目次
■車のエンジンとは
エンジンは、車の動力源であり、車の心臓部です。いろいろなタイプの車があるように、それに合わせて多種多様なエンジンがあります。
出力と燃費を向上させ、有害な排出ガスを低減させる最新技術を理解するためにも、まずはエンジンに関する基本構成と技術を知っておきましょう。
4ストロークエンジン
自動車用エンジンの主流は、4ストロークのレシプロ(往復ピストン)エンジンです。かつては、マツダが採用したロータリーエンジン(別頁で解説)がありましたが、2012年のマツダRX-8生産終了以降は、2023年5月現在まで生産されていません。
エンジンは燃焼行程で燃料を燃焼(爆発)させてピストンを押し下げ、そのエネルギーをエンジンの回転力として取り出します。燃料の持つ化学的エネルギーを機械的エネルギーに変換する装置です。
ガソリンエンジンでは、まず吸気行程で燃料と空気の混合気をシリンダーに吸入し、圧縮行程で吸入した混合気をピストンで圧縮します。次の燃焼行程で圧縮した混合気に点火プラグで点火して燃焼させ、最後の排気行程で燃焼ガスをシリンダーから排出する、といった一連の行程を繰り返します。
ディーゼルエンジンでは、空気のみを圧縮して高温になった圧縮空気中に、軽油を噴射し、蒸発した軽油が自着火して燃焼します。

エンジンの排気量と気筒配列
車のコンセプトや大きさ、目標出力と目標燃費を設定すれば、目標に見合ったエンジンの排気量や気筒数、気筒配列が決まります。気筒配列において通常は、直列配列とV型配列が一般的ですが、希少な配列としてポルシェとスバルが採用している水平対向エンジン(別頁で解説)があります。
圧縮比
圧縮比を上げるほど、エンジンの熱効率が上がり、燃費と出力が向上します。
ガソリンエンジンでは、それほど高温でない圧縮混合気であっても火花点火すれば燃焼するので、ノッキングが発生しない比較的低めの圧縮比(9〜12)に設定します。一方、ディーゼルエンジンは圧縮空気温度を上げて自着火させるため、高い圧縮比(17〜18)に設定します。
動弁系システム
動弁系は、吸気弁と排気弁を適切なタイミングで開閉する重要な役目を担っています。エンジンの吸気行程では吸気弁の開閉によって空気と燃料をシリンダー内に吸入し、排気行程では排気弁の開閉によって、燃焼ガスをシリンダーの外に排出します。
筒内流動(スワールとタンブル)
燃焼を活性化して燃焼速度を上げるためには、シリンダー内に流動(乱れ)が必要です。ディーゼルエンジンでは水平方向の「旋回流スワール」、ガソリンエンジンでは縦渦・垂直方向の「旋回流タンブル」が活用されます。スワールやタンブルを強化するために、吸気ポート形状やピストン頂面形状を最適化します。
フリクション
エンジンの損失のひとつであるフリクションは、主としてクランクシャフトやピストンなどの回転運動や往復運動時に発生する機械損失です。要素部品ひとつひとつの低減効果は小さくても、その積み重ねによってエンジン全体のフリクションが下がり、燃費改善につながります。
フライホイール
シンプルな構造ながら、エンジンをスムーズに回すという基本的な役目を担っています。それとともに、一方で車のレスポンスを左右する重要な部品です。
バランサーシャフト
ピストンエンジンでは、ピストンの往復運動で発生する慣性力に起因する振動は避けられません。この振動を抑制するために、一般的に採用されているのがバランサーシャフトです。
■ガソリンエンジンとディーゼルエンジンとは
自動車用エンジンはガソリンとディーゼルに大別できる
自動車用エンジンは、乗用車で一般的な「ガソリンエンジン」と、トラック・バスなどの大型車の「ディーゼルエンジン」に大別されます。ガソリンエンジンは、ガソリンを燃料とする「火花点火エンジン」、ディーゼルエンジンは軽油を燃料とする「圧縮自着火エンジン」です。
この項では、2つのエンジンの違いと特徴、得失について解説していきます。

ガソリンと軽油は何が違うのか
エンジンの違いの前に、まずガソリンと軽油の燃料性状の違いに触れておきます。
いろいろな成分が混合している原油から蒸留温度を調整することによって、ガソリン・灯油・軽油・重油などが抽出されます。
ガソリンは沸点が30〜220°Cの成分、軽油は沸点が200〜350°Cの成分です。引火点はガソリンが−40°C以下に対して、軽油は40°C以上。着火点(発火点)はガソリン約300°Cに対して、軽油は約250°Cと性状が異なります。
ガソリンは、蒸発しやすく炎を近づけると常温でも容易に引火し、軽油は蒸発しにくいですがガソリンよりも低い温度で着火(発火)します。
ガソリンエンジンとディーゼルエンジンの違い
2つのエンジンの最大の違いは、前述の燃料性状の違いに起因する燃焼方式です。
ガソリンエンジンは、ガソリンの混合気を圧縮して点火プラグの火花で混合気に点火(引火)し、燃焼する火花点火方式です。一方、ディーゼルエンジンは空気のみを圧縮して高温になった圧縮空気中に微粒化した軽油を噴射し、蒸発した軽油が自着火(発火)する圧縮自着火方式です。
ガソリンエンジンは、それほど高温でない圧縮混合気でも点火すれば燃焼するため、ノッキングが発生しない比較的低めの圧縮比(9〜12)に設定します。一方ディーゼルエンジンは、圧縮空気温度を上げて自着火させるため、高めの圧縮比(16〜18)に設定します。
ガソリンエンジンとディーゼルエンジンの得失
燃費はディーゼルエンジンの方が15〜20%程度優れています。ディーゼルエンジンは圧縮比が高いため熱効率が高く、さらに吸入空気量を制御するスロットルが通常はないため、ポンピング損失が小さく燃費向上に寄与しています。
ガソリンエンジンも燃費を良くするため圧縮比を上げたいのですが、圧縮比を上げていくとノッキングが発生するため、現状は圧縮比12〜13程度が限界です。
出力についてはディーゼルエンジンはほぼすべてターボ付きですが、ノッキングによる出力低下がないので、低中速トルクが高くなります。一方、 爆発圧力が高く頑強な構造のディーゼルエンジンは、機械損失が大きいため高回転化に不向きで、ガソリンエンジンの方が高回転高出力です。
排出ガスについては、ガソリンエンジンは三元触媒によって比較的容易に浄化できます。ディーゼルエンジンは、自着火燃焼に起因するスモークの発生やNOx(窒素酸化物)の排出量が多い特性があるため、排ガス浄化のための触媒システムが複雑で高価です。
日本でディーゼル車があまり普及しない理由
圧縮比が高いディーゼルエンジンは、爆発圧力が高いので頑丈で重く大きくなり、また振動や騒音も悪化します。加えて高圧の噴射システムが必要なため、エンジンコストが高くなってしまいます。
燃費が良く、軽油も安いのに、なぜ日本ではディーゼル乗用車が普及しないのでしょうか。
それは、エンジン本体と排ガス対策のためにコストがかかり、ディーゼル車が高価であること、振動騒音でまだガソリン車に劣ること、欧米に比べて日本は生涯走行距離が短く低燃費の恩恵を得にくいこと、いまだにディーゼル車に「汚い、うるさい」というネガティブイメージが強い、などが理由ではないでしょうか。
ガソリンエンジンとディーゼルエンジンの良いとこ取りの発想から、「直噴ガソリンエンジン」や「HCCI(予混合圧縮着火)エンジン」が生まれました。従来の火花点火燃焼、圧縮自着火燃焼とは異なる新しい燃焼方式の開発が、エンジンに魅せられた”エンジン屋”永遠のテーマです。
■気筒数と気筒配列とは
排気量や気筒数、気筒配列を決める要素
車のコンセプトやサイズ、それに見合ったエンジンの目標性能が設定されれば、最適な排気量や気筒数、気筒配列が決まってきます。排気量や気筒数、気筒配列はどのようにして決められるのか、解説していきます。

