焼のことです。三元触媒が使えず排出ガス低減が課題ですが、低燃費技術の目玉として現在も多くのメーカーが取り組んでいます。最近では、2020年に実用化したマツダの“SKYACTIV-X”を採用した「CX-30」や「マツダ3」、スバルの新型「レヴォーグ」は、手法は異なりますが、リーンバーンを採用しています。電動化技術が加速する中で、エンジンの燃焼技術は目立ちませんが、熱効率を上げる有効な手段であることに間違いありません。
コモンレール噴射(ディーゼルエンジン)
熱効率の高いディーゼルエンジンは、燃費は良いが、一方で燃焼音と排出ガスに課題がありました。1990年代末のコモンレール噴射システムの出現によって、課題は大きく改善され、欧州では乗用車でも50%近いシェアを獲得しました。
ディーゼルエンジンでは、微粒化と分散性に優れた燃料噴霧が必要なため、最大200MPa程度の超高圧で噴射されます。また、排出ガスと燃焼騒音を抑制するため、1回の燃焼行程中に噴射を複数回に分ける多段噴射を実現するために、高圧でありながら高応答の噴射弁が採用されています。
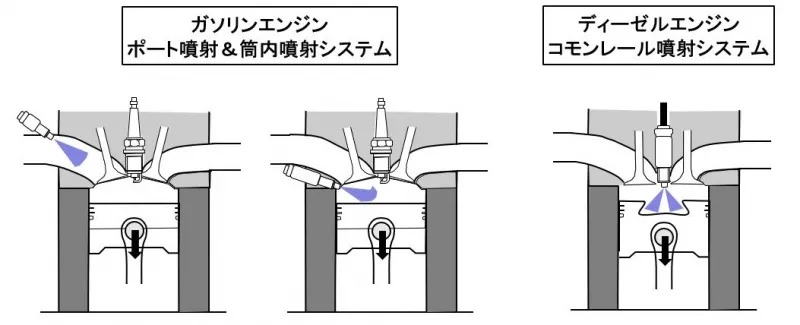
燃料噴射システムは、エンジンの直接的なエネルギー供給源であるため、燃費や出力、排出ガス性能すべてに大きな影響を与えます。
本章では、進化し続ける燃料噴射系システムについて、詳細に解説します。
■ポート噴射システムとは
ガソリンエンジンの標準的な噴射システムは、各気筒の吸気ポートに噴射弁を装着したポート噴射システムです。排ガス規制が強化され始めた1980年頃から普及し始め、現在、大半のガソリンエンジンが採用しています。
ガソリンエンジンの標準的なポート噴射システムについて、解説していきます。
ガソリン燃料噴射システムの歴史
ガソリンエンジンの噴射システムは、排気ガス規制の強化や低燃費ニーズに応えるため、従来の機械式のキャブレター(気化器)方式から、1980年代~1990年代にかけて吸気ポートに燃料を噴射する電子制御のポート噴射(PI)システムに置き換わりました。
過渡時には、キャブレターの位置に1本(または2本)の噴射弁を装着したSPI(シングルポイントインジェクション)システムもありましたが、中途半端な位置づけとなり短命に終わりました。ポート噴射を、SPIという表現に対比してMPI(マルチポイントインジェクション)と呼ぶ場合もあります。
ポート噴射システムの構成
燃料(ガソリン)は、燃料タンク内蔵の燃料ポンプによって吸い出されます。次に、燃料フィルターで異物が除去され、燃料デリバリーパイプに圧送されます。デリバリーパイプには、プレッシャーレギュレターが付いており、既定の噴射圧(0.3~0.4MPa)になるように圧力を調整します。
燃料は、デリバリーパイプから各気筒の吸気ポートに装着した噴射弁に供給され、シリンダー内に正確かつ均等に分配されます。噴射される燃料量や噴射時期などは、ECU(エンジンコントロールユニット)によって運転条件に応じて適切に制御されます。
