目次
■車のボディとは
車の基本骨格であるボディは、構成部位の中で最も大きく重く、車のサイズやデザイン、性格を決定付けます。
乗員を快適かつ安全に保護するために、強固でしなやかで軽量、さらに美しいフォルムを形作るボディの構造や要素、材質について、解説します。
ボディ形状の種類
車の形状を「1ボックス」、「2ボックス」、「3ボックス」と呼んで分類することがあります。これは、エンジンルームと乗員が乗るキャビン、荷物を載せるトランクの3要素が、いくつの箱(ボックス)で形成されているかを意味します。
1ボックスカーでは、エンジンとキャビン、トランクが一体となって箱型形状に収まっています。セダンは、エンジンルーム、キャビン、トランクが独立した空間をもつ3ボックスカーです。
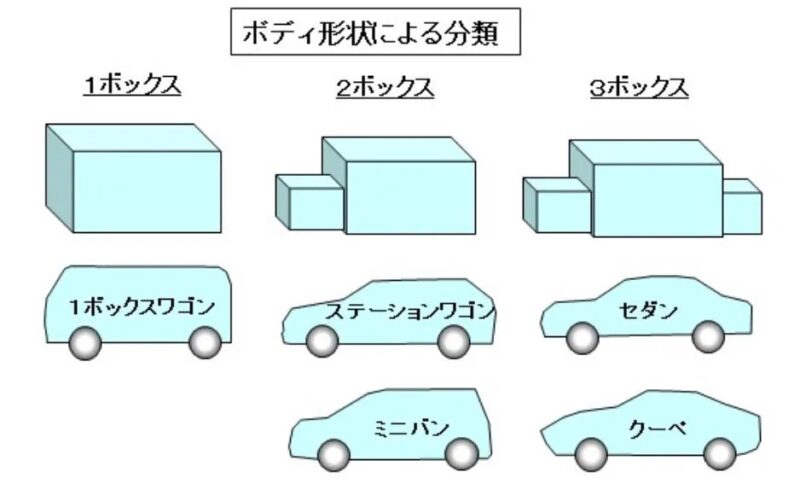
ボディの構造
車の構造は、「ラダーフレームボディ」と「モノコックボディ」に大別できます。
ラダーフレームは、例えばランクルやジムニーのようなオフロードSUVで採用されていますが、ほとんどの車はモノコックボディです。
ラダーフレームは、馬車の構造を起源とする昔からある基本的な構造です。
ハシゴ状のフレームの上に別に製造したボディを載せて、エンジンやサスペンションなど主要な部品はフレーム側に装着します。フレーム自体は、独立して強固ですが、重くて車内スペースが十分に確保できないという課題があります。
乗用車のほとんどが採用しているモノコックボディは、ボディとシャシーが一体の卵の殻のような構造です。
一体であるため、ボディ剛性が高く軽量で、車内スペースを確保できます。反面、すべての面で支え合っているので、衝撃が加わったときにボディ全体が大きくゆがみ、最悪の場合は走行困難になることがあります。
ラダーフレームとモノコックの中間的な「ビルトインラダーフレームモノコック」という構造もあります。
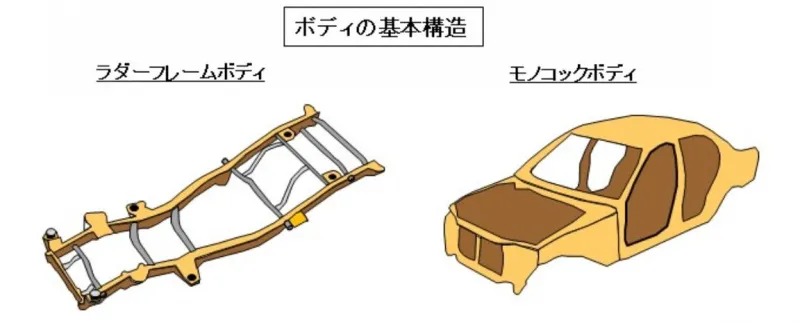
ボディの材質
ボディには、軽量化と衝突安全性の向上という、相反する課題に対応することが求められています。
現在は、低コストで加工性に優れ大量生産に向いている鋼板が主流ですが、適材適所で適切な材料を使うマルチマテリアル化や、軽量材料への置換による軽量化が進められています。ボディに限らず、鋼板は最も使用量が多く、車全体の40%(重量比)近くが使われています。
また、部位ごとの重量割合では、ボディが最も重くて車全体の30%程度あり、ボディ部材の軽量化が最大のターゲットになっています。
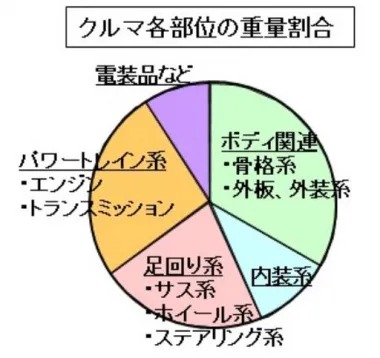
現在、積極的に採用されているのは、軽量で衝突エネルギー能力が高い高張力鋼板(ハイテン)です。最近は、980MPaや1180MPa、1470MPaの超高張力鋼板の採用が進んでいます。
また高張力鋼板と並行して、アルミ(鉄の1/3の比重)の採用も進んでいます。代表的なのは、ホンダ・NSXのアルミボディで、通常の鋼板に比べて40%の軽量化を実現しました。ただしアルミを使う場合、鋼板との異種接合部の強度を確保するための特別な技術が必要です。