1気筒あたりの適正な排気量
車のコンセプトやサイズ、目標性能などによって、エンジンの排気量が決まります。排気量が決まれば、次はエンジンの気筒数や1気筒あたりの排気量(ボア×ストローク)などの基本構成が決まります。
ガソリンエンジンの場合、高い熱効率を得るために1気筒あたりの排気量を400〜600ccに設定することが重要です。1気筒あたりの排気量が大き過ぎるとノッキングしやすく、燃焼期間が長期化します。また、排気量が小さ過ぎると熱損失が大きくなり、いずれの場合も熱効率が下がります。
軽自動車のように総排気量(660cc)が小さい特殊なエンジンでは、振動の問題から単気筒や2気筒にできないので3〜4気筒とし、1気筒あたりの排気量はやむを得ず適正な排気量より小さくしています。
※豆知識…小型車(1.0〜1.4L)では、かつては振動に有利な4気筒が主流でしたが、最近は3気筒エンジンが増えています。低振動技術が進んだため、1気筒あたりの排気量を増やす3気筒化によって機械損失を下げ、熱効率を上げて燃費を向上させるのが狙いです(4→3気筒によって、部品数が減り、コストが下がる効果もあります)。
直列エンジンとV型エンジン
エンジンルームの広さには限りがあるため、搭載するエンジンは極力コンパクトにする必要があります。直列エンジンの場合はエンジンの長さが搭載上の課題であり、またクランクシャフトが長くなるため剛性面でも不利です。
車にもよりますが、一般的に直列では6気筒が限界です。そのため、最近は直列6気筒ではなく、V型6気筒を採用する例が多くなっています。8気筒となると、直列ではさらに搭載が困難で、V型が一般的です。
V型の最大のメリットは搭載性です。幅は広がりますが長さが短くなり、コンパクトです。しかし、シリンダーヘッドが2分割になるなど、部品点数が増えて、構造が複雑でコストが上がるというデメリットがあります。

気筒数と振動特性
4ストロークエンジンでは、吸気・圧縮・燃焼・排気行程の4行程の中で、トルクを発生するのは燃焼行程だけなので、トルク変動が発生します。気筒数が多くなると、1回転中にどこかの気筒で燃焼行程が発生するため、トルク変動による振動が小さくなり、回転が滑らかになります。
最も多く採用されている直列4気筒では、「2次振動」が問題です。2気筒ずつ対称的な動きをしてバランスが取れているようですが、実はピストンが下向きに動く速度より上向きに動く速度の方がわずかに速いので、その差が振動を発生させます。
エンジンを揺さぶる偶力振動
一方、3気筒などの奇数気筒では、クランクシャフトの中央位置を中心にピストン配置を対象にできないので、エンジン自体を上下に揺する「偶力振動」が発生します。奇数気筒数の大きなデメリットです。
V6・V8気筒でも、1次・2次振動は釣り合いますが、偶力は発生するため、バランスウェイトが必要です。
※豆知識…直列6気筒エンジンは、「完全バランスエンジン」と呼ばれます。燃焼間隔が120°のため、ピストンの慣性力と偶力が互いの気筒で打ち消し合うため、2次振動、偶力振動も抑えることができるのです。
気筒数や気筒配列は、性能、振動、コスト、搭載性など総合的に判断して、設定されます。スバルとポルシェが採用する個性的な水平対向エンジンについては、別項で解説します。
■ロングストローク、ショートストロークとは
ロングストロークとショートストロークの得失
同じ排気量のエンジンでも、ボア径とストローク長さが変われば、エンジンの特性は大きく変わります。目標とする出力性能や燃費性能によって、ロングストロークかショートストロークかの設定が決まります。この項では、ロングストロークエンジンとショートストロークエンジンの得失について、解説していきます。