シリンダー内の空燃比(吸入空気重量/供給燃料重量)を精度高く制御できるため、三元触媒と組み合わせて、排出ガス性能が飛躍的に改善されました。
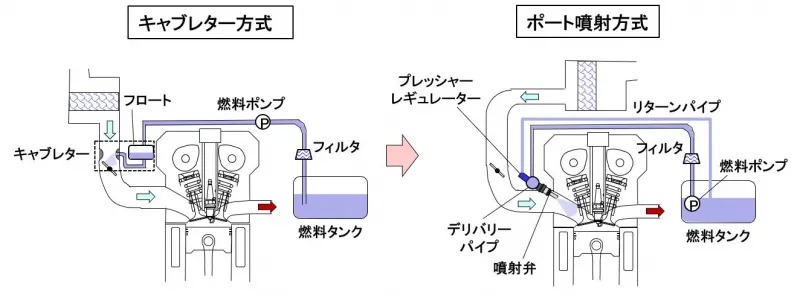
三元触媒と空燃比
三元触媒は、エンジンの空燃比を理論空燃比14.7近傍に設定することによって、CO、HC、NOxを同時に浄化できます。空燃比を理論空燃比近傍に精度良く設定するため、排気管に装着した酸素センサー(O2センサー)信号を使ってフィードバック制御します。
噴射弁
燃料噴射弁から噴射される燃料の噴霧特性や分散特性は、シリンダー内の混合気形成や燃焼特性に大きな影響を与えます。
噴射弁は、ニードル弁、プランジャー、ソレノイドコイルなどで構成される電磁弁です。
ソレノイドコイルに所定の時間の電流が流れると、プランジャーコアが磁力によって吸引され、コアと一体になっているニードルが引き上げられて、噴射弁が開きます。この間、プレートノズル部で微粒化された燃料噴霧が噴出します。
ソレノイドコイルの電流が切れると、ニードルはスプリングの押し付け力により全閉となります。燃料噴霧には、優れた微粒化特性が要求されるので、噴射弁先端ノズル部の形状の最適化が重要です。
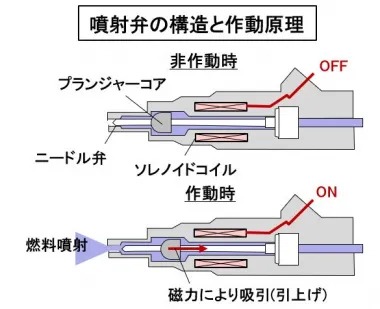
燃料噴射システムが、キャブレター方式からポート噴射システムへ変わった時点で、ガソリンエンジンは大きな進化を遂げました。
2010年以降に高級車用や燃費を訴求するようなエンジンで、筒内噴射システムを採用する例が増えていますが、今現在はまだコストパーフォーマンスで有利なポート噴射が主流です。ただし、今後も筒内噴射システムは増えることが予想され、2025年以降は廉価エンジンがポート噴射、高性能や低燃費エンジンには筒内噴射というように、噴射システムの二極化が進むと思われます。
■筒内噴射システムとは
1990年代末に出現した筒内噴射エンジンは、短期間ですぐに市場から消えましたが、また注目され始めています。「ダウンサイジング直噴ターボ」というコンセプトに組み込まれ、筒内噴射エンジンのノックしづらさや制御性に優れているという特徴が発揮されています。
再び注目されている筒内噴射システムについて、解説していきます。
筒内噴射システムの歴史
筒内噴射エンジンは、ディーゼルエンジンのようにシリンダー内に直接燃料を噴射するエンジンです。1996年に三菱自動車が発売した「GDI(Gasoline Direct Injection)エンジン」は、リーンバーンを実現した画期的なエンジンでした。トヨタと日産も追従しましたが、耐久性に課題があり、当時の次期排出ガス規制に対応が困難なことから、短期間ですぐに市場から消えました。