現在最も注目されている材料は、CFRP(炭素繊維強化プラスチック)です。BMWのEV車「i3」は、ボディ上部をオールCFRP製として大幅な軽量化を実現しました。まだコストや生産性に課題はありますが、圧倒的な軽量と強度はボディにとっては大きなメリットであり、徐々に採用例が増えつつあります。
軽量化と衝突安全性向上という相反する課題の解決を担っているのは、ボディ技術の進化です。特にボディの軽量化が進めば、今後さらに厳しさを増す燃費規制へ大きく貢献できます。
本章では、ボディの基本構成や構造、材質などについて、詳細に解説していきます。
■車両の基本諸元とは
車のカタログには、エンジン諸元とともに、車両のさまざまな諸元が表示されています。車両諸元によって、車のサイズだけでなく、車の性格や性能などもある程度予想できます。
車両の代表的な基本諸元の意味とその特徴について、解説していきます。
自動車の寸法規格
道路運送車両法による3つの分類(軽自動車、5ナンバー小型車、3ナンバー普通車)は、下記のようにエンジン排気量と車の寸法(全長、全幅、高さ)で定義されています。下記の排気量と3つの寸法のうち一つでも規格を外れると、一つ格上のナンバープレートになります。
・軽自動車:排気量660cc以下、全長3.4m以下、全幅1.48m以下、高さ2.0m以下
・小型車(5ナンバー車):排気量2000cc以下、全長4.7m以下、全幅1.70m以下、高さ2.0m以下
・普通車(3ナンバー車):排気量2000cc超、全長12.0m以下、全幅2.50m以下、高さ3.8m以下
※5ナンバーの条件にある排気量はガソリン車のみの設定であり、ディーゼル車には排気量の制限はありません。
以上の3つの分類によって、税金や保険料、車検費用が異なります。
ボディの大きさと特徴
車の大きさは、ボディ寸法の全長と全幅、高さで表されます。その他車の性格を左右する寸法としては、ホイールベースやトレッド、オーバーハング、最低地上高などがあります。
それぞれについて、以下で解説していきます。
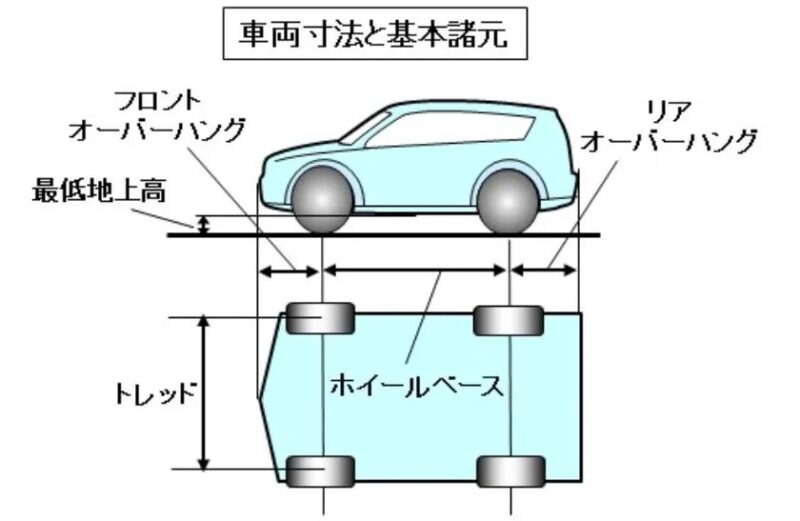
ホイールベース/トレッド
ホイールベース(前後車輪の中心間距離)とトレッド(左右のタイヤ幅の中心間距離)は、両者の相対的な大きさが車両性能を大きく左右する重要な要素です。ホイールベースの長い車は、直進安定性に優れてピッチングに強くなります。トレッドが広いと、旋回性能に優れローリングが抑えられます。
規格内で設定されるホイールベースとトレッド、両者の比率によって、車の運動性や性格が特徴づけられます。
オーバーハング
オーバーハングとは、前輪の車軸中心から最前端部までの距離(フロントオーバーハング)、または後輪の車軸中心から最後端部までの距離(リアオーバーハング)です。車の前後端に重量を持つため運動性能に影響を与え、衝突の際には潰れて衝撃を吸収するクラッシャブルゾーンの役目があります。
最近の車は、室内空間を確保するためにホイールベースを長くとり、車体全体をコンパクトにするため前後のオーバーハングを短くする傾向があります。ショート・オーバーハングにすることによって、前後端の重量が小さくなり、小気味よい操縦性が実現されます。
最低地上高