ボア/ストローク比
エンジンの排気量は、シリンダーの内径(ボア)とピストンが上下運動する上死点から下死点までの移動する距離(ストローク)で決まります。具体的には、以下の式で示されます。
排気量=ボア×2×3.14(円周率)×ストローク×気筒数÷4
ボアよりもストロークが長いと「ロングストローク」エンジン、ボアよりもストロークが短いと「ショートストローク」エンジン、またボアとストロークがほぼ同じ場合は「スクエア」エンジンと呼ばれます。
ロングストロークエンジンの特性
ロングストロークエンジンでは、ボアが小さいので燃焼室は丸みを帯びたコンパクトな形状になり、同じエンジン回転数でもピストンの上下移動速度は大きくなります。このディメンションがエンジンの特性に大きな影響を与えます。
燃焼室がコンパクトになると、燃焼室の表面積が小さくなり、SV比(燃焼室の表面積と容積の比率)が小さくなります。これにより、燃焼による発熱が壁面から放出される割合が少なくなるため、熱損失が小さくなります。また、ピストン速度が大きくなるとシリンダー内の空気流動が活発になり、燃焼速度が速くなります。
つまり、ロングストロークエンジンは、熱損失の低減と燃焼速度の急速化によって、燃費が良くなります。
一方、デメリットもあります。燃焼室がコンパクトであるということは、吸・排気弁が大きく設定できないため、吸入空気量が減少します。またピストン最高速度が上がるとピストン慣性力が大きくなるため、ピストン、コンロッド、クランクシャフトなどの補強が必要となり、フリクションが大きくなります。
ロングストロークエンジンは燃費は良いですが、高回転・高出力化には向いていません。ただし、低中速域では吸気弁の大きさによる吸入空気量の制約は少なく、コンパクトな燃焼室はノッキングが発生しにくいことから、ロングストロークの方が出力が出やすくなります。
ショートストロークエンジンの特性
ショートストロークエンジンは、ロングストロークエンジンと全く逆の特性を示します。ボアが大きいので燃焼室は扁平な形状になり、同じエンジン回転数でもピストン速度は小さくなります。
燃焼室が扁平ということはSV比が大きくなって熱損失が大きくなるため、燃費には不利です。一方、吸・排気弁を大きく設定でき、ピストン速度も小さいため、高回転化に対応できます。
ショートストロークエンジンは、燃費は良くないですが、高回転・高出力化に向いているエンジンです。
スクエアエンジン
ボアとストロークがほぼ同じエンジンは、エンジンの縦断面でみて、ボアとストロークが1:1になるのでスクエアエンジンと呼ばれています。
ロングストロークとショートストロークの中間的な特性を持ち、燃費が今ほど重視されてなかった1990年頃までは主流でしたが、現在は一般的な量産車は圧倒的に燃費の良いロングストロークエンジンが多いです。
一言で表すと、ロングストロークエンジンは低燃費型、ショートストロークエンジンは高出力型です。燃費を重視する一般的な量産車にはロングストロークエンジン、出力性能を重視するスポーツ車やレース車にはショートストロークエンジンが採用されています。
■水平対向エンジンとは
スバルとポルシェはなぜ水平対向にこだわるのか
水平対向エンジンといえば、すぐにスバルとポルシェを思い浮かべる人が多いと思います。直列エンジンとV型エンジンが主流の中にあって、2つの自動車メーカーが水平対向エンジンにこだわるのには、それなりの理由があるはずです。この項では、水平対向エンジンの特徴、メリットとデメリットについて解説していきます。

水平対向エンジン
現在広く採用されているのは直列エンジンです。全幅は抑えられますが、全長と全高は高くなります。吸・排気弁など動弁機構を組み込んだシリンダーヘッドは最もシンプルな構造になります。V型エンジンは、シリンダーを左右交互にV型に配置して、ピストンは斜めに往復します。全長が抑えられ全体にコンパクトな構造になる利点がありますが、シリンダーヘッドが左右ひとつずつ1対必要で、複雑な構造でコストが上がります。
さて、独特なメカニズムを持つ「水平対向エンジン」です。クランクシャフトに対してシリンダーを左右水平に配置し、左右に向かい合った一対のピストンが水平方向に往復するエンジンです。V型エンジンと同様に、シリンダーヘッドが左右1対必要です。
ボクサーがパンチを打ち合う様子に似ていることから、「ボクサーエンジン」とも呼ばれています。

水平対向エンジンのメリット
水平対向エンジンには、多くのメリットがあります。
・低振動
左右で対向しているピストンが互いの慣性力を打ち消すように対称的に往復運動するため、エンジンは振動が少なく、スムーズに作動します
・低重心
シリンダーが水平に配置されるため全高が低く、全幅が広い構造は低重心となります。しかも左右対称ですから、車両の安定した操縦性や走行性能に大きく寄与します
・高剛性
全長が短いのでクランクシャフトが短く、またクランクシャフトは左右クランクケースによって両側から強固に挟み込む構造なので、クランクケース全体の剛性が高くなります。高い剛性は、低振動と耐久信頼性の向上につながります
・高出力
パッケージングのためにエンジン全幅には制約があり、ショートストロークにならざるを得ません。このショートストロークと、本来持つバランスの良さが、高回転化と高出力を実現します
・衝突安全性
エンジンの全高が低いので、前面衝突したときにエンジンがフロアの下に潜り込み、乗員へのダメージが軽減できます
※豆知識…スバルの場合、低重心で左右対称といった水平対向エンジンの優位性と、相性の良い「フルタイムAWD(4駆)」技術を組み合わせて、「走りのスバル」「4駆のスバル」といった独自のブランドを築き上げました。
水平対向エンジンのデメリット
多くのメリットがありますが、一方で将来に向けたエンジンとしては、普及を妨げる「決定的なデメリット」があります。
水平対向エンジンは設計的な制約が多く、種々な要求に応える自由度がありません。全幅の制約からショートストロークで高出力向きですが、熱損失が大きく燃費は不利です。また、電動化技術との組合せも構造上、容易ではありません。
今後、様々な環境対応技術や電動化技術と組み合わせるためには、水平対向エンジンの適正化だけでなく、プラットフォームの改良など車体側の改良も必要です。
走りを追求する車のパワーユニットとして水平対向エンジンが持つ低重心は、最大のメリットです。環境対応技術で後れを取っていることが最大の問題ですが、今後も進化し続けて個性あるパワーユニットして存在感を示してほしいものです。
■ロータリーエンジンとは
RX-8の終焉とともに一度は生産を終えたが…
ロータリーエンジンといえばマツダですが、燃費の悪さが致命的となり、現在は、2012年のRX-8の終焉とともに搭載モデルは存在しません(2023年2月現在)。しかし、2023年初頭にマツダがロータリーエンジンを発電機として使うシリーズハイブリッド方式のプラグインハイブリッドSUV「MX-30 e-SKYACTIV R-EV」の市場投入を正式に発表(発売日は未定)しました。ロータリーエンジンの構造やメリット、デメリットについて解説していきます。