噴射システムの進化とともに筒内噴射のメリットが再評価されています。現在の筒内噴射エンジンの多くは、リーンバーンは採用していませんが、ダウンサイジングターボシステムと組み合わせています。ダウンサイジング直噴ターボは、ダウンサイジング直噴ターボは、2010年以降欧州を中心に普及し、国内メーカーも採用し始めました。
リーンバーン
リーンバーンとは、空燃比が14.7(理論空燃比)より大きい(例えば30~40)、燃料に対して吸入空気が多い希薄燃焼のことです。三元触媒が使えず排出ガス低減が課題ですが、低燃費技術の目玉として多くのメーカーが取り組んでいます。
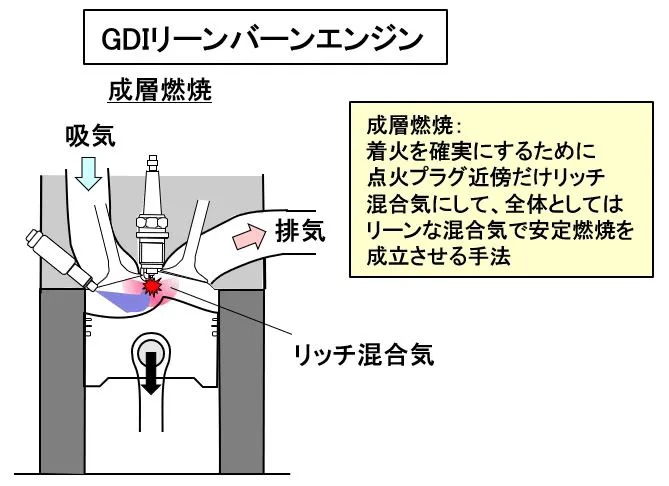
筒内噴射システムのメリット
筒内噴射システムは、ポート噴射システムに対して以下のメリットがあります。
・燃料を直接シリンダー内に噴射するため、より高度に応答性良く、エンジンが制御できる。
・シリンダー内に噴射された燃料は、周囲から熱を奪って気化。この気化熱によってシリンダー内の圧縮温度が低下し、密度が上がるために吸入空気が増え、出力が向上する。
・シリンダー内の温度が下がると、ノッキングしづらくなる。ノッキングが抑えられれば、圧縮比を上げることができ、出力向上や燃費向上につながる。
筒内噴射は、圧縮行程後半の圧力が高いシリンダー内に噴射するため、噴射圧力はポート噴射の0.3~0.4MPaに対して、最大50MPa程度まで高めています。そのため、噴射系全体のコストは高くなります。
筒内噴射システムの構成
燃料(ガソリン)は、燃料タンク内蔵の低圧フィードポンプで吸い上げられて、高圧燃料ポンプに圧送されます。エンジンのカム駆動の高圧ポンプで昇圧された燃料は、燃料デリバリーパイプに圧送されてプレッシャーレギュレターによって既定の圧力に調整されてから、各シリンダーへ噴射されます。
筒内噴射用の噴射弁は、基本的にはポート噴射弁と同様、電磁駆動タイプです。噴射圧が高いので、噴射弁の駆動電圧を上げて電磁力を強化しています。また、噴霧の微粒化や分散性を改善するため、複数の噴孔を設ける、あるいは噴射弁の先端シート部にスワール流を発生させるような工夫をしているものがあります。
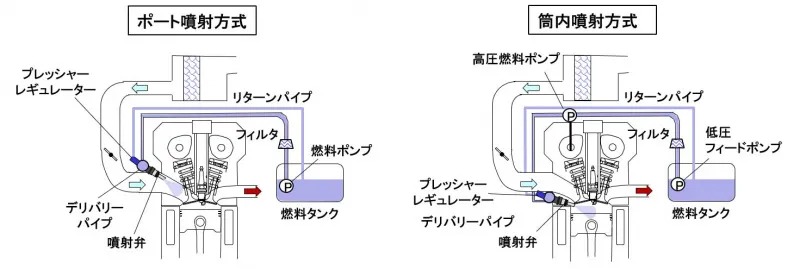
欧州に追従して日本でも2010年以降筒内噴射エンジンが増えてきました。
これらのエンジンは、ダウンサイジング直噴ターボという新しい低燃費コンセプトで、筒内噴射システムの特徴を生かしています。ただし筒内噴射エンジンは、噴射弁や高圧ポンプがまだ高価なため、標準エンジンとしてポート噴射エンジンに取って代わるには、もう少し時間がかかりそうです。
■ 筒内噴射リーンバーンとは
1996年、三菱自動車がGDI(筒内噴射)エンジンを市場投入しました。燃費に優れたリーンバーンを採用した当時としては、画期的な直噴エンジンでした。すぐにトヨタと日産も追従しましたが、いずれも10年足らずで市場から撤退しました。