最低地上高とは、水平な地上面から車の最も低い部位までの垂直距離で、保安基準で90mm以上あることが規定されています。
悪路や凹凸が大きな路面を積極的に走行する4WDやSUVなどでは、車の底面を守るために最低地上高は高く、空力やスタイリングを重視するスポーツ車などは低く設定します。
車室空間
車室空間をどのように確保するかによって、ボディ形状は左右されます。性能を重視すれば、ドライバーはできるだけ車の中央付近に配置することが望ましいですが、車室空間を広くするためには、ドライバーの位置は前方に配置されます。
小型乗用車では、できるだけ広い車室空間を確保するために、ホイールベースを大きくする、エンジンルームをコンパクトにするなどの工夫をしています。
車やエンジンの性能や機能などを気にする人は多いですが、具体的な寸法などの諸元値を見る人、理解できる人は少ないのではないでしょうか。
上記のような諸元値の意味するところを理解すれば、車の違いが楽しめ、車を選ぶときに役立ちます。
■車体の構造とは
現在ボディ構造として採用されているのは、一部のオフロード用SUVに採用されているラダーフレーム構造と、その他ほとんどの車で採用されているモノコック構造です。
ラダーフレームとモノコックの構造と特徴について、解説していきます。
ボディ構造の種類
車の構造は、「ラダーフレームボディ」と「モノコックボディ」の2種に大別されます。ラダーフレームは、ランクルやジムニーのようなオフロードSUVで採用されていますが、ほとんどの車はモノコックです。
ラダーフレーム構造は、フレームが骨格として体を支えているので人間や動物に、モノコック構造は、外側の硬い殻で体そのものを支えている昆虫や甲殻類に例えられます。
ラダーフレームボディ
ラダーフレームは、馬車の構造を起源とした昔からある基本的な構造です。ハシゴ状のフレームの上に別に製造したボディを載せて、エンジンやサスペンションなど主要な部品はフレーム側に搭載します。ボディが歪んでもフレームさえ無事ならば、問題なく走行できる強みがあるので、トヨタ・ランドクルーザーやスズキ・ジムニーなど、一部の本格オフロード車に採用されています。
フレーム自体は、独立して頑強ですが、重くて車内スペースが十分に確保できないという課題があります。
モノコックボディ
乗用車のほとんどが採用しているモノコックボディは、ボディとシャシーが一体の卵の殻のような構造です。プレスで成形した1~2mm程度の鋼板を重ねた部分をスポット溶接でつなぎ合わせて、箱型に組み立てています。一体構造なためボディ剛性が高く軽量で、しかも車内スペースを確保でき、乗り心地も良好です。
一方で、すべての面で支え合っているので、衝撃が加わったときにボディ全体が歪み易く、最悪の場合は走行困難になることがあります。
ラダーフレームとモノコックの中間的な「ビルトインラダーフレームモノコック」という構造もあります。フレームとボディを溶接して一体化したフレームレスボディです。フレームの頑強さとモノコックの長所を取り込むことをねらっており、三菱・パジェロやレンジローバーなどが採用しています。
衝撃吸収ボディ
単純にボディを強固にすれば、乗員の安全が確保されるというわけではありません。