なぜロータリーエンジンは消えたのか
ロータリーエンジンはドイツ人の発明家ヴァンケルによって発案され、1964年NSU社のヴァンケルスパイダーに初めて搭載されました。しかし、オイル消費の増大やシール不良などの不具合が多発し、評価は得られませんでした。日本ではマツダが1967年にコスモスポーツに搭載し、以降2012年のRX-8の終焉まで多くのスポーツモデルで採用されました。
軽量コンパクトで高回転高トルクな特性がスポーツカーに向いており、熱烈なファンを獲得しました。一方で燃費の悪さもクローズアップされ、「ロータリーエンジンは燃費が悪い」というイメージも定着してしまいました。車好きには魅力的なエンジンでしたが、燃費が悪いのは致命的で、残念ながら自然消滅してしまいました。
ロータリーエンジンの作動原理
一般的なピストンエンジンでは、シリンダー内をピストンが2往復(エンジンが2回転)する間に「吸気」「圧縮」「燃焼」「排気行程」の4行程を行います。
ロータリーエンジンは、三角おむすび型のローターがトロイド曲線を持つ繭(まゆ)型のハウジング内部を、独特な動きで回転します。回転とともに、ローターとハウジングで形成される燃焼室が移動しながら、「吸気」「圧縮」「燃焼」「排気行程」の4行程を繰り返します。
ローター1回転で、通常エンジンのクランクシャフトに相当するエキセントリックシャフトが3回転するので、吸気、圧縮、燃焼、排気行程の4行程はエンジンで3回転(4ストロークエンジンでは2回転)に相当します。ローターには3辺(3つの燃焼室)があるので、結果として燃焼行程は1回転で1回発生します。2回転に1回の燃焼行程の4ストロークエンジンに対して、トルクは理論上2倍になります。
ロータリーエンジンのメリットとデメリット
往復運動を回転運動に変える通常のエンジンに対して、ダイレクトに回転が引き出せるロータリーエンジンは、ある意味、画期的なエンジンと言えます。4ストロークエンジンに対するメリットは、以下のとおりです。
・軽量コンパクト
ピストンや動弁系(吸排気弁など)が不要なため、その分コンパクトで軽量です。また、動弁系にかかわる部品がないため、関連するフリクションがありません。
・低振動/低騒音
ピストンの往復運動がないので騒音振動に優れています。
・高出力
1回転中に燃焼が1回発生するので、4ストロークエンジンに対して同じ排気量で出力は理論上2倍になります。また、トルク変動と回転変動が抑えられ、回転がスムーズです。
一方で、重大なデメリットがあります。
・燃費が悪い1.(燃焼効果)
吸排気弁がないため、吸排気効率が悪く、また混合気の流動が小さいため、不完全燃焼になりやすく、燃焼の効率が低いです。
・燃費が悪い2.(熱効率)
SV(燃焼室表面積/容積)比が大きい燃焼室形状のため、熱損失が大きく、熱効率が低いです。
・排気音が大きい
排気弁がなく、一気に燃焼ガスが排出されるため、排気音が大きくなります。
・エンジンオイルの消費量が多い
ローターハウジング内にも潤滑オイルが必要で、燃料とともにオイルも一緒に燃焼するため、オイル消費が大きくなります。
ロータリーエンジンは、今後さらに厳しくなる燃費規制と排出ガス規制をクリアすることは非常に厳しいというのが、一般的な見解です。
一方、2023年初頭にマツダが、ロータリーエンジンを発電機として使うシリーズハイブリッド方式のプラグインハイブリッドSUV「MX-30 e-SKYACTIV R-EV」の市場投入を正式に発表(発売日は未定)しました。発電機用エンジンであれば、コンパクトで軽量という扱いやすいロータリーエンジンの特徴が生かせるかもしれません。
■圧縮比とは
エンジンの熱効率を決定する重要な因子
圧縮比は、エンジンの熱効率、すなわち出力や燃費を決定する重要な因子です。圧縮比の定義、ガソリンエンジンとディーゼルエンジンの圧縮比設定の考え方の違いについて解説していきます。