注目された筒内噴射リーンバーンエンジンがなぜ市場から消えたのか、解説していきます。
リーンバーンのメリット
通常ガソリンエンジンでは、部分負荷時は理論空燃比で運転します。理論空燃比は、燃料と空気(酸素)が過不足なく燃焼する吸入空気と燃料の重量比で、14.7です。
理論空燃比に制御すると、三元触媒を使って排出ガス中の規制物質CO、HC、NOxを同時に低減できるからです。
リーンバーンとは、空燃比が理論空燃比14.7よりも大きい、すなわち燃料が少ない(薄い)混合気の希薄燃焼です。実際には、空燃比が約20以上の燃焼をリーンバーンと呼びます。リーンバーンが実現できれば、少ない燃料で走行できるため燃費は向上します。
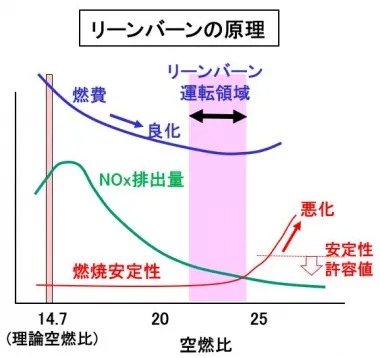
リーンバーンを実現するには
三菱のGDIやトヨタのD-4(Direct Injection 4-stroke)エンジンのリーンバーンは、成層燃焼によってリーンバーンを実現しました。
成層燃焼は、圧縮行程後半に燃料を噴射し、筒内全体としては希薄混合気でありながら、点火プラグ付近に着火可能な濃い混合気を集めて、安定した希薄燃焼(リーンバーン)を実現する手法です。
成層燃焼によってリーンバーンを実用化する手法としては、以下の2つのコンセプトがあります。
・三菱やトヨタが採用したピストンのキャビティを利用して、濃い混合気を点火プラグ近傍に集めるウォールガイド方式
・メルセデス・ベンツやBMWが採用している噴霧自身の貫徹力を利用して、混合気を層状化するスプレーガイド方式
いずれも点火プラグ近傍に濃い混合気を集めて、着火を安定させることがポイントです。
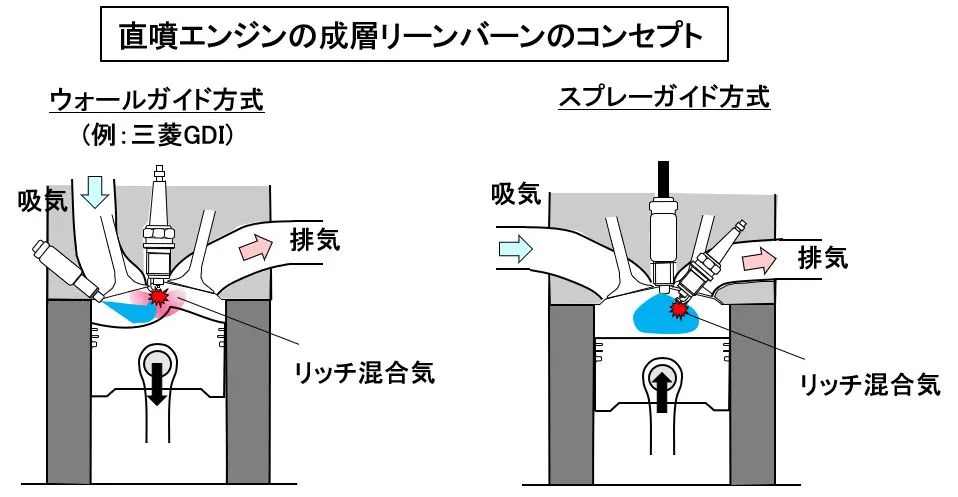
成層リーンバーンエンジンの問題点
当時の2000年以前は、三菱やトヨタのように成層燃焼によってリーンバーンを実現していました。しかし、成層燃焼には以下に挙げる課題があり、それを完全に解決することはできませんでした。
・カーボンデポジット(堆積)
成層燃焼は、局所(プラグ付近)では濃い混合気の燃焼になるので、煤(カーボン)が発生します。特に、燃焼室からの吹き戻しによって煤が吸気弁背面や吸気ポートに堆積します。これが、吸気量や吸気の流れに悪影響を与えて、燃焼が不安定になります。
・燃料希釈によるエンジンオイルの増量
負荷の高い領域では、燃料噴霧はライナーに直接衝突するため、燃料がエンジンオイルに混入してオイル希釈が起こります。特に、油温が低く燃料が蒸発しにくい条件では顕著になり、オイルの潤滑性低下やオイル量増大を招きます。
・排出ガス規制対応の難しさ
リーンバーンエンジンでは、三元触媒が使えず、NOx還元触媒が必要です。当時のNOx吸蔵触媒は、浄化効率が低いため、次期排出ガス規制への適合が困難でした。