最近の車は、衝突時に車室前後のクラッシャブルゾーンを変形させて衝撃を吸収し、車室の変形を抑えることによって、乗員の安全を確保します。具体的には、車室周りの強度を上げて、エンジンルームやトランクは柔らかくしておくことで衝撃を吸収します。
衝突安全ボディは、トヨタではGOA(グローバル・アウトスタンディング・アセスメント)、日産ではゾーンボディと呼んでいます。
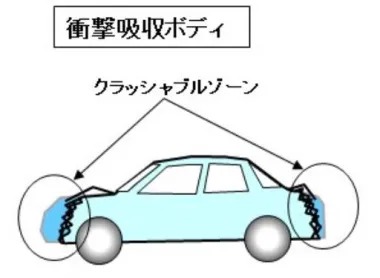
プラットフォームの統一・共用化
プラットフォームは、モノコック構造のボディや外板を除いたシャシー部分を指します。
近年自動車メーカーは、プラットフォームの統一・共用化を積極的に進めています。例えば、トヨタはTNGA(トヨタ・ニュー・グローバル・アーキテクチャー)、日産はCMF(コモン・モジュール・ファミリー)という統一コンセプトによって推進しています。
狙いは、生産基準の統一による生産設備の投資抑制や生産性向上、さらに共用構造による開発費の抑制です。同じプラットフォームでも、ホイールベースやサスペンションなどの設定変更によって、車のスタイルや性格を変えて対応します。
ボディ構造は、軽量でありながら剛性が高いフレームレスのモノコック構造が主流ですが、実際には状況に応じて前後方向や横方向にはメンバーを追加しています。剛性を強化する目的とともに、潰れない部位と潰れる部位をコントロールする役目をしています。
■車体の材質とは
ボディの材質は、軽量化と衝突安全性向上という相反する課題を解決するため、通常の鋼板から高張力鋼板やアルミ、さらにCFRP(炭素繊維強化プラスチック)へと軽量化材料の使用拡大が進んでいます。
それぞれの材質のメリットと課題、今後の材質の方向性について、解説していきます。
ボディ重量の推移
車の重量は燃費に大きく影響し、車体重量が100kg低減すると燃費は1km/L向上すると言われています。中でもボディの重量は、車全体の30%程度を占め、ボディ部材の軽量化が最大のターゲットになっています。
材料としては、ボディに限らず鋼板の使用量が最も多く、車全体の40%(重量比)近くが使われています。低コストで加工性に優れ、大量生産に向いていることが採用の理由です。
現在は、ボディの最大の課題である軽量化と衝突安全性向上を両立させるため、適材適所で適切な材料を使うマルチマテリアル化や軽量材料への置換が、積極的に進められています。
高張力鋼板
現在採用が進んでいるのは、軽量で衝突エネルギー能力が高い高張力鋼板(ハイテン)です。高張力鋼板は、比較的大きな応力がかかる部分で使われ、最近は980MPaや1180MPa、1470MPaの超高張力鋼板の採用例も増えています。
高張力鋼板は、Mn(マンガン)などの合金成分を添加して、熱処理などで材料組織の制御を行い、通常の鋼板よりも強度を向上させた鋼材です。コストは鋼板よりも高いですが、アルミよりは安く、補修やリサイクルが容易という特徴もあります。
アルミニウム
高張力鋼板と並行して、アルミ(鉄の1/3の比重)の採用も進んでいます。軽量ですが強度も1/3程度なので、鋼板と同じ構造では強度不足になるため、形状や構成には特別な技術が必要です。