圧縮比と膨張比
圧縮比とは、「シリンダー内の空気または混合気が、ピストン上昇によってどれくらい圧縮されるのか」の割合を示す指標で、次の計算式で表されます。
圧縮比=(燃焼室容積+排気量)÷燃焼室容積
燃焼室容積とはピストンが上死点(往復運動するピストンが最も上昇した位置)での容積、排気量とはピストンが往復運動する間の容積で「ボア×2×3.14(円周率)×ストローク×気筒数÷4」です。
一方、膨張比とは、「燃焼ガスがピストン下降によってどれくらい膨張するか」の割合を示す指標で、通常は圧縮比と同じ値を示します。
熱効率は、燃焼エネルギーがどれだけピストンを押し下げる機械的エネルギーに変換されるかの割合です。したがって、熱効率は本来、膨張比に依存しますが、一般には圧縮比=膨張比なので、両者を区別せず代表して圧縮比が使われます。
熱効率は、圧縮比(膨張比)の上昇とともに向上しますが、圧縮比が14より高くなると向上率は頭打ちになる傾向があります。圧縮比を上げていくと燃焼室容積が減るため、SV比(燃焼室表面積/容積)が増大して、壁面からの熱損失が増えてしまうからです。
エンジンは、発生した燃焼エネルギーの多くを排出ガスの熱として捨てます。圧縮比(膨張比)を高くすればするほど、ピストンが下降する間に燃焼ガスは膨張して排出ガス温度が下がり、捨てるエネルギーが減るため、その分、仕事量が増えます。このように考えると、圧縮比(膨張比)が高ければ熱効率が高いということが理解しやすくなります。
ガソリンエンジンの圧縮比設定
ガソリンエンジンでは圧縮比を上げるとノッキングが発生するため、一般的には圧縮比10〜13程度に設定されます。
ノッキングとは、火花点火による火炎が到達する前に、燃焼室端部の未燃ガスの温度が上がって自着火してしまう現象です。高温高圧の激しい燃焼なので、燃焼室内で高周波の圧力振動が起こり、カリカリといった音が発生し、最悪の場合は熱によってピストンが溶損する原因になります。
ノッキングの発生を抑えるため、燃焼室形状の最適化や、未燃ガスの温度を下げるために、燃焼室の冷却性を向上させるといった手法が採用されています。
過給エンジンの場合は、ピストンで圧縮する前にすでに吸気が過給によって圧縮されています。したがって、圧縮後のシリンダー内温度が高くノッキングしやすいため、圧縮比は8〜9程度と低く設定されます。その分、燃費は悪くなってしまいます。
ちなみに、2018年春に「夢のエンジン」と呼ばれた可変圧縮比エンジンが、日産によって実用化されました。運転条件に応じて自動的に最適な圧縮比に設定することができるため、燃費と出力を両立します。
独自の可変圧縮比機構によって、低回転・低負荷運転条件では燃費のために圧縮比を高く、高回転・高負荷運転条件ではノッキングの発生を抑えるため圧縮比を低く設定します。
ディーゼルエンジンの圧縮比設定
ディーゼルエンジンは、着火性の良い軽油を使った圧縮自着火エンジンです。圧縮高温の空気に燃料を噴射して燃焼させるため、圧縮比は一般には17〜18程度に設定します。ガソリンエンジンに比べて圧縮比が高いので、熱効率が高く、燃費が良くなります。
ただし、圧縮比が高いために有害ガスNOx(窒素酸化物)が排出されやすく、またエンジン各部が頑強な構造になるためフリクションが大きくなります。
2010年以降は、マツダのSKYACTIV-Dエンジンのように、NOx低減やフリクション低減のため、圧縮比を15以下に下げたディ-ゼルエンジンが出現しています。圧縮比を下げると圧縮温度が下がり着火性が悪化するので、低温始動性や燃焼安定性を改良する技術が必要です。
燃焼方式の違いによって、ガソリンエンジンとディーゼルエンジンで圧縮比の目指す方向が真逆である点が、興味深いですね。
■吸・排気弁とは
混合気と排出ガスを制御する重要な機構
「吸気弁」は、エンジンのシリンダー内に供給される空気を制御し、「排気弁」はシリンダーから排出される燃焼ガスを制御する重要な役割を担っています。吸・排気弁の役割と弁駆動の仕組み、どのようなタイミングで開閉するのかを解説していきます。

吸・排気弁の役割
吸・排気弁とそれを動かす動弁系機構は、エンジン上部のシリンダーヘッドに組み込まれています。
吸気弁はシリンダーヘッドに形成された吸気ポートの入り口に配置され、シリンダーの中に空気または燃料と空気の混合気を送り込んだり、止めたりします。排気弁は排気ポートの出口に配置され、シリンダーの燃焼ガスを排気管に排出したり、止めたりします。
弁(バルブ)は、ステムと呼ばれる棒状の先端に円形の傘が付いたキノコ形状のポペット弁です。上下に動く弁傘部の弁フェースと、吸・排気ポートそれぞれに装着された弁座(弁シート)の間隔(弁リフト)によって、流れを開放したり遮断したりします。
最近のエンジンは、1気筒あたり吸・排気弁がそれぞれ2個、合計4個ある4弁エンジン(4バルブエンジン)が一般的です。
吸・排気弁の開閉時期
吸・排気弁は、どのようなタイミングで開閉するのでしょうか。
4ストロークエンジンは、4つの行程で構成されています。この4行程でエンジンは2回転して、それを連続的に繰り返すことによって、回転を持続します。
・吸気行程
ピストンが下降し始める上死点(最上点)直前に吸気弁を開いて、シリンダー内に空気または混合気を吸い込みます。ピストンが下死点(最下点)を過ぎてから吸気弁を閉じます。
・圧縮行程
吸入した空気または混合気を圧縮するので、吸・排気弁とも閉じています。
・燃焼行程
圧縮した混合気に点火(ガソリンエンジン)あるいは自着火(ディーゼルエンジン)によって、燃焼してピストンを押し下げます。吸・排気弁は閉じたままです。
・排気行程
ピストンが上昇し始める下死点より前に排気弁を開いて燃焼ガスを排出します。上死点直後に排気弁を閉じます。
空気には重さがあり慣性によって遅れが生じるので、吸気弁の閉時期は下死点をある程度過ぎてから閉じます。一方排気弁については、燃焼によって圧力が上昇するので、できるだけ効率よく燃焼ガスをシリンダー外に排出するために、下死点より前に排気弁を開きます。閉じるのは上死点直後です。
※豆知識…排気弁は上死点後に閉じ、吸気弁は上死点前に開くようにします。この上死点前後で、排気弁と吸気弁の両方が少しだけ開いている期間をオーバーラップと呼びます。オーバーラップ期間の長さによって、残留ガス量が増減し、燃費や排出ガス特性は大きな影響を受けます。
弁駆動の仕組み
吸・排気弁は、ピストンの動きに連動してカムシャフトで駆動します。
カムシャフトには、目標とする弁の開閉時期やリフトを実現するプロファイルをもつ、卵の断面のような形状のカムが、吸・排気弁の数だけ配列されています。このカムシャフトを、クランクシャフトが2回転する間に1回転するように、タイミングベルトまたはタイミングチェーンで連動させます。
カムの配置については、1つのカムシャフトで吸・排気弁を駆動させるSOHC方式、吸・排気それぞれに1つのカムシャフトで駆動させるDOHC方式があります。
弁の形状は、エンジンが誕生してからほとんど変わっていません。しかし、弁開閉機構は大きく進化し、運転条件に応じて開閉時期や弁リフト量を変更できる可変動弁機構は、ごく一般的な技術となりました。動弁系機構はすでに円熟した技術ですが、次の目標はカムを使わず、弁リフトカーブまで自在に制御できる電動の弁駆動方式でしょうか。
■動弁機構とは
適切なタイミングで吸・排気弁を開閉する機構
空気や混合気をシリンダーの中に吸入するための吸気弁、燃焼ガスをシリンダーの外に排出するための排気弁。それぞれをカムシャフトを使って適切なタイミングで開閉する機構を動弁機構と呼びます。今回は、代表的なシングルカムSOHC(Single Overhead Camshaft)方式と、ツインカムDOHC(Double Overhead Camshaft)方式を比較しながら、動弁機構の構造と役割について解説していきます。