当時は、カーボンデポジットによる信頼性の低さと排出ガス規制への適合性の困難さが、筒内噴射リーンバーンエンジンの普及に大きな障害となりました。
現在もリーンバーンエンジンは、燃費向上の有望な技術のひとつです。
多くのメーカーは、リーンバーンを成層燃焼でなく、NOxをほとんど排出しないHCCI(予混合圧縮着火)のような均一予混合の燃焼で実現することを目指しています。マツダがマツダ3に搭載したSKYACTIV-Xというエンジンは、その先駆け的な存在です。
■コモンレール噴射システムとは
コモンレール噴射システムの出現によって、ディーゼルエンジンは大きく進化しました。噴射圧の高圧化とともに、多段噴射によって燃焼を自在に制御できることが、最大のメリットです。
噴射の自由度が高いコモンレール噴射システムの構成やメリットについて、解説していきます。
ディーゼル噴射システムの歴史
ディーゼルエンジンは、コモンレール噴射システムになる以前は、分配型燃料ポンプ式の噴射システムを主に採用していました。分配型燃料ポンプは、回転するカムでプランジャーを作動させて高圧を発生させる燃料ポンプです。
この分配型ポンプに、燃料圧力によって弁開閉を行う自動噴射弁を組み合わせて、燃料をシリンダー内に噴射していました。
1995年に、噴射自由度の高い電子制御のコモンレール噴射システムが実用化されました。高圧噴射や1回の燃焼行程中に噴射を複数回分割する多段(マルチ)噴射など、高精度に燃料噴射が制御できるため、排出ガス規制の強化とともに急速に普及しました。
コモンレール噴射システムの構成
コモンレール噴射システムは、ガソリンの噴射システムと同様、あらかじめ高圧の燃料をコモンレール(デリバリーパイプ)に蓄えておき、電磁タイプの高圧噴射弁で燃料を噴射します。
燃料(軽油)は、燃料タンクから高圧ポンプに内蔵されたフィードポンプで吸い上げられ、高圧(サプライ)ポンプで昇圧されます。コモンレールに圧送された燃料は、圧力コントロールバルブによって既定の圧力に調整されます。
高圧ポンプは、プランジャーの往復運動により、燃料を吸入・圧送しますが、本体はベルトやチェーンを介してエンジンで駆動します。
高圧噴射弁は、ソレノイドコイルのON/OFFでコマンドピストンを作動させることで、噴射弁を開閉します。燃料の微粒化と分散性のため、6~8個程度の多噴孔ノズルを使い、噴射圧は最高で200MPaを超える仕様もあります。
ピエゾ式噴射弁
コモンレール噴射システムの噴射弁としては、ソレノイドタイプが一般的ですが、高級ディーゼル車の一部では応答性の高いピエゾタイプの噴射弁を採用しています。
ピエゾ噴射弁は、電圧をかけると伸張するピエゾ素子を弁開閉のアクチュエーターとして使用します。コストは高いですが、応答性に優れ、より精度高く噴射量と噴射時期を制御できます。
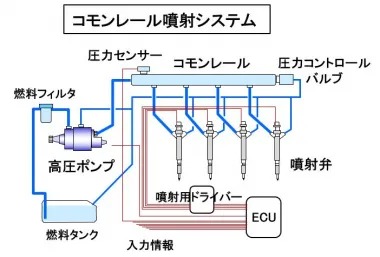
コモンレール噴射システムのメリット