フロントフードやルーフ、フェンダーなどへのアルミの採用例は見られますが、代表的なのは初代ホンダ NSX(1990年~)のアルミボディで、通常の鋼板に比べて40%の軽量化を実現しました。
アルミを使う場合、鋼板との異種接合部の強度を確保するための特別な技術が必要です。鋼板同士の接合はスポット溶接が主流ですが、アルミの場合には電気伝導や熱伝導が異なるため、スポット溶接の代わりにレーザー溶接やMIG溶接、リベット止めが採用されます。
ボディの溶接法
スポット溶接は、溶接する2枚の鋼板を電極で挟み、電気抵抗による発熱で鋼板を溶かして溶接します。レーザー溶接は、レーザーを集光した熱で鋼板を溶かして溶接します。スポット溶接のような点でなく、線溶接ができることが最大の利点です。
MIG溶接は、放電を利用するアーク溶接の一種で、シールドガスに不活性ガスを用います。ステンレスやアルミの接合に用いられます。
CFRP
最も注目されている材料は、CFRP(炭素繊維強化プラスチック)です。航空機では、すでに機体の半分はCFRPを使っています。比重は1.6(アルミ2.7)、強度はアルミの5倍程度と高く、軽量化材料としては圧倒的に優れています。
トヨタ・レクサスLFAは、前後フードとルーフにCFRPを使い、CFRP65%/アルミ35%のボディを実現しました。またBMWのEV「i3」は、ボディのキャビンをオールCFRPとして大幅な軽量化を実現しました。
まだコストや生産性に課題はありますが、徐々に採用例が増えつつあります。
燃費向上だけでなく、加速性能、ブレーキ性能、旋回性能など、走行性能全般のレベルアップに最も効果的なのが、車の軽量化です。一方で、軽量化と相反する衝突安全性の向上をどのように両立させるかが、最大の課題です。
特にマルチマテリアル化や材料置換など、材料の技術革新に期待するところが大です。
■CFRP(炭素繊維強化プラスチック)とは
軽くて強い、車にとって理想的な軽量化材料は、CFRP(炭素繊維強化プラスチック)です。コストと生産性に課題はあるものの、徐々に適用例は増え、ボディの大部分にCFRPを使った車も出現しています。
最も注目されている材料CFRPについて、解説していきます。
CFRPの特徴
CFRPは、樹脂に強化材として炭素繊維を混ぜた炭素繊維強化プラスチックです。高価ですが、軽くて強い、硬くて寸法精度が高いなどの特徴から、航空機はもとより車への適用が進んでいます。
CFRPの比重は約1.8で鋼(比重7.8)の約1/4に相当し、強度(引張強度/比重)は鋼の約10倍です。
NEDO(新エネルギー・産業技術総合開発機構)の試算によると、ボディフレームやフードなどにCFRPを適用すれば、1380kgの車両が410kgも減らせる、約30%の軽量化が実現できるとのことです。これだけ軽量化できれば、燃費は22.5%低減できます。
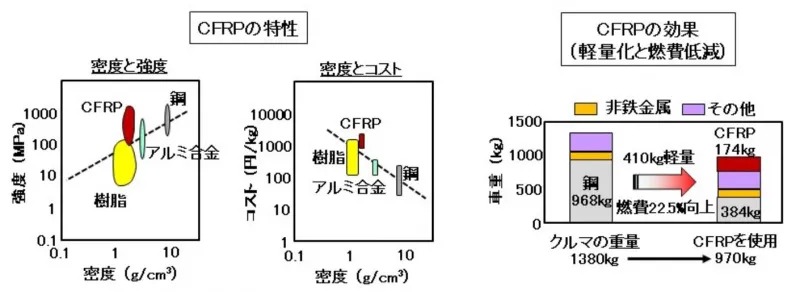
CFRPの課題
最大の課題は、コストと生産性です。CFRPのコストは、2017年時点で1500~7000円/kgで、鋼の10倍です。
一般的なのは、航空機のフレームなどに使われる、エポキシ樹脂などの熱硬化樹脂に炭素繊維を混ぜて造る熱硬化性CFRPです。ただし、これは高温高圧の圧力釜、オートクレーブを使って成形するため、加工終了まで2~4時間かかり、車のような大量生産には向きません。