カムシャフトの役割
SOHCとDOHCの違いを説明する前に、まずエンジンにおけるカムシャフトの役割についてです。
4ストロークエンジンでは、シリンダーの中をピストンが2往復する間に吸気、圧縮、燃焼、排気行程の4行程を行い、エンジンは2回転します。吸気行程では、吸気弁の開閉によって空気と燃料をシリンダー内に吸入し、排気行程では排気弁の開閉によって燃焼ガスをシリンダー外に排出します。
吸・排気弁を適切なタイミングで開閉する役目を担っているのがカムシャフトです。カムシャフトには、弁の開閉時期やリフトを実現するプロファイルをもつ卵の断面のような形状のカム山が、吸・排気弁の数だけ、配列されています。
このカムシャフトを、クランクが2回転する間に1回転するように、タイミングベルトまたはタイミングチェーンで連動させ、吸・排気弁を開閉します。
SOHCとDOHCの違い
カムシャフトの配置の違いによって、1つのカムシャフトで吸・排気弁を駆動させるSOHCと、吸・排気弁それぞれを1つのカムシャフトで駆動させるDOHCの2方式があります。また、弁を駆動する方式には、カムシャフトのカム山で直接弁を駆動させる直動式と、ロッカーアームやスイングアーム(小さなロッカーアーム)を使ってテコの原理で駆動させる方式があります。
SOHCは1本のカムシャフトをシリンダヘッドの中央に配置し、ロッカーアームを介して左右に配置された吸・排気弁を駆動させます。一方、DOHCでは吸・排気弁の直上にそれぞれのカムシャフトを配置して直接弁を駆動させるか、スイングアームを介して弁を駆動します。
現在は高出力化が可能な1気筒あたり4弁(吸気弁×2、排気弁×2)エンジンが標準的であり、それに対応しやすいDOHCエンジンが主流となっています。

DOHCとSOHCの得失
DOHCの最大のメリットは、燃焼室形状や弁挟み角(吸気弁と排気弁の軸がなす角度)などの設計自由度が高いことです。カムシャフトが吸・排気側にそれぞれ配置されるので、点火プラグが燃焼室中央に配置でき燃焼効率の向上に有利です。
また吸・排気弁の挟み角を大きくできるので、燃焼室がペントルーフ(屋根型)形状にできます。これによって、吸・排気弁径が大きくとれて出力向上につながります。
SOHCではシリンダヘッド中央にカムシャフトが配置されるため、点火プラグを燃焼室中央に配置するのは難しくなります。また、弁径を大きくするために吸・排気弁の挟み角を大きくすると、ロッカーアームのアームが長くなり、アームがたわみ弁開閉タイミングの精度が下がってしまいます。
これらの特徴を踏まえ、DOHCエンジンは、高回転・高出力エンジンと呼ばれています。一方、SOHCは部品点数が少なく、小型軽量で低コストです。またカムシャフトが少ない分、フリクションが小さく、燃費には有利です。
DOHCエンジンは、1990年頃までは高出力エンジンの代名詞として位置づけられていましたが、現在はごく一般的な標準エンジンになっています。SOHCとDOHCのどちらが優れているかという議論でなく、車のコンセプトや要求性能などによって、使い分けることが重要です。
■筒内流動とは
ディーゼルでは「スワール」、ガソリンでは「タンブル」
エンジンの燃焼効率を向上させるためには、シリンダー内の流動を強化することが重要です。ディーゼルエンジンでは「スワール」、ガソリンエンジンでは「タンブル」と呼ばれる旋回流を活用しています。スワールやタンブルを生成する狙いや生成手法について、解説していきます。
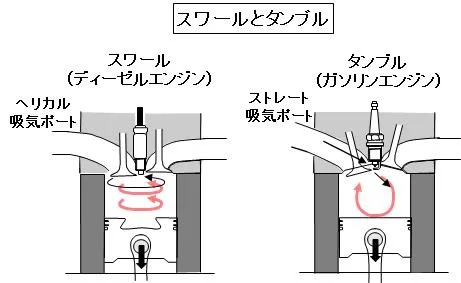
なぜ筒内(シリンダー内)流動は必要なのか
熱効率を向上するためには、できるだけ燃焼速度を速めて上死点付近で短時間に燃焼を完了させることが重要です。燃焼を速くするための効果的な手法が、シリンダー内の流動の強化です。シリンダー内の流動を強化すると、それに付随した小さなスケールの乱れが発生するため、燃焼が促進されます。
高速域ではピストンスピードが上がり自然に流動は増大するため、流動の強化よりも吸気量を増やすことに重点が置かれます。流動強化が必要なのは、燃焼速度が遅くなる低中速の部分負荷の運転領域です。
シリンダー内の流動としてはディーゼルエンジンで採用している水平方向旋回流のスワールと、ガソリンエンジンで採用しているシリンダー軸方向旋回流のタンブルがあります。
スワールの生成方法
ディーゼルエンジンは、ピストン上面に形成されたドーナツ型のキャビティ燃焼室に燃料を噴射しながら自着火する拡散燃焼です。したがって、ドーナツ型の燃焼室内に噴射燃料を収めて流動を確保するためには、水平方向のスワールが必須です。
スワールを生成するためには、吸入空気を吸気弁全周から均一にシリンダー内に流入するのではなく、流れに偏りを持たせる必要があります。一般的な生成手法としては、吸気ポート形状を渦巻き状にしたヘリカルポートを使う、吸気ポート内に流れを制御するスワールコントロール弁を装着する、吸気2弁エンジンであれば片弁を閉じるなどがあります。
タンブルの生成方法
かつてはガソリンエンジンもスワールを採用していました。しかし、1990年代から高出力化による4弁化が普及し、スワールよりも縦渦のタンブルの方が生成しやすいため、タンブルが採用されるようになりました。
タンブルは、吸気ポートをストレート形状にして、吸気ポートの上部から流入する空気量を増大させて生成させます。日産など、タンブルコントロール弁を吸気ポート内に装着している例もあります。基本的には、吸気ポート形状の最適化でタンブルを調整でき、スワールに比べて吸気量が減少しにくいメリットがあります。
タンブルは、4弁化とともに生まれた比較的新しい流動制御技術です。一方で、ディーゼルエンジンも4弁化が進みましたが、前述のようにドーナツ型の燃焼室内で燃焼を完結させるために、水平旋回流のスワールしか対応できないため、現在もスワールが採用されています。
スワール比とタンブル比
スワールとタンブルの強さの指標として、「スワール比」と「タンブル比」が使われています。スワール比とタンブル比は、ピストンが1往復する間に旋回流が何回転するかを表しています。例えば、スワール比2はピストンが吸気(ピストン下降)から圧縮(ピストン上昇)の間にスワールが2回転することを意味します。
吸気弁周りから流入する空気の流れに偏りを持たせるということは、吸入空気量を減らすことに他なりません。したがって、シリンダー内の流動強化と吸入空気量を増やすことは、トレードオフ関係にあります。目標とするスワール比あるいはタンブル比と吸入空気量が両立できる吸気ポート形状は、最近はCAE(熱流体解析)技術によって精度良く設計できます。
■摩擦損失とは
摩擦損失低減は燃費改善の手法のひとつ
いろいろな部品が作動しているエンジンでは、部品間に摩擦損失(フリクション)が発生します。燃費を改善する手法のひとつが、この摩擦損失を減少させる「フリクション(摩擦損失)低減技術」です。エンジンフリクションの構成要素や低減手法について、解説していきます。