コモンレール噴射システムによって、燃料噴射の噴射量や圧力、噴射時期、噴射回数を自在に制御できるようになりました。特に、1回の燃焼行程中に噴射を複数回に分割する多段(マルチ)噴射によって、ディーゼルエンジンの課題であった排出ガスと燃焼音を同時に低減できるようになりました。
噴射パターンは、運転条件に応じてエンジン回転数と負荷(噴射量)によって使い分けます。典型的な多段噴射は、主噴射の前のパイロット噴射とプレ噴射、主噴射の後のアフター噴射とポスト噴射の計5回噴射です。
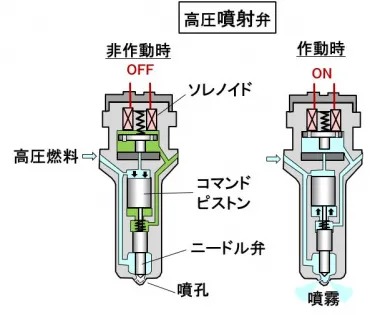
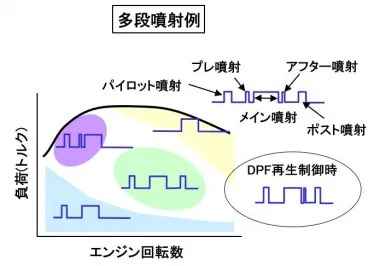
ディーゼル乗用車の排出ガス規制は、2000年以降、段階的に強化され、コモンレール噴射システムも高圧化と高応答性を目指して、進化し続けています。
一方、コストは後処理システムも加えて上昇傾向にあり、ガソリンエンジンに対して大きなデメリットとなっています。これが、ディーゼル車普及の足かせとなっており、特に日本では普及の兆しは見えてきません。
■副室ディーゼルエンジンとは
ディーゼルエンジンは、コモンレール噴射の直噴エンジンが主流ですが、1990年以前には副室ディーゼルエンジンが主流でした。
主燃焼室の他に副燃焼室設けた副室エンジンの採用例はほとんどありませんが、副室ディーゼルエンジンとその噴射システムについて、解説していきます。
副室ディーゼルエンジンの概要
現在主流の直噴(DI:Direct Injection)エンジンは、高圧で多段噴射もできるコモンレール噴射を組み合わせて、燃費と排出ガスを低減して高出力も実現しています。
主燃焼室の他に副燃焼室(副室)を設けた副室(IDI:Indirect Injection)エンジンは、直噴エンジンが開発される以前の旧世代のディーゼルエンジンです。副室エンジンでは、副室内に燃料を噴射して着火させて、副室の燃焼ガスが絞り(主室と副室の連通管)を通じて主室内に噴出して燃焼が完了します。
副室ディーゼルエンジンの構成
副室エンジンには、副室の燃焼形態の違いで2種類あります。
・渦流室式
主燃焼室の上部に球型またはまゆ型の副燃焼室(主燃焼室容積の60~80%)を設けて、吸入空気は圧縮行程中に渦流室に押し込まれ、強い渦流を発生します。上死点前に噴射した燃料は、ほとんどすべて渦流室内で燃焼して、主室側に噴出してピストンを押し下げます。
・予燃焼室式
予燃焼室の容積は主燃焼室容積の30~40%程度で、予燃焼室で噴射した燃料の一部を燃焼させます。着火後に燃焼ガスと燃料の混合気が噴流となって、主室へ噴出して燃焼が完了します。予燃焼室は、着火装置のような役目を果たします。
予燃焼室の方が比較的穏やかな燃焼になりますが、高回転化には向かないなど一長一短があります。通常は、高回転型の渦流式が商用車と乗用車に採用されていました。