車用として開発が進められているのは、熱可塑性樹脂を使うCFRPです。CFRTP(炭素繊維強化熱可塑性樹脂)と呼ばれ、熱硬化性CFRPよりも成形時間を大幅に短縮でき、大物ブレスの成形でも数分以内、小物部品であれば30秒以内で成形できます。
これなら大量生産も可能なので、車用として開発が加速され、採用も徐々に増えています。
CFRPの適用例
CFRPは、すでにいろいろな部品に採用されています。例えば、ボンネットフード、リアスポイラー、プロペラシャフトなどです。
・ボンネットフード
ボンネットフードに世界で初めて採用したのは、日産・スカイラインGT-R(R34型Vスペック)です。アルミ製に対して 30%の軽量化を実現しました。参考値ですが、ボンネットフードの重さはCFRP製で8kg、アルミ製で12kg、鋼板で20kgです。
・プロペラシャフト
三菱・3代目パジェロ(1999年~)や日産フェアレディZ(Z33、Z34型)、GT-R(R34型)などで採用しています。高い剛性によって中間軸も省けて、部品全体で50%の軽量化が達成できています。さらに、静粛性や走行性能の向上にも寄与しています。
・バックドア
2代目プリウスPHV(2016年~)で採用し、アルミに比べて40%の軽量化を実現しています。
CFRP適用車
車両のボディ構造に積極的にCFRPを採用した例としては、スポーツタイプのトヨタ・レクサスLFAと電気自動車のBMW i3があります。
トヨタ・レクサスLFAは、前後フードとルーフにCFRPを使い、ボディをCFRP65%/アルミ35%の比率で構成しています。BMW i3は、大量のリチウムイオン電池搭載による車重増加をキャンセルするため、量産車としては異例に多い100kg程度のCFRPを使ってボディのキャビンを構成しています。
CFRPは、航空機やレーシングカーへの採用から、一般量産車への適用が加速しています。その背景には、電動化や安全技術の装備などによる車全体の重量増加と、厳しさを増す燃費規制があります。
課題のコストと生産性は直接リンクしており、生産性が上がれば採用しやすくなり、使用量が増えればコストも下がります。より一般的な材料となるには、熱硬化性CFRPの弱点が克服できる熱可塑性CFRTPの進化が、今後のカギと言えます。
■構造用接着剤とは
車は、スポット溶接と構造用接着剤を併用して、剛性を高めるようにしています。一方で、接着剤を補助的な用途でなく、CFRPのような新材料の接合技術のために、より積極的に使用する動きがあります。
最近の構造用接着剤の動向について、解説していきます。
鋼板の接着法
鋼板の構造用接着剤の一般的な使い方は、スポット溶接と併用して剛性を高めるウェルボンド工法です。スポット溶接だけでは、機能上の理由からスポット数や接合部位に制約があるため、十分なボディ剛性を確保できません。
ウェルボンド工法では、スポット溶接の点接合部に構造用エポキシ系接着剤を併用します。点接合から面接合となることによって、ボディが捻じれにくく、剛性が向上します。その結果、補強板の使用や鋼板を厚くする必要がなくなり、ボディ剛性を確保しつつ、軽量化を図ることができます。