エンンジンの熱収支
エンジンの仕事量は、燃料が燃焼して発生する熱量から、各種の損失(冷却損失、機械損失、ポンプ損失、排気損失、燃料の未燃損失)を差し引いた残りの熱量から引き出されます。ガソリンエンジンの場合、これらの損失は燃焼による発生熱量の60%以上に相当し、すべてが廃棄されます。したがって燃費を良くする、熱効率を向上させることは、これらの損失を減らすことに他なりません。
この中の機械損失「フリクション」は、主としてクランクシャフトやピストンなどの回転運動や往復運動時に発生する摩擦損失です。
フリクションの内訳
フリクションは、ピストンがシリンダー内で往復運動するときのピストンとシリンダー間、ピストンリングとシリンダー間の摩擦、クランクやコンロッド大端部が回転運動するときのコンロッドメタルやクランクメタルの摩擦、吸・排気弁を駆動させるカムシャフトや弁駆動のときの摩擦、クランクのカウンターウェイトがオイルに浸かって回転するときの摩擦、オルタネーターなどの補機可動部の摩擦などで発生します。
補機類のフリクションは、回転によらずほぼ一定です。動弁系のフリクションは、低速域でカム山を乗り越えるときの摩擦が大きく、高速になるほど十分に潤滑されるため、フリクションは低下していきます。その他の部品では、エンジンの回転が上がるほど、フリクションが周速に依存するため、増大します。

フリクション低減手法
フリクションを低減するためには、部品同士の摺動抵抗を減らす、ピストンなど軽量化によって慣性抵抗を減らす、オイルや水などの攪拌抵抗を減らす、補機駆動損失を減らすことなどが有効です。
・摺動抵抗の低減
ピストンスカート部形状の最適化や表面処理、カム表面の表面処理などの部品の接触面の改善や、ピストンリングの形状改良、張力低減、弁スプリング荷重の最適化、タイミングベルト張力の低減などの部品の接触力の低減、低粘度オイルの使用による摺動抵抗の低減などが効果的です。
・慣性抵抗の低減
効果的なのはピストンの軽量化です。ピストンが軽量化できればコンロッドとメタルも軽量化でき、さらにカムシャフトベアリングも小型化できるのでフリクション低減につながります。ただし、ピストンには燃焼で発生する熱を上手く逃がしたり、適正な強度や剛性が必要なので、安易な軽量化は禁物です。
・攪拌抵抗の低減
高速になると、オイルパンのオイル油面が上昇してクランクのカウンターウェイトがオイルに浸かり、大きな抵抗になる場合があります。そのためにも、十分な潤滑性能を確保した上でオイル量を減らすことが効果的です。
・補機駆動損失の低減
補機にはオルタネーター、水ポンプ、オイルポンプ、冷却ファン、パワーステアリングポンプ、エアコンコンプレッサーなどがあります。最近は、フリクション低減のため、条件によって駆動を制御する可変化機構などに加えて、電動水ポンプ、電動ファン、電動パワーステアリングなの電動化の採用例が増えています。
フリクション低減は、ひとつひとつの効果は小さくても「塵も積もれば」によって大きな効果となり、燃費改善にも大きく寄与します。部品点数を減らし部品同士の接触を極力避けた電動化技術も、フリクション低減技術と言えるかもしれません。
■フライホイールとは
車のレスポンスを左右する重要部品
フライホイールは、シンプルな構造ながらエンジンをスムーズに回すという基本的な役目を担いつつ、一方で車のレスポンスを左右する重要な部品です。