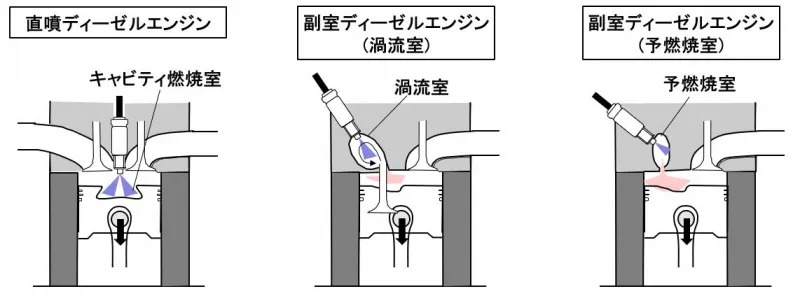
副室ディーゼルエンジンのメリットとデメリット
1990年以前は、直噴エンジンに対応できる微粒化と分散性に優れた高圧噴射弁がまだ開発されておらず、副室エンジンが主流でした。また日本では、当時もディーゼル車の数は限られており、一部の商用車に搭載されていましたが、乗用車ディーゼルはほとんどありませんでした。
限られた副室内で燃料を噴射するので、低圧の噴射弁でも確実に着火できます。現行のコモンレール噴射では200MPaを超える噴射圧仕様もありますが、副室の噴射圧は最高で40MPa程度です。また、副室内は空気量が少なく燃焼圧と燃焼温度が低いため、ディーゼルノックが発生しづらく、NOx生成量が少ないという特徴がありました。
しかし高温の燃焼ガスが絞り部を往来する、また燃焼室表面積が大きいため、絞り損失と熱損失が大きいという弱点がありました。結果として、直噴エンジンに対して5~10%程度燃費が悪化します。また、シリンダーヘッド内に副室を設けるために、耐久信頼性を確保するのが難しく、高回転化には限界がありました。
燃焼音が小さくNOx排出量が少ないというメリットはあるものの、燃費が直噴エンジンに比べて劣ること、さらに4弁エンジンでは副室を設けるスペースが確保できないことが致命的でした。2000年頃には、一部の新興国向け以外は市場から姿を消しました。
直噴ディーゼルエンジンが出現した2000年頃は、まだ完成度が低く、ディーゼルノックによる騒音が大きく、排出ガス性能も満足できるレベルではありませんでした。高出力用エンジンには直噴エンジン、低出力用エンジンには副室エンジンと棲み分けしていた時期もありました。
その後10年も経たないうちに、コモンレール噴射システムと直噴エンジンが急速に進化したため、副室ディーゼルエンジンは世界市場から消え去りました。
■燃料蒸発ガス(エバポ)とは
未燃燃料に由来する炭化水素(HC)や燃焼で生成するHCは、排気管から排出されるだけでなく、燃料タンクや燃料ホースなどからも蒸発ガスとして放出され、排出ガスの規制対象となっています。
ガソリン車から放出される燃料蒸発ガスの発生要因と抑制方法などについて、解説していきます。
燃料蒸発ガスの概要
ガソリン車では、排気管から放出される排出ガス中のHCだけでなく、燃料タンクや燃料ホースなどから燃料の蒸発ガスHC(エバポ)が放出されます。
燃料蒸発ガスは走行中だけでなく、駐車時や給油時にも排出され、その主成分HCは光化学オキシダントやPM2.5の原因物質です。したがって、国内外において厳しい燃料蒸発ガス規制(エバポ規制)が施行されています。
燃料蒸発ガスの発生要因
燃料蒸発ガスには、主に3つの発生要因があります。
・透過
燃料ホースやその接続部、燃料タンクのようなゴムや樹脂などの微小な孔を通じてガス成分が放出する現象です。
・波過