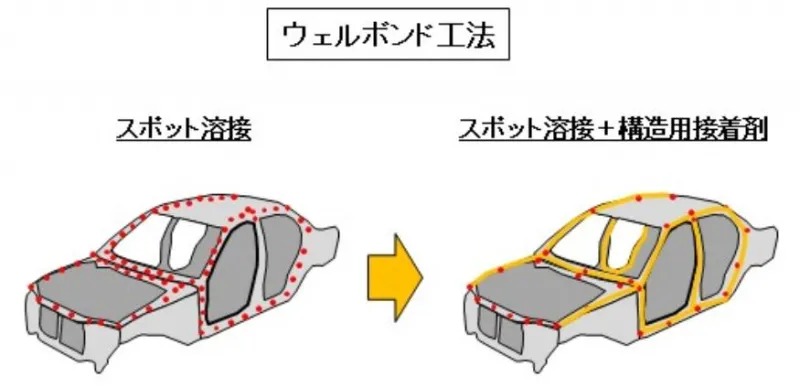
マルチマテリアル構造の接着法
ボディの軽量化については、日本よりドイツメーカーの方が積極的に取り組んでいます。特に、アルミや樹脂など異種材料を使い分けるマルチマテリアル構造とCFRP(炭素繊維強化プラスチック)などの採用が進んでいます。
マルチマテリアル構造は、鋼板とともにアルミや樹脂など異なる材料を適材適所で使い分けて、軽量化を図る手法です。異種材料を接合するためには、接着剤が必要であり、マルチマテリアルを推進しているドイツを中心に、構造用の接着技術が飛躍的に進んでいます。それぞれ異なる熱膨張係数の異種材料を強固に接合するためには、発生する熱応力差を吸収する接着剤が求められます。
CFRPの接着法
CFRPは軽くて強く、寸法精度が高いなどの理由から、ボディ軽量化の切り札として注目されています。ドイツメーカーが構造用接着剤を積極的に開発し採用する背景には、CFRPによって車の軽量化を進め、燃費向上を図るという戦略があります。言い換えると、機能的に優れた接着剤がなければ、CFRPボディは成立しないということです。
低燃費戦略に関する日本とドイツの違いは、日本がHEVのようなエンジン改良と電動化技術を軸に推進しているのに対して、ドイツは車体の軽量化技術、例えばマルチマテリアル化やCFRP化に注力している点です。結果として、エンジンと電動化技術では日本メーカーが、軽量化技術ではドイツメーカーが先行しています。
構造用接着剤の種類
現在、構造用接着剤として採用が進んでいるのは、ウレタン系接着剤とエポキシ系接着剤です。
ウレタン系接着剤は、性能はやや劣りますが、室温でも短時間で硬化して接合できるため、ドイツメーカーは積極的に採用しています。すでにBMWやダイムラー、アウディの軽量化ボディには採用されており、電気自動車BMW i3のCFRPのボディキャビンの接合は、ウレタン系接着剤を使っています。
日本では、エポキシ系接着剤を用いた接着が採用されています。エポキシ系接着剤の方がウレタン系よりも、信頼性を含めて総合的には優れていますが、硬化のコントロールが難しいという課題があります。トヨタのレクサス LFAでは、CFRPキャビンの接合に、エポキシ系接着剤とブラインドリベットを併用しています。
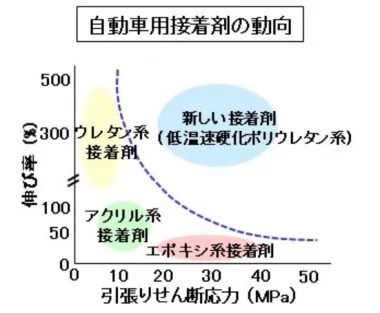
ボディの結合については、燃費規制のための軽量化を背景に、溶接から接着への流れが急速に進んでいます。
■ボディ形状と空力特性とは
車のデザインは、見た目のカッコ良さだけでなく、空力的に優れたスタイルであることが重要です。空気抵抗が大きければ、エンジン出力が十分に生かせず走行性能も燃費性能も悪化します。
ボディの形状と空力的な要素について、解説していきます。
車の空気抵抗
車の空気抵抗とは、車が走行するときに進行を妨げるような逆向きの空気の抵抗で、ボディ表面の空気との摩擦によって発生し、以下の式で表されます。
空気抵抗 = 1/2 x Cd × (空気密度) × (前面投影面積) × (車速)2