なぜフライホイールは必要なのか?
4ストロークエンジンでは、次の4つの行程で構成され、4行程でエンジンは2回転します。
・燃料と空気をシリンダに吸入する「吸気行程」
・吸入した混合気を圧縮する「圧縮行程」
・圧縮した混合気に点火して、燃焼(爆発)する「燃焼行程」
・燃焼ガスをシリンダから排出する「排気行程」
この中で、ピストンを押し下げエンジンを回すトルク(仕事)が発生するのは、燃焼行程だけです。残りの3行程は、仕事はせず惰性(慣性)で回ります。このような間欠的なトルクの発生が、回転中のトルク変動や回転速度変動を引き起こします。
フライホイールの原理
トルク変動の大きいエンジンをそのまま車に搭載すると、車はガタガタでアイドルが不安定になりエンストしやすくなります。これを防止するのが、フライホイールの役目です。
フライホイールはクランクシャフトの後端に付ける重い円盤です。燃焼行程で発生したトルクは、クランクシャフトを回す回転力になり、回転を維持しようとします。ところが、次の排気・吸気・圧縮行程は、自力で回転できないので回転速度は低下します。特に、アイドルのような低速条件では、回転の落ち込んでいる時間が長いため、エンストしやすくなります。
ここでフライホイールが機能を発揮します。フライホイールがクランクシャフトにつられて回ることによって、フライホイールの回転の勢い(慣性力)が、回転低下を防ぐように働き回転を維持します。
フライホイールは、ちょうどコマ(独楽)と同じような働きをします。コマは径が大きく外周部が重いほど、安定して回ります。フライホイールも同じで、エンジンをスムーズに回転させるためにはフライホイールの径は大きく、円周部が重い方が効果的です。
最適なフライホイールとは
フライホイールは、車が目標とする車両性能に応じて最適な設計をする必要があります。
慣性モーメントとエンジン回転速度の関係は、次のように表せます。
・回転させようとする力:エンジントルク(Nm) = 慣性モーメント(kgm2) × 角加速度(rad/sec2)
同一トルクで回転させる場合、慣性モーメントと角加速度(回転の上がりやすさ)は反比例の関係にあります。
フライホイールが重い(慣性モーメントが大)場合は、角加速度は小さくなりエンジン回転は安定します。言い換えると、レスポンスは悪化し、加速しづらく減速しづらくなります。逆にフライホイールを軽くするとレスポンスは良くなりますが、回転変動を抑えるという本来の効果が小さくなり、アイドルや低速時に回転が不安定になります。
モータースポーツに使うようなレース車輌ではレスポンスを重視して、できる限り軽量化を狙ったフライホイールを採用します。バランスを取りながら円盤に穴をあけたり、材質にクロームモリブデン鋼鉄やアルミ合金を使った軽量フライホイールが採用されています。
なおトルコン付きAT車では、トルコン自体が大きな慣性重量になりトルク変動を吸収するため、フライホイールは必要ありません。
エンジン技術が日々進化する中で、昔からずっと変わらない目立たない存在ですが、重要な役目を担っている貴重な部品です。
■バランサーシャフトとは
4気筒エンジンでは慣性2次振動が発生する
レシプロエンジンでは、ピストンの往復運動で発生する慣性力に起因する振動は避けられません。この振動を抑制するために一般的に採用されているのが「バランサーシャフト」です。最も一般的に採用されている4気筒エンジンのバランサーシャフトの原理と効果について、解説していきます。

エンジンの振動
最も一般的な直列4気筒エンジンでは、「慣性2次振動(エンジン回転数の2倍の周波数)」が発生します。2気筒ずつ対称的な動きをしてバランスが取れているようですが、実はピストンが下向きに動く速度より、上向きに動く速度の方がわずかに速いので、その差が振動を発生させます。
また、直列3気筒エンジンや直列5気筒エンジンなど奇数気筒エンジンでは、クランクシャフトの中央位置を中心にピストン配置を対称にできないので、エンジン自体を上下に揺する「慣性1次の偶力振動」が発生します。これが、奇数気筒数の振動が大きいと言われる要因となっています。
これらの振動を抑制するために、バランサーシャフトが採用されます。
バランサーシャフト
排気量2.0L以上の直列4気筒エンジンでは、バランサーシャフトが採用されます。ピストンが大きく(重く)慣性力が大きくなるため、2次振動が問題となるケースが多いためです。
日本では、1974年に三菱自動車が「サイレントシャフト」という名称で2気筒の軽自動車用エンジンに初めて採用し、翌年には4気筒エンジンにも採用しました。一対のサイレントシャフトをオイルポンプに連動して回転させ、振動を効果的に低減しました。その後、ポルシェなど欧州メーカーも採用し、現在はディーゼルエンジンを含めて2.0L以上の4気筒エンジンの多くは、サイレントシャフトに類似したバランサーシャフトを採用しています。
ただしバランサーシャフトは、クランクシャフトからタイミングベルトやチェーンを介して回転させるので、高速域で駆動ロスが発生します。最近は、駆動ロスを抑えたコンパクトなユニットタイプが主流になっています。
バランサーシャフトの原理
エンジンの2次慣性力は、ピストンの往復運動によって180度の周期で上下方向に働きます。4気筒エンジンの場合は、NO.1&NO.4とNO.2&NO.3の気筒が対称的な動きをします。しかし、ピストンが下向きに動く速度より上向きに動く速度の方がわずかに速いので、その差によって90度周期の2次振動が発生します。
バランサーシャフトは、アンバランスを付けた一対のバランサーシャフトをクランクシャフト回転数の2倍の速度で逆回転させます。このバランサーシャフトが発生する逆位相の起振力によって、2次慣性力をキャンセルします。一方で左右の慣性力は、一対のバランサーシャフトで互いにキャンセルします。
また、慣性1次偶力が発生する直列3気筒エンジンと5気筒エンジンでも、それをキャンセルするためにバランサーシャフトが採用される場合が多いです。
かつてホンダのF1エンジンにも、バランサーシャフトが採用されていました。不快な振動は、ドライバーの集中力を欠き、疲労が蓄積するためです。
最近の車は、上級志向が強く、乗り心地や振動騒音の軽減は商品力強化の重要なテーマです。バランサーシャフトだけでなく、エンジンマウントやクランクシャフトのダンパー機構、フライホイールなどで総合的にエンジンの振動騒音を低減しています。
(Mr.ソラン)
クリッカー自動車用語辞典 https://clicccar.com/glossary/