蒸発ガスの排出抑制装置である活性炭キャニスター(後述)がオーバーフローして、蒸発ガスが放出する現象です。
・給油時
給油時には、燃料タンクの給油口や給油ノズルとの隙間から、蒸発ガスが放出します。
透過は、ガソリン成分が透過しにくい材質を使用することである程度抑えられます。波過については、キャニスター容量の最適化やキャニスター制御の最適化が行われています。
最後の給油時の燃料蒸発ガスについては、米国では規制されていますが、今現在、欧州や日本ではまだ規制対象ではありません。しかし、2010年以降日本でも問題視され始め、多くのガソリンスタンドに燃料蒸発ガス回収機能付き給油機が設置されるなど、規制化の動きが活発化しています。
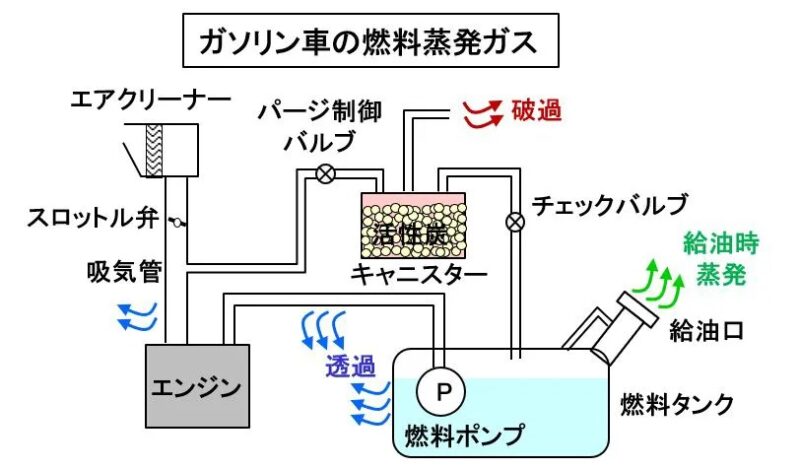
活性炭キャニスターの役割
燃料蒸発ガス対策として、ほぼすべてのガソリン車が採用しているのが、活性炭キャニスターです。
活性炭キャニスターは、筒状の容器に詰めた活性炭でガソリン蒸気を吸着して、一定量溜まると、エンジンの吸気管に投入して再燃焼する装置です。
キャニスターには、ガソリン蒸気を回収する配管と、エンジンの吸気系に送り込む配管、外気を取り入れる配管が繋がっています。エンジンの吸気管と繋がっている配管には、蒸発ガスのパージ量を制御する電磁弁が装着されています。
エンジン駆動時には吸気管に負圧が発生するので、活性炭に吸着していた蒸発ガスは、外気から吸入される新気によって分離され、エンジンの吸気管に供給されて燃焼します。同時に、キャニスター内には新気が充満して、次の吸着を始めます。
燃料蒸発ガス規制の現況
米国が先行して、日本は追従する形で燃料蒸発ガス規制を強化しています。ただし、米国が規制している給油時の燃料蒸発ガスについては、今現在日本では規制対象にしておらず、その必要性が議論されています。
燃料蒸発ガスの発生は、走行時と停止直後、駐車時、給油時に分類されます。
日本での計測は、停車直後と駐車場での長時間放置を想定した2つの試験「暖気放置時排出試験」と、「終日保管時排出試験」を、「SHED(Sealed Housing for Evaporative)」という専用の試験設備で実施します。
SHED試験
SHEDは、車全体から放出される燃料蒸発ガス量を計測する密閉室です。試験走行直後の車をSHEDに入れ、室温を試験法に従って変化(20~35度)させて、車全体から放出される燃料蒸発ガス量、すなわち試験室内に溜まったHC重量を計測します。
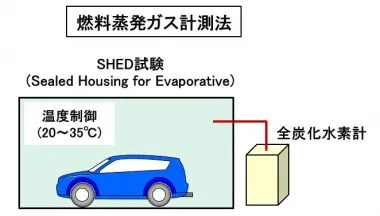
燃料噴射システムとは直接関係ありませんが、燃料系に係るテーマということで取り上げました。
室内がガソリン臭いと感じたら、キャニスターなどの燃料ガス蒸発抑制装置周辺の漏れを疑ってみてください。
(Mr.ソラン)
クリッカー自動車用語辞典 https://clicccar.com/glossary/