Cd(空気抵抗係数)と前面投影面積については、あとで詳しく説明しますが、いずれも車のスタイルやサイズに大きく影響されます。簡単に言えば、空気抵抗を小さくするためには、ボディ形状をコンパクトにして空気の流れをスムーズにすることが重要です。
また、空気抵抗が車速の二乗に比例することから、高速になればなるほど空気抵抗が大きくなります。高速性能や高速燃費に空気抵抗が大きく影響することを意味します。
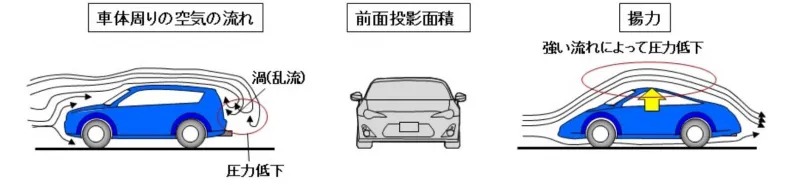
空気抵抗係数Cd
Cdは、走行している車を逆方向に戻そうとする力の指標で、車体に沿った空気の流れやすさを示し、数値が小さいほど空気抵抗は小さくなります。
車が走行すると、車体前面に衝突した空気は車の外周に沿って流れ、車体後部では渦が発生します。渦が発生する車体後部は負圧状態になり、一方、空気が衝突する車体前面は圧力が高くなるので、車体には後ろに引っ張られる空気抵抗が発生します。
Cd値を小さくするには、流れをスムーズにする流線型のボディ形状が効果的です。実際には、乗員スペース、居住性を確保する必要があるので、流星型ボディという訳にはいきません。
Cd値の例
飛行機の翼のCd値は0.1程度、立て板が1.25で、最近のCd値の低い乗用車は0.25~0.3、背の高いSUVやワンボックスカーは0.3~0.4程度です。ちなみに、トヨタ4代目プリウスは0.24、日産GT-R(R35型)が0.26です。
前面投影面積
前面投影面積は、車を前から見たときの面積を表します。当然、面積が小さいほど空気抵抗は小さくなります。Cd値が同じでも投影面積が大きければ、その分、走行性能や燃費性能は劣ってしまいます。
別の見方をすると、前面投影面積が大きいからただ単に良くないということではなく、乗員スペースの大小を表しているとも言えます。すなわち、前面投影面積は車の性格や用途の指標であると考えることができます。
風洞試験
Cdのような空力特性の評価は、風洞試験で行います。風洞試験装置とは、車を固定して空気を流すことで、走行中の空気の流れを解析する装置です。ボディ周辺の流れを可視化する場合は、トレーサーとして煙を空気とともに流して、煙の流れ方で車体周りの空気の流れを解析します。最近は、タイヤも回転させるムービングベルト方式が一般的です。
揚力係数CL
Cdを限りなく小さくすると、飛行機の翼のような形状になりますが、こうなると飛行機のように車を持ち上げる力、揚力が発生します。この特性を表す数値を、揚力係数CLで表します。高速になると、ボディ上部を流れる空気の速度が下部よりも速くなり、圧力が下がることによって、揚力が発生します。
揚力が発生すると、タイヤの接地力が低下し、操縦安定性や直進安定性が悪化します。レーシングカーやスポーツ車ではCdを低減しながら、一方で揚力を抑制するエアロパーツであるリアスポイラーやエアダムスカートを装着しています。
高速燃費を改善するために、Cdの小さいボディ形状を検討することは常套手段ですが、相反するのは乗員の車内スペースです。
限られたサイズの中で居住空間を確保しながら、空力特性の優れた魅力的なスタイルを実現することが、ボディ形状に求められています。
(Mr.ソラン)
クリッカー自動車用語辞典 https://clicccar.com/glossary/